What are the different types of die cutting machines? | Keshenglong&Shinko Expert Guide
For flexo printers, selecting the right die-cutting machine is paramount for production efficiency and product quality. This guide demystifies the various types – rotary, flatbed, and digital – addressing key considerations like speed, precision, and cost. We provide essential insights for informed procurement, ensuring your investment aligns with current and future production needs, culminating with the advantages of leading brands like Keshenglong and Shinko.
- Understanding Die Cutting Machines: An Essential Guide for Flexo Printers
- What are the fundamental differences between Rotary and Flatbed Die Cutting Machines?
- When should a flexo printer consider Digital Die Cutting over traditional methods?
- How do I choose the right die-cutting machine for my specific production volume and material types?
- What factors influence the precision and speed of die-cutting equipment?
- What are the key considerations for integrating a new die-cutting machine into an existing flexo printing workflow?
- Keshenglong & Shinko: Advantages in Die Cutting Solutions
Understanding Die Cutting Machines: An Essential Guide for Flexo Printers
In the dynamic world of flexographic printing, the efficiency and precision of post-press operations are just as crucial as the print quality itself. For flexo printers, especially those involved in packaging, labels, and corrugated board production, the die-cutting machine is a critical piece of equipment. As you consider your next capital investment, understanding the different types of die-cutting machines and their specific applications is key to optimizing your workflow and enhancing profitability. Let's delve into the most common questions and considerations for flexo printers in procurement.
What are the fundamental differences between Rotary and Flatbed Die Cutting Machines?
The choice between rotary and flatbed die-cutting machines often comes down to production volume, material type, and required precision.
- Rotary Die Cutting Machines: These machines utilize cylindrical dies that rotate at high speeds, making them ideal for long production runs and continuous processes. They are commonly integrated inline with flexo presses for label printing, flexible packaging, and certain types of corrugated board (e.g., in-line flexo folder-gluers). Rotary dies (often solid or flexible steel) are more expensive to produce initially but offer exceptional durability and fast throughput (e.g., up to 150-300 meters per minute for labels). Their continuous motion minimizes downtime between cuts. However, they are less versatile for very thick materials or intricate designs requiring multiple pressure points.
- Flatbed Die Cutting Machines: Operating with a flat cutting surface and a flat die (typically steel rule dies), these machines offer greater versatility and higher precision for intricate cuts, creasing, and embossing, especially on thicker substrates like folding carton and corrugated board. They are generally slower than rotary systems (e.g., 2,000-8,000 sheets per hour) due to their stop-start action, making them more suitable for short to medium runs. Flatbed dies are less costly and quicker to produce and modify. For corrugated post-print, flatbed die cutters are prevalent due to their ability to handle large sheet sizes and varying board thicknesses with high accuracy.
When should a flexo printer consider Digital Die Cutting over traditional methods?
Digital die cutting, which typically employs laser cutting, plotters, or digital knife technology, has emerged as a disruptive force, especially for short runs and specialized applications.
- Short Runs and Prototyping: The primary advantage is the elimination of physical dies, significantly reducing setup time and tooling costs. This makes digital die cutting highly economical for very short runs, personalized packaging, and prototyping where traditional die costs would be prohibitive.
- Variable Data and Intricate Designs: Digital technology excels at handling variable designs and highly complex, intricate cuts that would be difficult or impossible with conventional dies. It offers unparalleled design flexibility.
- Reduced Lead Times: Without the need to wait for die manufacturing, production lead times are drastically cut, allowing for faster response to market demands.
- Considerations: While versatile, digital die cutting is generally slower than high-volume rotary systems. For flexo printers, it's often a supplementary technology, complementing traditional methods for niche markets or on-demand services rather than replacing them for high-volume production.
How do I choose the right die-cutting machine for my specific production volume and material types?
Making the right choice involves a careful assessment of your current and future needs:
- Production Volume: For high-volume, long-run production (e.g., millions of labels, continuous corrugated box production), a high-speed rotary die cutter (often inline) is the most efficient choice. For short to medium runs, custom packaging, or specialty items, a flatbed or digital solution provides better cost-effectiveness and flexibility.
- Material Types: Consider the substrates you primarily work with. Rotary is excellent for thin films, labels, and some corrugated. Flatbed excels with thicker materials like heavy-duty corrugated board, micro-flute, and folding carton. Digital handles a wide range but may have speed limitations for very thick materials.
- Job Complexity: If your jobs frequently involve intricate patterns, multiple creases, or embossing, a flatbed machine offers superior precision. For basic shapes at high speed, rotary is preferred. Digital is unmatched for unique and complex, short-run designs.
- Budget & ROI: Evaluate the initial investment (machine cost, tooling cost) against potential return on investment (throughput, waste reduction, new market opportunities).
What factors influence the precision and speed of die-cutting equipment?
Both precision and speed are critical performance indicators, and they are influenced by several factors:
- Die Quality: The quality and manufacturing accuracy of the die itself are paramount. High-quality steel dies (for rotary or flatbed) maintain precision over long runs.
- Machine Rigidity & Build Quality: A robust, well-engineered machine minimizes vibration and ensures consistent pressure across the cutting area, directly impacting precision. Heavy-duty construction and quality components (e.g., bearings, gears, servo motors) contribute to both speed and stability.
- Automation & Registration Systems: Advanced feeding and delivery systems, along with precise registration technology (e.g., optical sensors for print-to-cut registration), ensure accurate cuts, especially on pre-printed material. Fully automatic machines reduce human error and increase effective throughput.
- Operator Skill & Maintenance: While less about the machine itself, skilled operators and regular, proper maintenance significantly impact the longevity of the machine's precision and its operational speed.
What are the key considerations for integrating a new die-cutting machine into an existing flexo printing workflow?
Seamless integration is vital to maximize the efficiency of your entire production line:
- Inline vs. Offline: For label and continuous roll applications, inline rotary die cutting (integrated directly with the flexo press) offers the highest efficiency, eliminating transfer steps and reducing waste. For sheet-fed applications (e.g., corrugated, folding carton), an offline flatbed die cutter is standard.
- Automation & Connectivity: Consider machines with advanced automation features (e.g., automatic sheet feeding, waste stripping, stacking) to minimize manual intervention and labor costs. Look for systems that can integrate with your existing management information systems (MIS) for production tracking and scheduling.
- Space & Infrastructure: Evaluate the physical footprint of the new machine and ensure your facility has adequate space, power supply, and material handling capabilities (e.g., forklift access, pallet storage).
- Training & Support: Prioritize suppliers who offer comprehensive training for your operators and robust after-sales support to ensure smooth operation and minimal downtime.
Keshenglong & Shinko: Advantages in Die Cutting Solutions
When considering investments in die-cutting technology, especially within the corrugated and heavy-duty packaging sectors, brands like Keshenglong and Shinko stand out. Both are renowned for their robust, high-performance machinery that flexo printers can rely on for consistent quality and efficiency.
- Keshenglong: A prominent name, especially in the corrugated industry, Keshenglong machines (often flexo printer-slotter-die-cutters or stand-alone flatbed die cutters) are known for their heavy-duty construction, high precision, and reliability. They often feature advanced servo drive technology, quick setup times, and superior waste stripping capabilities, leading to high throughput and reduced labor. Their focus on durability ensures a long operational life and consistent performance under demanding industrial conditions.
- Shinko: Another leading manufacturer, Shinko is synonymous with high-speed, high-precision corrugated machinery. Their inline flexo folder-gluers often come with integrated rotary die-cutting units that deliver exceptional accuracy and speed for complex box designs. Shinko machines are celebrated for their engineering excellence, advanced automation features, and user-friendliness, contributing to significant productivity gains and lower operational costs for flexo printers handling large volumes of corrugated board.
Both brands offer solutions that prioritize efficiency, durability, and technological advancement, making them strong contenders for flexo printers looking to upgrade or expand their die-cutting capabilities and ensure a competitive edge in the market.
Recommended for you
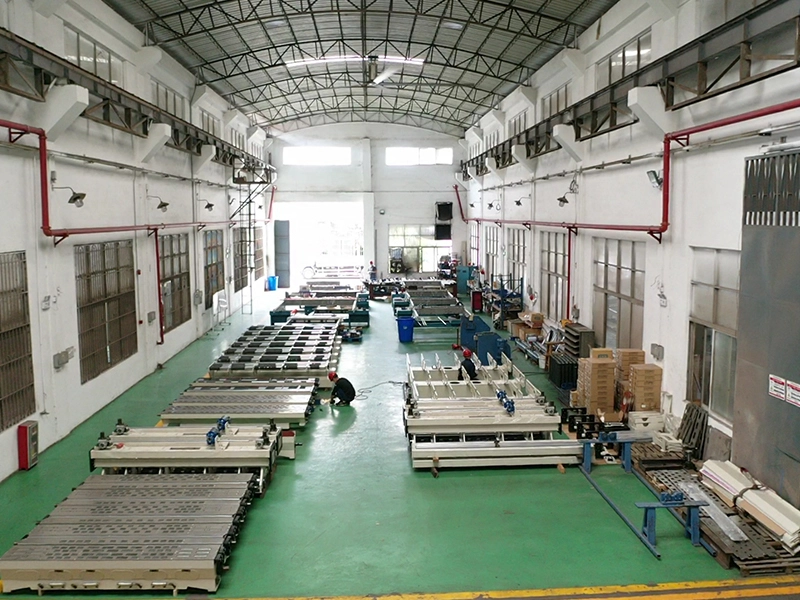
5 Common Flexo Folder Gluer Problems and Expert Solutions
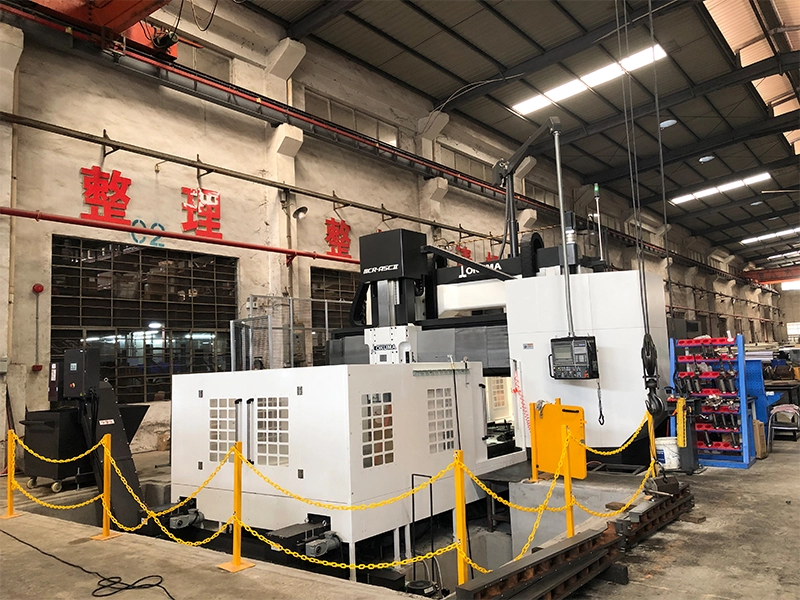
Flexo Folder Gluer Explained: Your Expert Guide
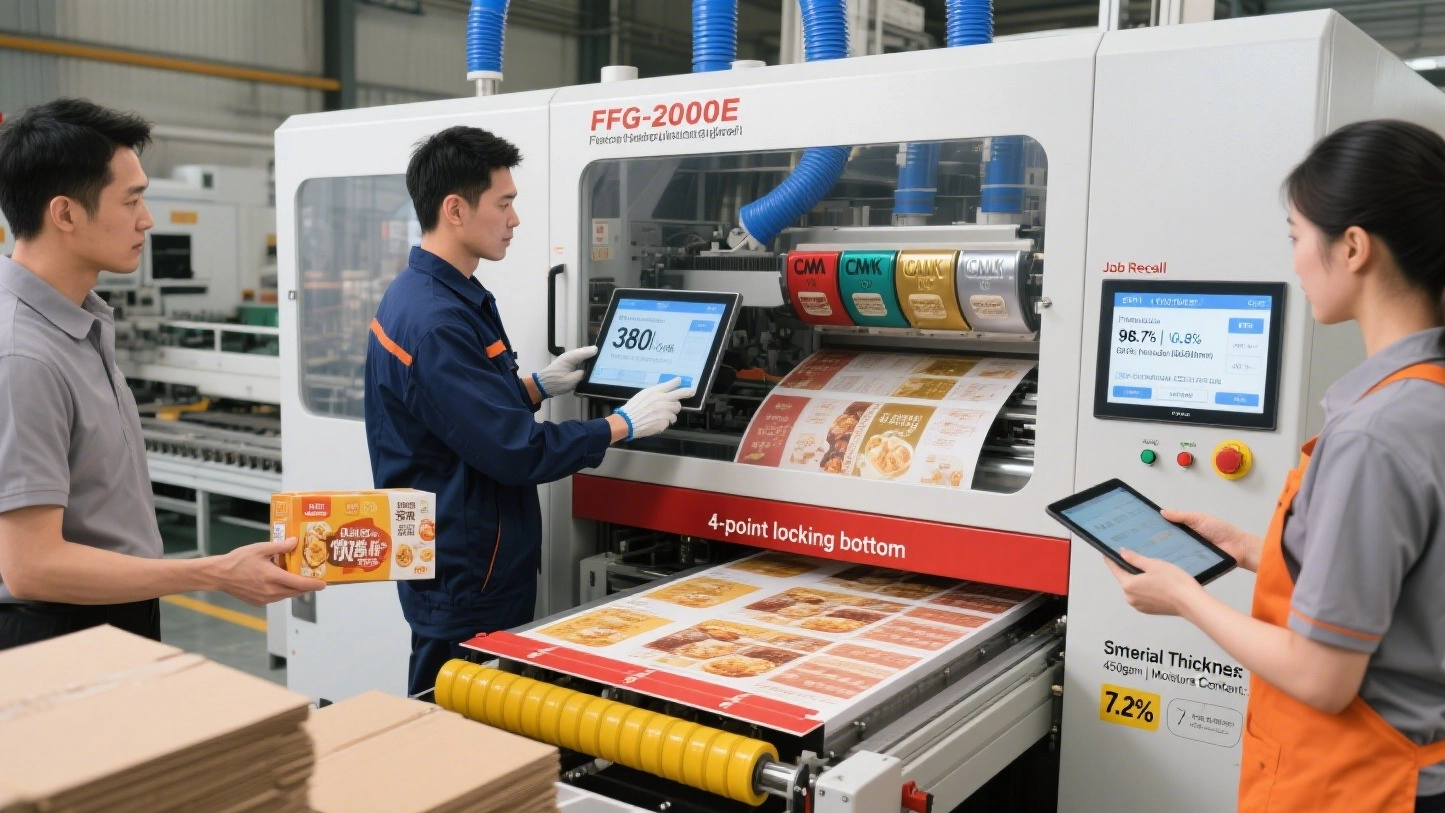
How to Operate a Flexo Folder Gluer Efficiently
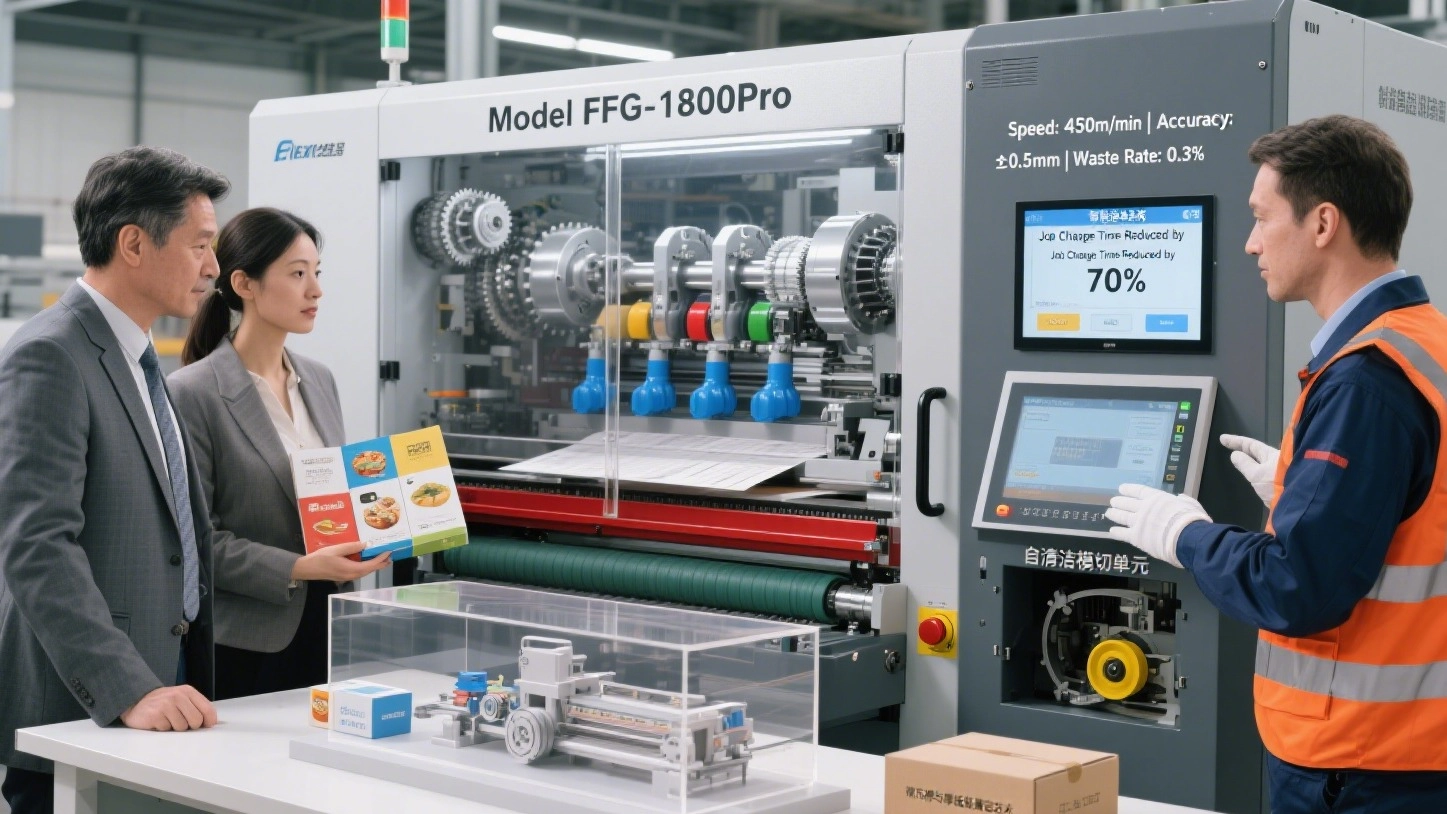
The Ultimate Guide to Flexo Folder Gluer Machines: How to Choose, Operate, and Maintain

Top Corrugated Box Printer Machine Brands
Shipping
What is the estimated delivery time for your machines?
Delivery times vary based on location and order size, but we typically estimate 4-6 weeks for delivery.
Do you offer international shipping for your machines?
Yes, we offer international shipping and can handle all necessary customs documentation.
Product
How do I troubleshoot common issues with the folding mechanism?
Common issues can often be resolved by checking the alignment of the folding plates and ensuring there is no debris obstructing the mechanism.
What materials are compatible with your folding carton machines?
Our machines are compatible with a wide range of materials including cardboard, corrugated board, and paperboard.
Industry Solutions
What is the lifespan of your folding carton machines?
With proper maintenance, our machines are built to last for many years, providing long-term value for your investment.
Leave a message
Have any questions or queries about our products? Please leave us a message here and our team will get back to you promptly.
* Rest assured that your privacy is important to us, and all information provided will be handled with the utmost confidentiality.
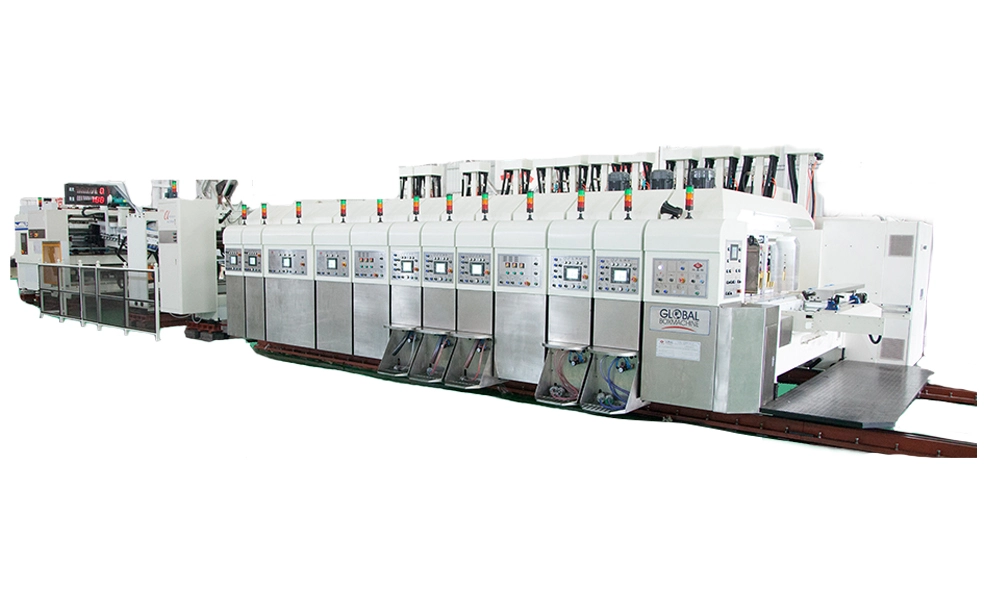
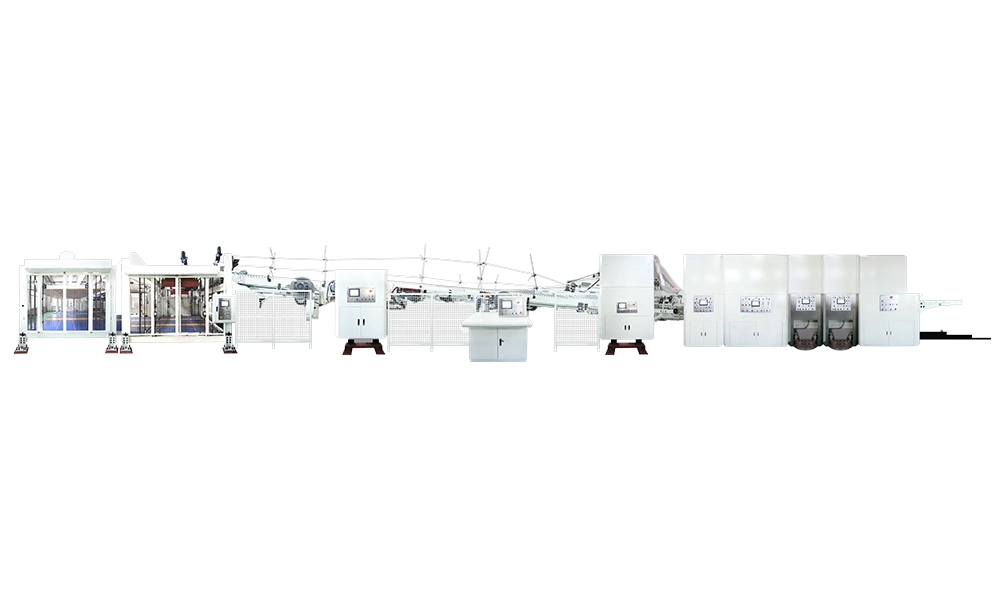
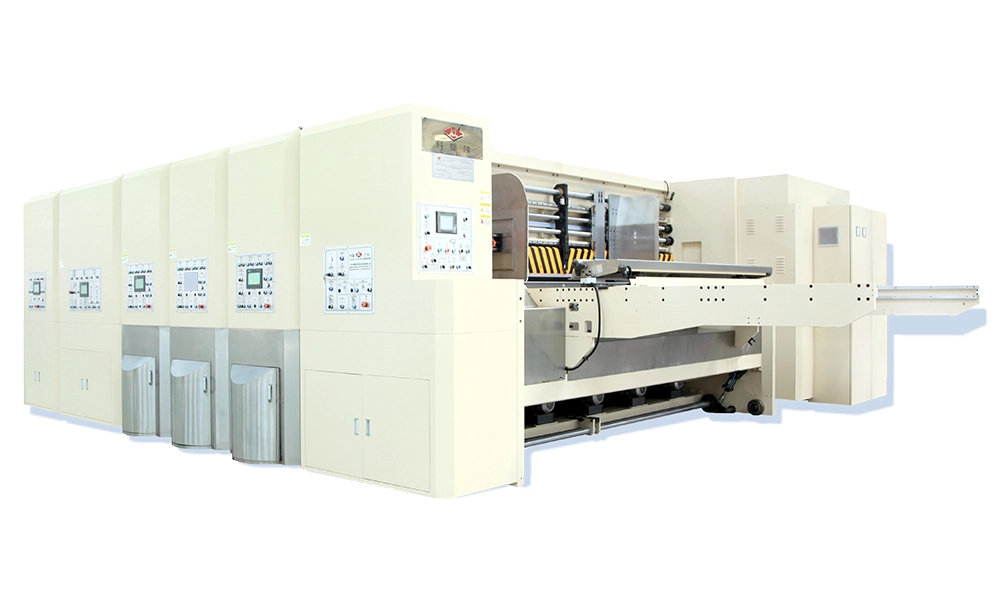
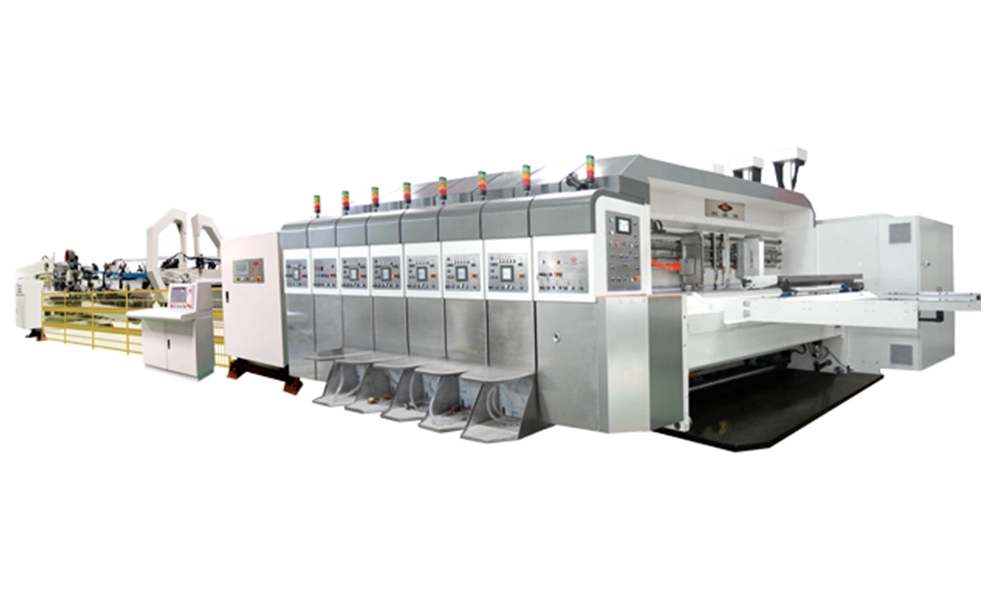
© 2025 Keshenglong & SHINKO All Rights Reserved.
Keshenglong Carton Packing Machine
Keshenglong Carton Packing Machine
Keshenglong Carton Packing Machine
Keshenglong Carton Packing Machine
Keshenglong Carton Packing Machine