What materials can be cut with a die cutting machine? | Keshenglong&Shinko Expert Guide
This guide for flexo printers dives into the capabilities of die-cutting machines across a spectrum of materials. Learn about common substrates like self-adhesive labels and paperboard, the nuances of cutting challenging thin films and heavy corrugated, and how material thickness influences precision. We explore specialized considerations for adhesive and multi-layered materials, plus recent innovations expanding die-cutting versatility. Understand key factors for machine selection and the advantages of Keshenglong and Shinko solutions for your re-purchase needs, ensuring optimal production efficiency and quality.
- What Materials Can Be Cut with a Die Cutting Machine? A Guide for Flexo Printers
- What are the Core Materials Flexo Printers Die-Cut Daily?
- Can Die-Cutters Handle Challenging Substrates Like Thin Films or Heavy Corrugated?
- How Does Material Thickness Impact Die-Cutting Precision and Machine Selection?
- What Special Considerations Apply to Cutting Adhesive and Multi-Layered Materials?
- What Innovations in Die-Cutting Technology Expand Material Capabilities?
What Materials Can Be Cut with a Die Cutting Machine? A Guide for Flexo Printers
For flexo printers, the efficiency and versatility of your die-cutting machinery are paramount. As you consider re-purchasing or upgrading, understanding the full spectrum of materials your machines can handle—and the nuances involved—is crucial. Die-cutting is a precision process, and the right machine combined with the correct tooling can transform raw materials into complex, high-value products.
What are the Core Materials Flexo Printers Die-Cut Daily?
Flexo printers primarily operate in the label, flexible packaging, and folding carton sectors, meaning their die-cutting needs revolve around a core set of materials:
- Self-Adhesive Label Stock: This is perhaps the most common, encompassing paper (gloss, matte, thermal), synthetic films (BOPP, PE, PET, PVC, often 40-150 microns thick), and specialty materials like metallized or clear films. Die-cutting for labels involves both through-cutting and 'kiss-cutting' (cutting the face material without cutting the liner).
- Paperboard and Cardboard: For folding cartons, blister cards, and tags, flexo printers commonly cut paperboard ranging from 180 GSM to 500 GSM (approx. 0.2mm to 0.7mm thick). Rotary die-cutting is efficient for continuous forms, while flatbed die-cutting offers versatility for thicker, larger formats.
- Flexible Packaging Films: Materials like BOPP, PET, PE, and various laminates (often 12-50 microns per layer) are die-cut for pouches, sachets, and wrappers. Precision is key to maintain barrier properties and seal integrity.
- Specialty Papers: Including thermal papers, synthetic papers, and sometimes even thin foils or laminates for unique applications.
Can Die-Cutters Handle Challenging Substrates Like Thin Films or Heavy Corrugated?
Yes, modern die-cutting machines, especially those integrated with flexo lines, are engineered to handle a broad range of challenging materials, but with specific considerations:
- Ultra-Thin Films: Films as thin as 12-20 microns (e.g., some BOPP or PET films used in flexible packaging) can be precisely die-cut. This requires extremely sharp, high-tolerance rotary dies, minimal cutting gaps, and precise pressure control to prevent tearing or stretching. Vacuum assistance or specialized web tension systems might be employed.
- Heavy Corrugated Board: While less common on integrated flexo presses for labels, dedicated corrugated converting lines (often featuring flexo printing) regularly die-cut heavy corrugated boards (e.g., E, B, C, A flutes, 1mm-7mm thick). This typically employs robust rotary die-cutters or flatbed die-cutters that exert significant force, often using steel rule dies or solid rotary dies designed for thick, fibrous materials.
- Multi-Layer Laminates: The complexity increases with materials like pharmaceutical blister packs or multi-layer food packaging, which can combine paper, film, and foil. Specialized dies and controlled pressure are vital to cut specific layers cleanly without compromising others.
How Does Material Thickness Impact Die-Cutting Precision and Machine Selection?
Material thickness is a critical factor influencing die design, machine robustnes, and cutting accuracy:
- Die Design: Thicker materials require taller, stronger cutting rules (for steel rule dies) or deeper, more aggressive blade profiles (for rotary dies) to ensure complete severance. The 'bevel' or angle of the cutting edge must be optimized for the specific material thickness.
- Machine Robustness and Stability: Cutting thicker materials demands more force, which necessitates a more rigid and powerful die-cutting machine. Machines designed for thin films may lack the necessary structural integrity or drive power for heavy cardstock. Conversely, a machine optimized for thick materials might struggle with the finesse required for kiss-cutting thin labels.
- Cutting Gap and Pressure Control: Maintaining consistent cutting depth across the web is crucial, especially for kiss-cutting. Variations in material thickness can lead to uneven cuts. Modern machines feature micro-gap adjustments and precise pressure control systems to compensate for slight variations and ensure uniform cutting. For example, a cutting gap of 0.05-0.1mm is often required for precise kiss-cutting of common label stocks.
What Special Considerations Apply to Cutting Adhesive and Multi-Layered Materials?
Cutting self-adhesive label stock and other multi-layered laminates presents unique challenges:
- Adhesive Residue: Adhesives can stick to dies, causing build-up, incomplete cuts, and reduced die life. Solutions include dies with non-stick coatings (e.g., Teflon-based), specific die materials (e.g., polished carbide), and sometimes even heating or cooling elements within the die to manage adhesive viscosity.
- Kiss-Cutting Precision: For self-adhesive labels, the challenge is to cut the face stock cleanly while leaving the silicone-coated release liner intact. This requires incredibly precise depth control, often within microns. Rotary dies with adjustable bearers or magnetic cylinders holding flexible dies are commonly used to achieve this accuracy, with tolerances often needing to be tighter than ±0.025 mm.
- Liner Release: Ensuring the matrix (waste material around the label) peels away cleanly from the liner without tearing or leaving adhesive residue is vital for high-speed production. Proper die design, cutting pressure, and web tension management are key.
- Multi-Layer Delamination: When cutting complex laminates, there's a risk of delamination between layers if the cutting force is not evenly distributed or if the material's bond strength is compromised by the cutting process.
What Innovations in Die-Cutting Technology Expand Material Capabilities?
The die-cutting industry is continuously evolving, driven by demands for greater versatility, efficiency, and precision:
- Advanced Die Materials & Coatings: The development of new steel alloys, carbide-tipped dies, and specialized non-stick or low-friction coatings enhances die life and performance on abrasive, sticky, or difficult-to-cut materials. This extends the range of materials that can be efficiently processed.
- Digital Die-Cutting: For short runs, prototyping, or highly intricate designs, digital die-cutting (e.g., laser cutting, plotter cutting) offers immense flexibility. Laser cutters can process materials like films, foams, and some plastics without physical dies, eliminating tooling costs and setup time. While slower than conventional rotary for long runs, they excel in handling varied materials with complex geometries.
- Servo-Driven Systems: Modern die-cutting machines often incorporate servo motors for precise control over cutting pressure, web tension, and registration. This allows for superior accuracy and consistency when working with a wide array of materials, from elastic films to rigid boards.
- Magnetic Die Cylinders and Flexible Dies: These innovations have revolutionized label printing, allowing for rapid job changeovers and cost-effective tooling. Flexible dies, being thinner and lighter, are easier to handle and store, and can be customized for a vast range of label shapes and materials, offering high precision at high speeds.
- Integrated Automation: Features like automatic matrix stripping, waste removal systems, and inline inspection help manage a wider range of materials by ensuring consistent quality and minimizing manual intervention.
Keshenglong & Shinko: Your Partners in Die-Cutting Excellence
When considering your next die-cutting machine purchase, partnering with reputable manufacturers like Keshenglong and Shinko offers distinct advantages:
- Keshenglong: Known for their robust and high-precision flexographic printing and converting solutions, Keshenglong machines integrate state-of-the-art rotary die-cutting units. Their systems are designed for high-speed, continuous production of labels and flexible packaging, ensuring exceptional accuracy and clean cuts across a wide array of filmic and paper-based substrates. Investing in Keshenglong means benefiting from reliable performance, minimal downtime, and a seamless workflow from print to finish, critical for high-volume flexo operations.
- Shinko: With a strong legacy in corrugated converting machinery, Shinko offers heavy-duty die-cutting capabilities optimized for demanding packaging materials. While often associated with post-print finishing of corrugated board, their expertise extends to robust and precise cutting for thicker paperboards and specialized packaging. Shinko machines are engineered for durability and consistent performance under high stress, providing the power and accuracy needed for large-format, challenging die-cutting applications, ensuring that even your toughest materials are processed with precision and reliability.
Both brands deliver solutions that meet the evolving demands of the printing and packaging industry, ensuring your investment enhances your material processing capabilities and overall operational efficiency.
Recommended for you
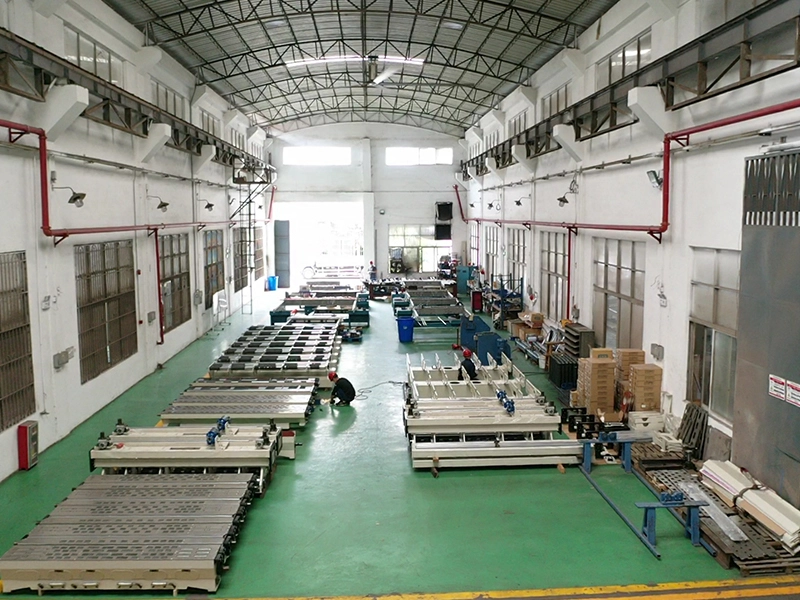
5 Common Flexo Folder Gluer Problems and Expert Solutions
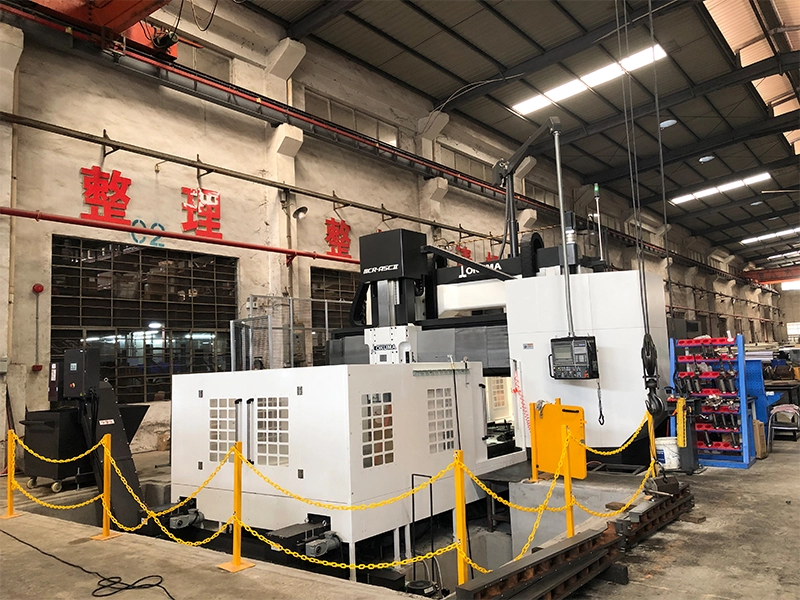
Flexo Folder Gluer Explained: Your Expert Guide
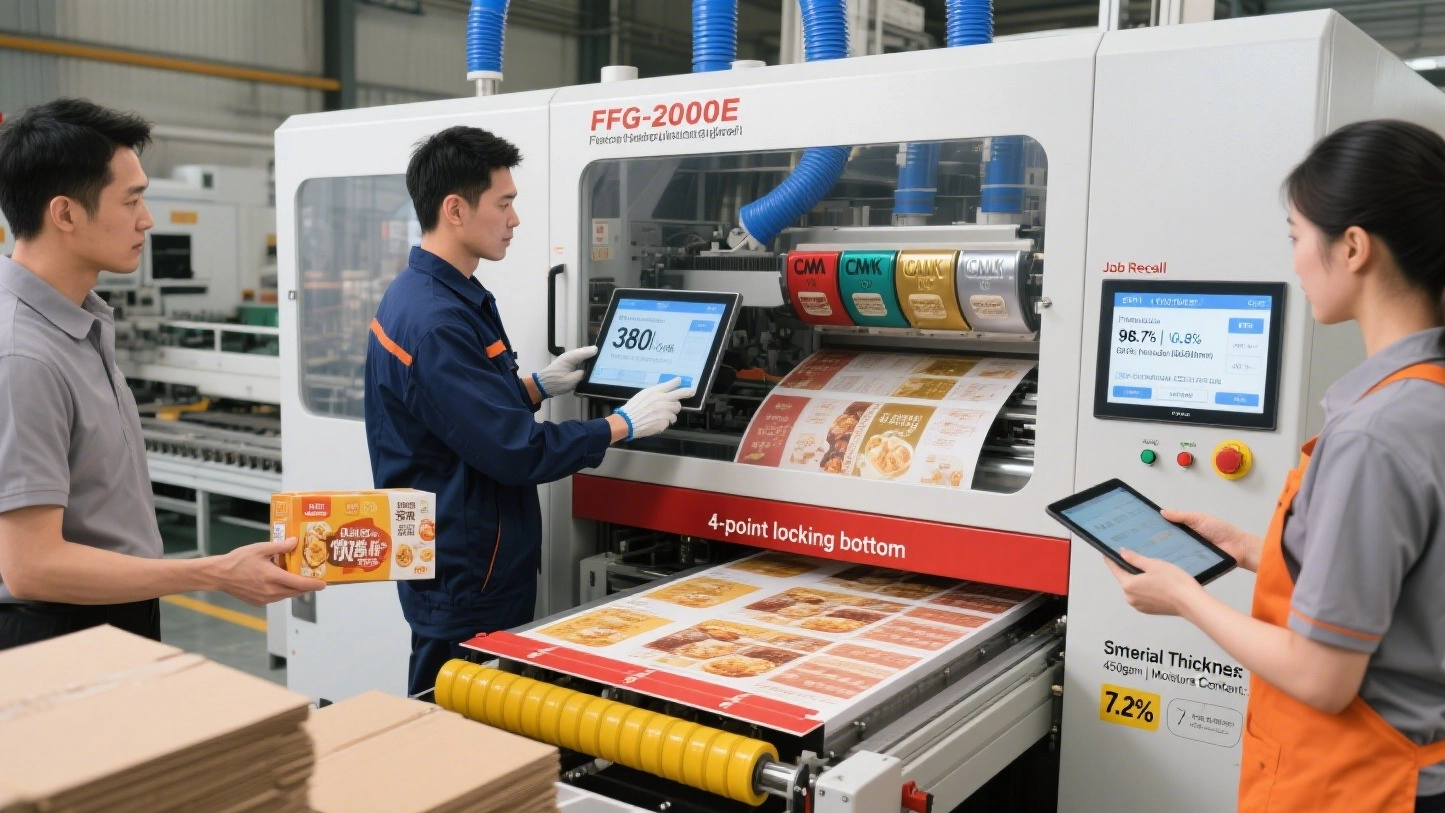
How to Operate a Flexo Folder Gluer Efficiently
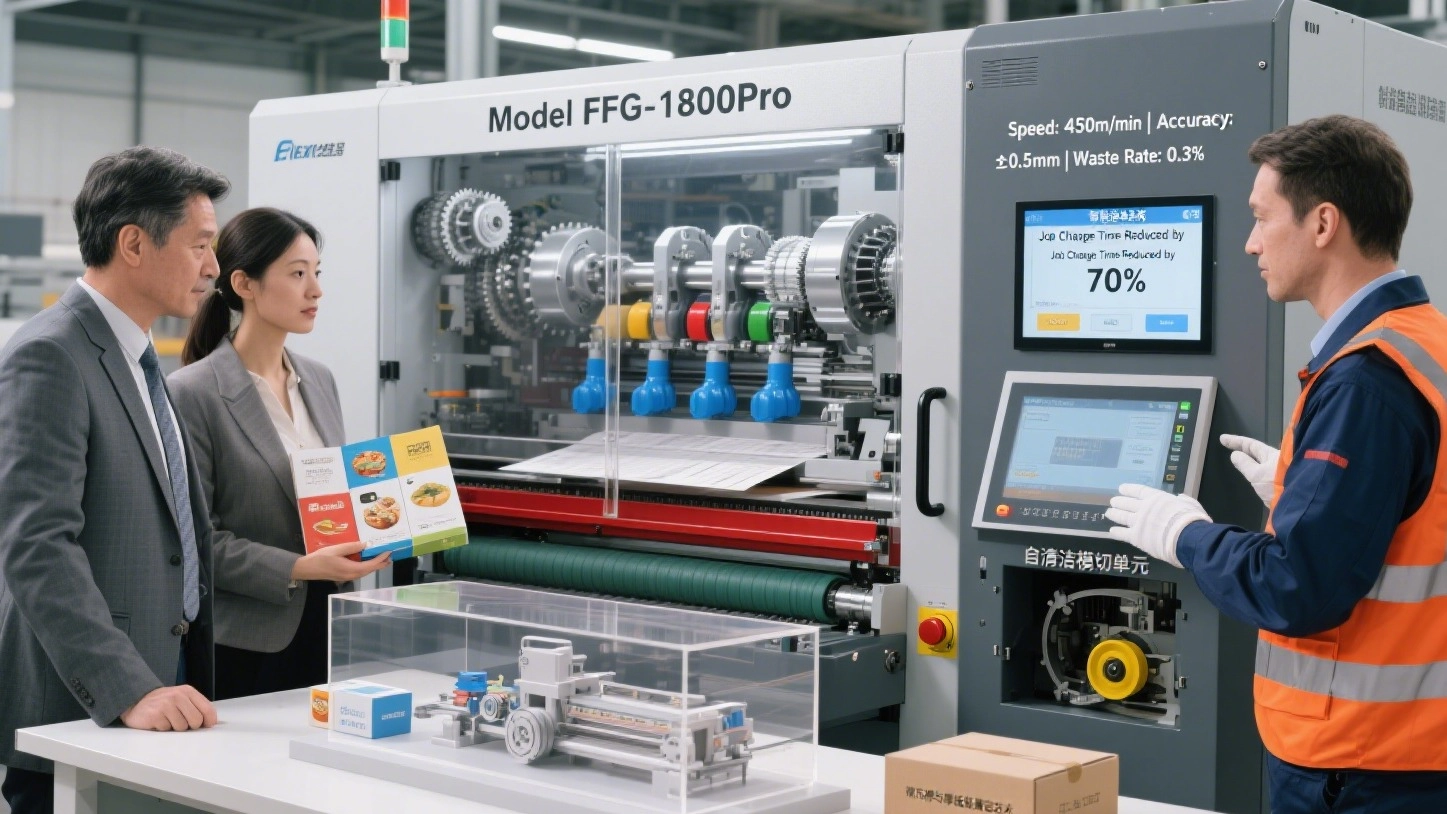
The Ultimate Guide to Flexo Folder Gluer Machines: How to Choose, Operate, and Maintain

Top Corrugated Box Printer Machine Brands
Industry Solutions
Can your machines handle high-volume production demands?
Yes, our machines are designed for high-volume production, ensuring reliable and efficient operation.
What industries typically use your folding carton machines?
Our machines are used in various industries including food and beverage, pharmaceuticals, cosmetics, and electronics.
Product
How can I integrate your machines into my existing production line?
Our technical team can assist with integrating our machines into your current production setup, ensuring a seamless operation.
What should I do if the machine jams during operation?
In case of a jam, immediately stop the machine, remove any obstructions, and check for any damage before restarting.
How do I troubleshoot common issues with the folding mechanism?
Common issues can often be resolved by checking the alignment of the folding plates and ensuring there is no debris obstructing the mechanism.
Leave a message
Have any questions or queries about our products? Please leave us a message here and our team will get back to you promptly.
* Rest assured that your privacy is important to us, and all information provided will be handled with the utmost confidentiality.
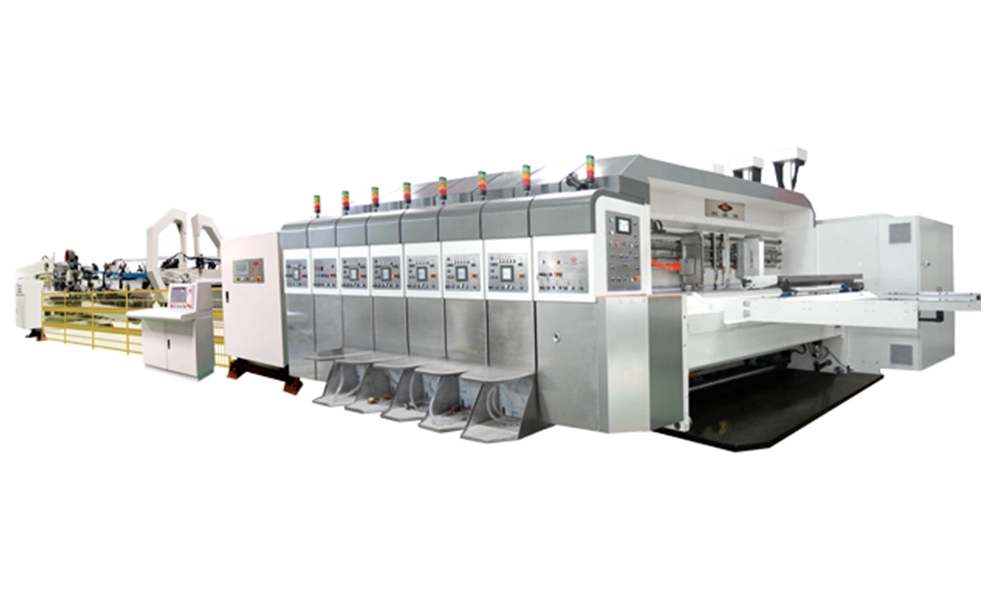
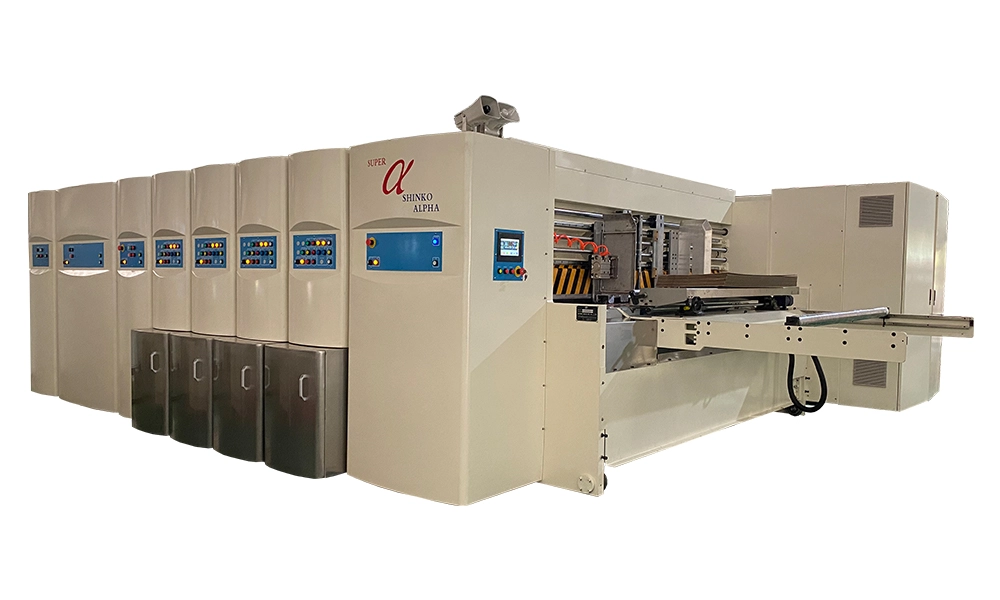
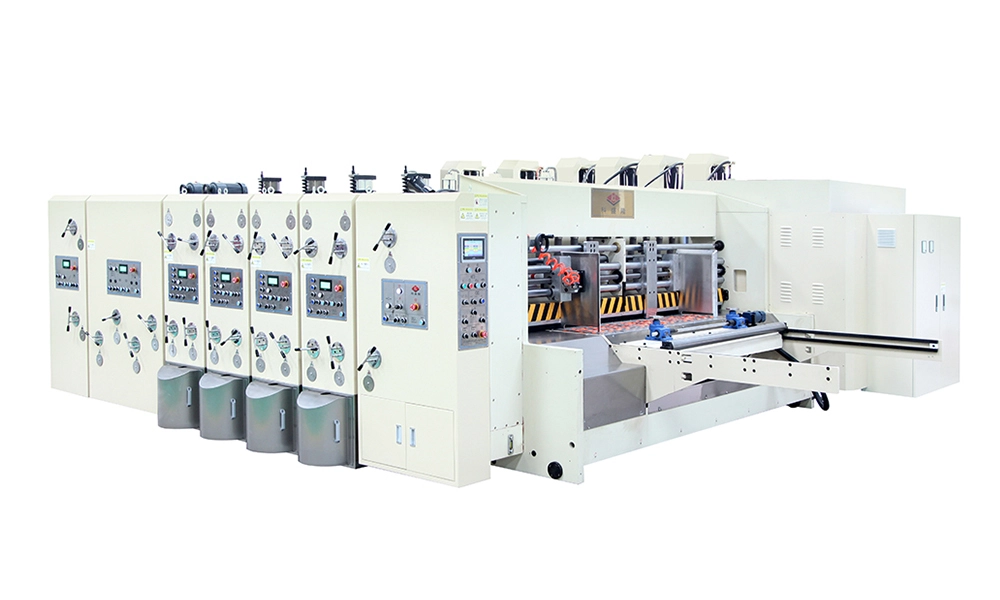
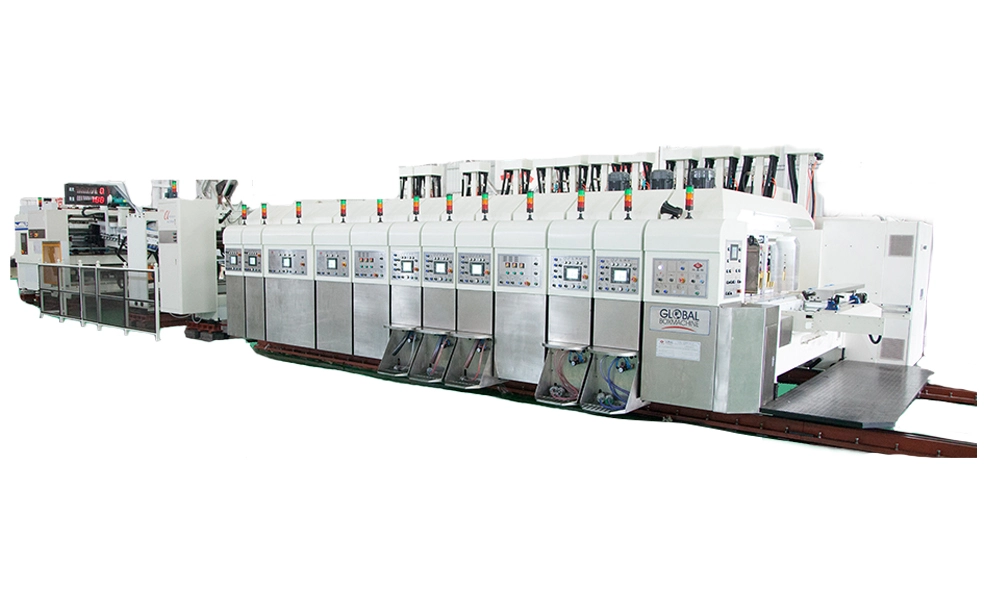
© 2025 Keshenglong & SHINKO All Rights Reserved.
Keshenglong Carton Packing Machine
Keshenglong Carton Packing Machine
Keshenglong Carton Packing Machine
Keshenglong Carton Packing Machine
Keshenglong Carton Packing Machine