What is a die cutting machine used for? | Keshenglong&Shinko Expert Guide
Die cutting machines are indispensable tools in flexographic printing, crucial for transforming printed rolls into finished products like labels, packaging, and specialized components. This article delves into their diverse applications, comparing rotary and flatbed types, highlighting the significant benefits they offer in terms of precision, speed, and waste reduction. Discover essential features for enhancing your flexo workflow and learn why brands like Keshenglong & Shinko lead the industry, providing reliable, high-performance solutions for your re-purchasing needs.
- What Exactly is a Die-Cutting Machine Used for in Flexographic Printing?
- How Do Different Types of Die-Cutting Machines Cater to Flexo Printing Needs?
- What Are the Key Benefits of Integrating a Modern Die-Cutting Machine into a Flexo Workflow?
- What Materials Can Be Effectively Die-Cut, and What Are the Limitations?
- What Advanced Features Should Flexo Printers Look For in a New Die-Cutting Machine?
- Keshenglong & Shinko: Leading the Way in Converting Solutions
What Exactly is a Die-Cutting Machine Used for in Flexographic Printing?
In the dynamic world of flexographic printing, a die-cutting machine is not just an accessory; it's a critical component that transforms printed rolls of material into their final, functional shapes. At its core, a die-cutting machine uses a custom-made steel rule die or rotary tool to precisely cut, crease, perforate, or even emboss specific designs out of a substrate. For flexo printers, its primary use is to produce a wide array of finished products, including self-adhesive labels, flexible packaging, tags, cartons, and specialized components that require intricate and repeatable shapes. It's the precision and efficiency of this process that enables high-volume production with consistent quality, making it indispensable for converting printed web into ready-to-use items.
How Do Different Types of Die-Cutting Machines Cater to Flexo Printing Needs?
For flexographic printers, the choice typically narrows down to two main types: rotary die-cutting and flatbed die-cutting, each serving distinct purposes based on application, volume, and material.
- Rotary Die-Cutting: This is the workhorse of the flexo label and flexible packaging industry. It uses cylindrical dies mounted on a rotating press. Known for its incredible speed and efficiency, rotary die-cutting can run continuously at high speeds, often matching or exceeding the speed of modern flexo presses (e.g., up to 150-200 meters per minute or more). It's ideal for long production runs of labels, pouches, and thin film packaging where precision and throughput are paramount. Its ability to integrate inline with flexo presses streamlines the entire printing and converting process.
- Flatbed Die-Cutting: While less common for high-volume label production directly inline with flexo presses, flatbed die-cutters are crucial for thicker materials like folding cartons, heavy tags, or for shorter runs requiring deep creases or complex cuts. They operate by pressing a flat die onto the material, offering high cutting force and precision for a wider range of thicknesses. Some flexo printers utilize flatbed units offline for specialized packaging or display items.
The global die-cutting machine market, valued at approximately USD 2.3 billion in 2022, is projected to grow, with rotary solutions dominating the packaging and label segments due to their speed and automation capabilities (Source: Mordor Intelligence, Die Cutting Machine Market - Growth, Trends, COVID-19 Impact, and Forecasts (2023 - 2028)).
What Are the Key Benefits of Integrating a Modern Die-Cutting Machine into a Flexo Workflow?
Investing in a modern die-cutting machine offers significant returns for flexo printers:
- Enhanced Precision and Quality: Modern machines, especially rotary ones, offer exceptional cutting accuracy, often down to ±0.005 inches (0.127 mm) or even tighter tolerances. This ensures consistent product quality, critical for brand consistency and functionality (e.g., proper label application).
- Increased Production Efficiency: High-speed operation and quick job changeovers minimize downtime. Inline integration with flexo presses eliminates the need for separate handling, significantly boosting overall throughput and reducing lead times.
- Material Waste Reduction: Advanced features like automated waste matrix stripping and precise registration systems minimize material waste, which is a substantial cost saving. For every 1% reduction in material waste, large-scale operations can save tens of thousands annually.
- Versatility and Design Freedom: The ability to create intricate and unique shapes allows printers to offer more complex and visually appealing product designs, providing a competitive edge in the market.
- Cost Savings: Beyond waste reduction, automation reduces labor costs, and faster production cycles mean higher output per shift, improving profitability.
What Materials Can Be Effectively Die-Cut, and What Are the Limitations?
Die-cutting machines in flexographic operations are designed to handle a diverse range of flexible and semi-rigid substrates commonly used in printing:
- Self-Adhesive Papers: Coated, uncoated, thermal, and specialty papers are routinely die-cut for labels of all kinds.
- Films: A wide variety of plastic films, including BOPP, PET, PE, PVC, and synthetic papers, are cut for flexible packaging, shrink sleeves, and durable labels. These require precise tension control and specialized tooling to prevent stretching or tearing.
- Tag and Board Stock: Thicker paperboards, tag materials, and some light carton stock can be die-cut, often requiring more robust tooling or flatbed systems for creasing.
- Foils and Laminates: Multi-layer laminates and metallic foils are also processed, demanding specific die designs and cutting pressures to ensure clean cuts without delamination.
Limitations primarily revolve around material thickness and rigidity. While rotary dies excel with thinner, flexible materials, very thick corrugated board or extremely rigid plastics might require specialized heavy-duty flatbed or digital cutting solutions. Material integrity and precise web tension control are paramount to prevent distortions during high-speed cutting.
What Advanced Features Should Flexo Printers Look For in a New Die-Cutting Machine?
When considering a re-purchase, look beyond basic cutting functionality for features that enhance productivity, precision, and ease of use:
- Automated Registration Systems: Critical for multi-color jobs, these systems use sensors (e.g., optical or vision systems) to ensure the die cut aligns perfectly with the printed image, compensating for web stretch or misfeeds in real-time.
- Quick Changeover Systems: Magnetic cylinders for flexible dies allow for rapid job setup and changeovers, significantly reducing downtime between runs. This is crucial for short-to-medium run versatility.
- Automated Waste Matrix Stripping: Efficient removal of waste material surrounding the cut product is vital. Advanced systems include vacuum removal, air jets, and specialized tools to ensure clean separation at high speeds, preventing costly bottlenecks.
- Multi-Die and Re-registration Capabilities: For complex jobs, the ability to use multiple dies simultaneously or re-register for a second pass (e.g., for intricate perforations or kiss-cutting) offers tremendous flexibility.
- Digital Integration and Automation: Look for machines with intuitive touchscreens, job memory, and connectivity options for seamless integration into existing MIS (Management Information System) and workflow automation.
- Energy Efficiency and Sustainability: Modern machines often incorporate energy-saving motors and designs that reduce power consumption, aligning with growing industry demands for sustainable operations.
Keshenglong & Shinko: Leading the Way in Converting Solutions
When it comes to reliable and high-performance converting equipment, Keshenglong (KSL) and Shinko stand out as industry leaders, offering distinct advantages for flexo printers.
- Keshenglong (KSL): A prominent player in the flexographic printing and converting machinery sector, particularly in the Asian market, KSL is renowned for its integrated flexo presses that often include robust inline die-cutting units. KSL machines are praised for their competitive pricing, high speed, precision, and reliable performance, making them an excellent choice for label and flexible packaging printers seeking a cost-effective yet powerful solution with strong after-sales support. Their continuous innovation in automation and user-friendliness makes them a preferred choice for enhancing workflow efficiency.
- Shinko: While historically recognized for its heavy-duty rotary die-cutting and converting machinery for corrugated board, Shinko's reputation for engineering excellence, durability, and high-performance extends across the broader converting industry. Shinko machines are known for their exceptional build quality, longevity, and consistent precision, even under demanding industrial conditions. For printers with diverse material requirements or those seeking equipment with a proven track record of robustness and minimal maintenance, Shinko represents a High Quality investment in reliability and long-term operational stability.
Both brands exemplify the advancements in die-cutting technology, providing solutions that empower flexo printers to achieve higher efficiency, superior product quality, and greater profitability in today's competitive market.
Recommended for you
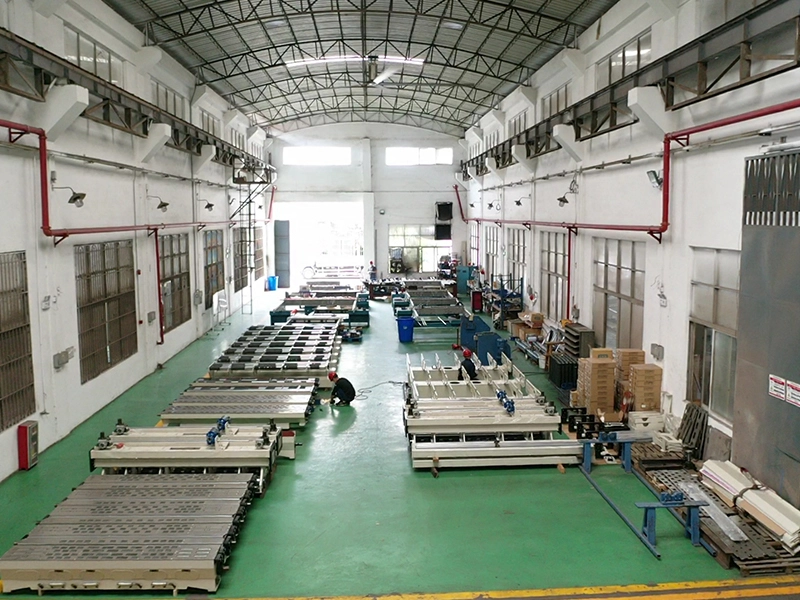
5 Common Flexo Folder Gluer Problems and Expert Solutions
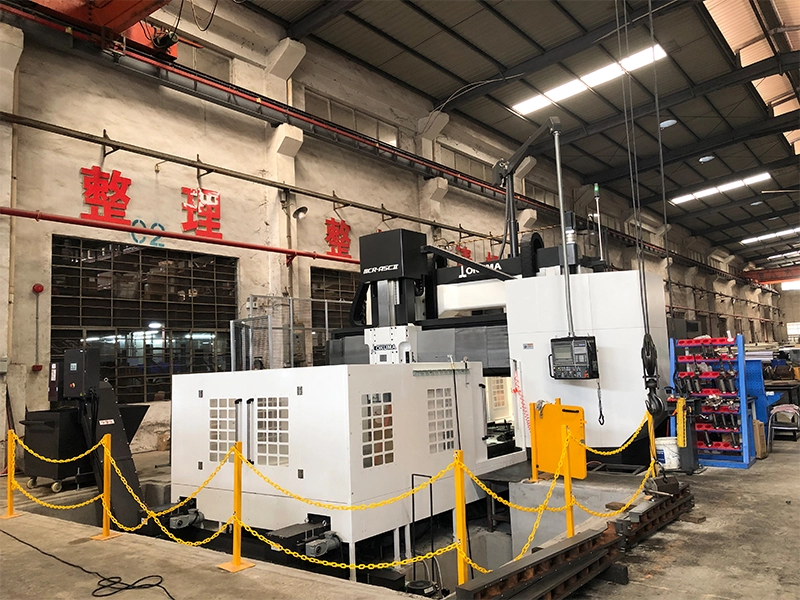
Flexo Folder Gluer Explained: Your Expert Guide
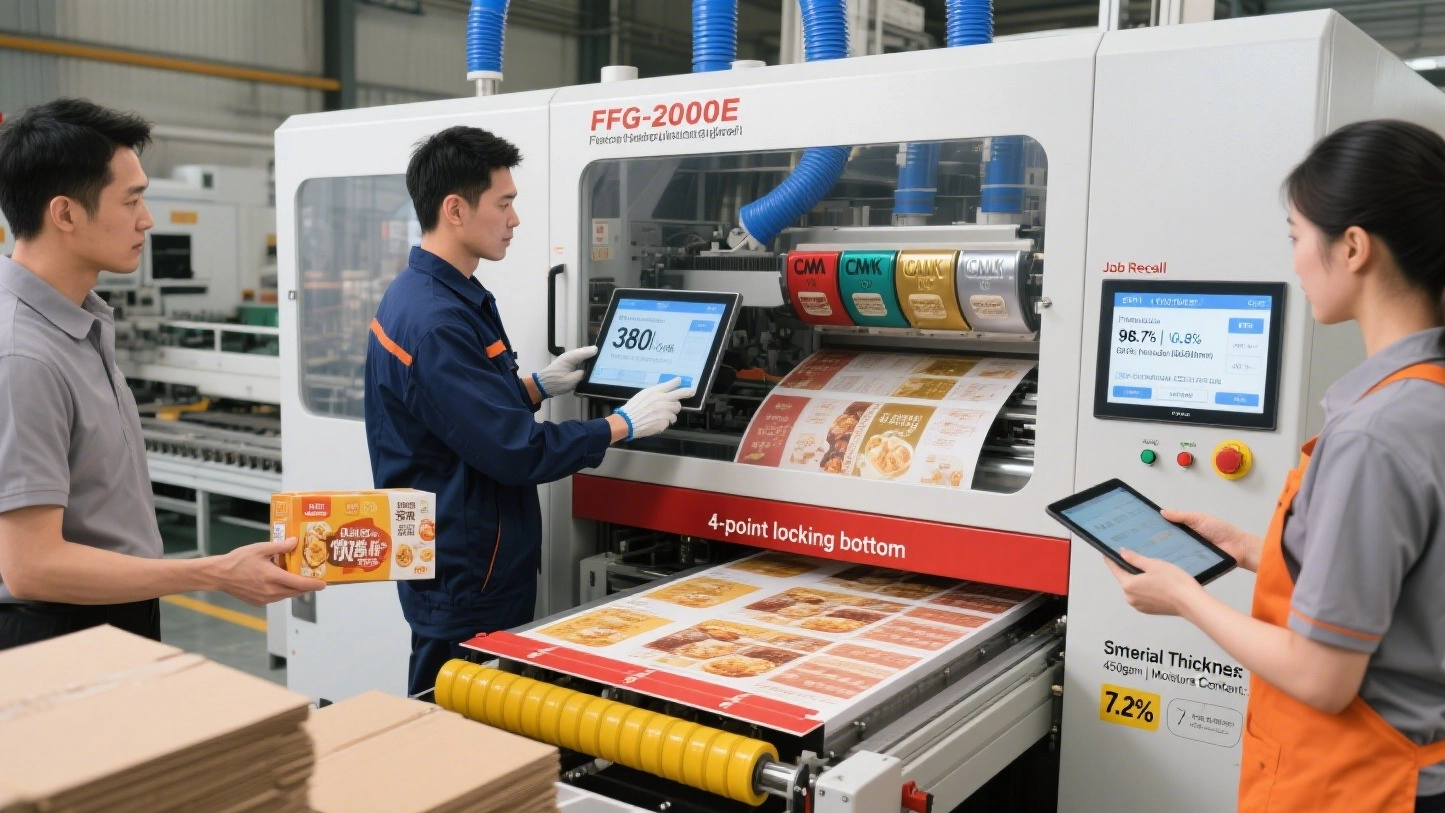
How to Operate a Flexo Folder Gluer Efficiently
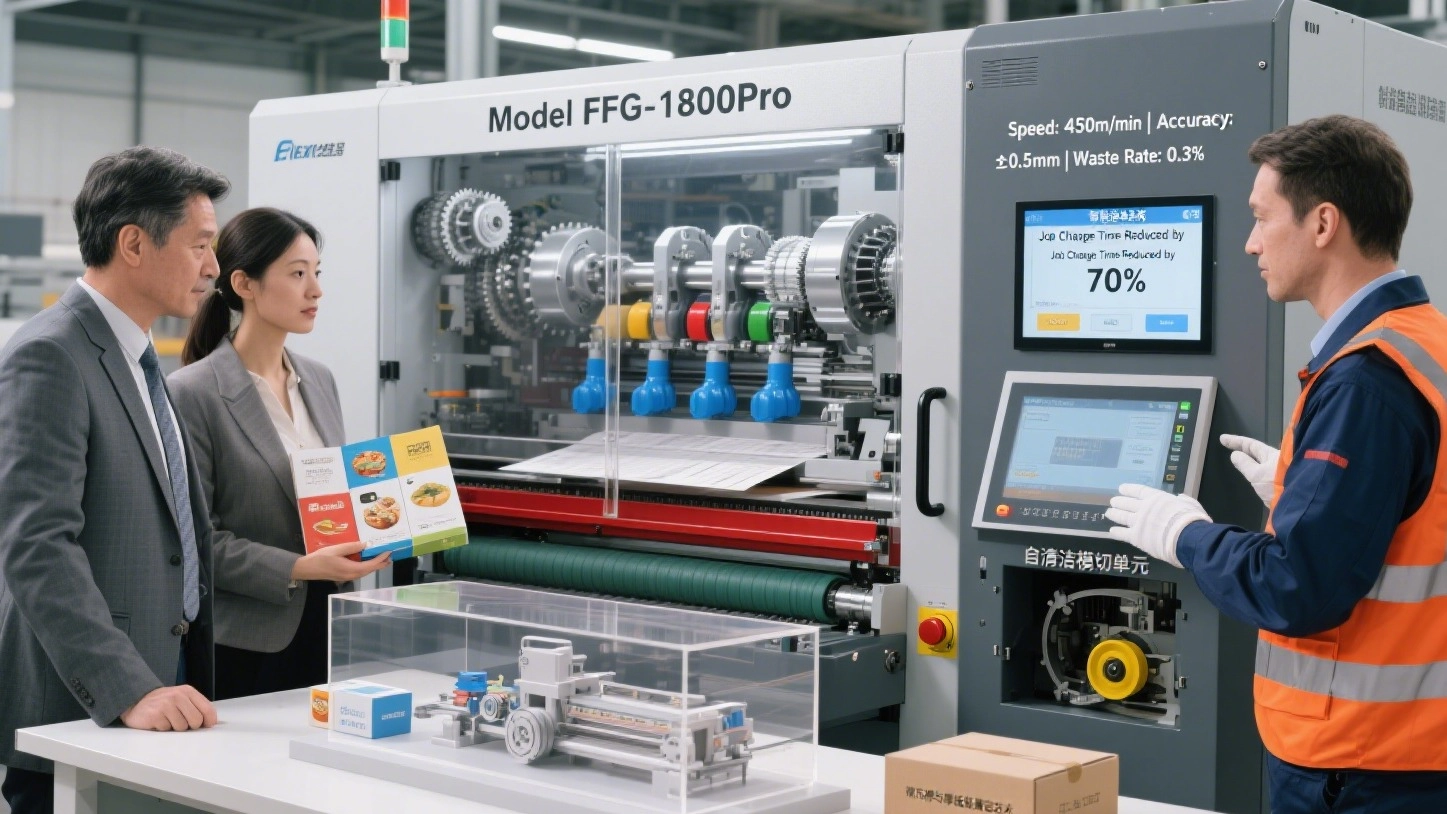
The Ultimate Guide to Flexo Folder Gluer Machines: How to Choose, Operate, and Maintain

Top Corrugated Box Printer Machine Brands
Product
Can your machines handle custom carton designs?
Yes, our machines can be customized to handle various carton designs and specifications.
Do your machines support automated quality control checks?
Yes, our machines can be equipped with automated quality control systems to ensure consistent production quality.
Shipping
Can I track my shipment once it has been dispatched?
Yes, we provide tracking information for all shipments so you can monitor the delivery status.
Can you ship to remote or difficult-to-access locations?
Yes, we can arrange shipping to remote locations, though additional charges and time may apply.
Industry Solutions
How can your machines improve my production workflow?
By automating carton production, our machines streamline your workflow, increase output, and reduce downtime.
Leave a message
Have any questions or queries about our products? Please leave us a message here and our team will get back to you promptly.
* Rest assured that your privacy is important to us, and all information provided will be handled with the utmost confidentiality.
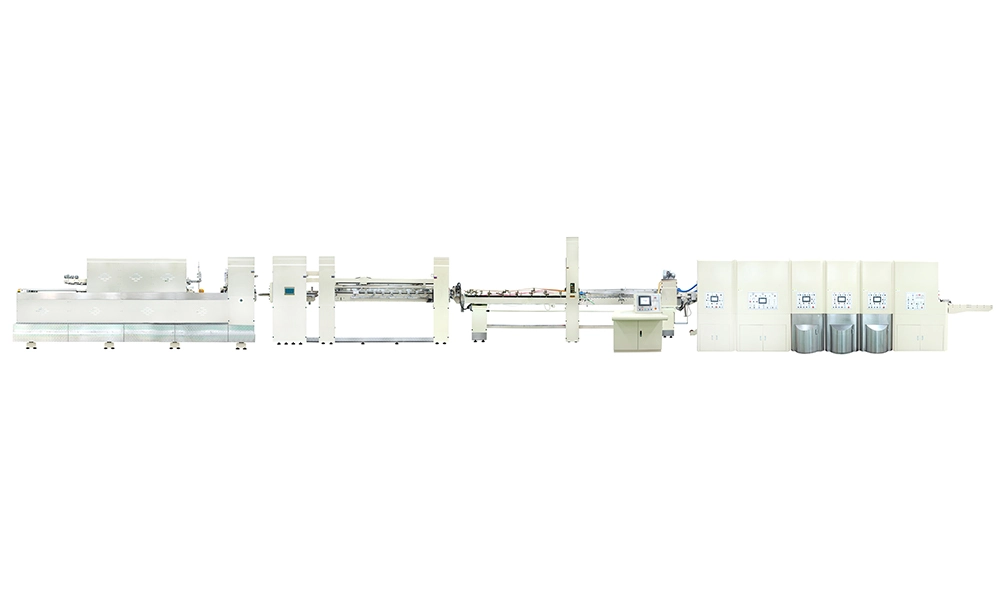
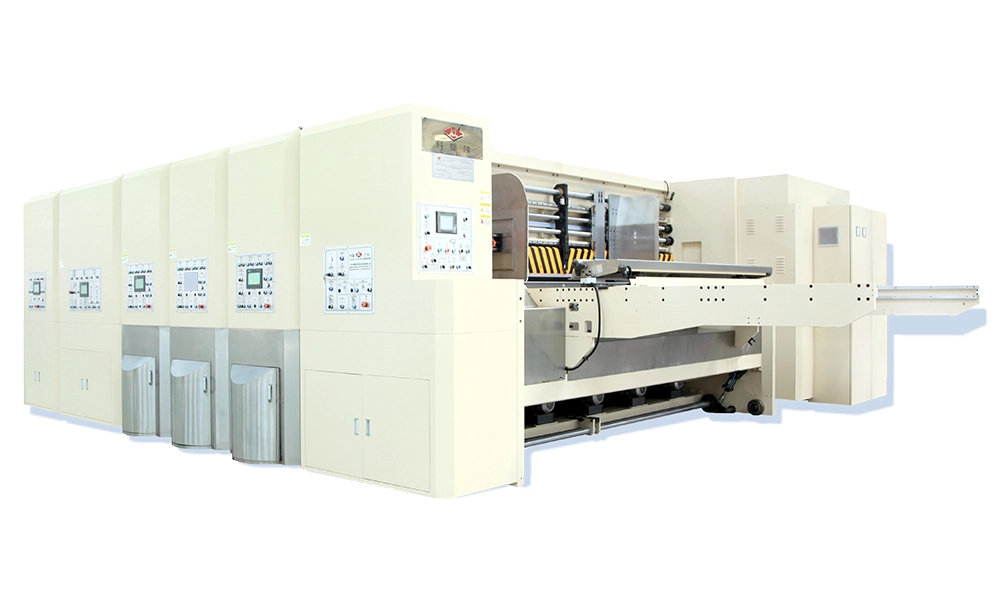
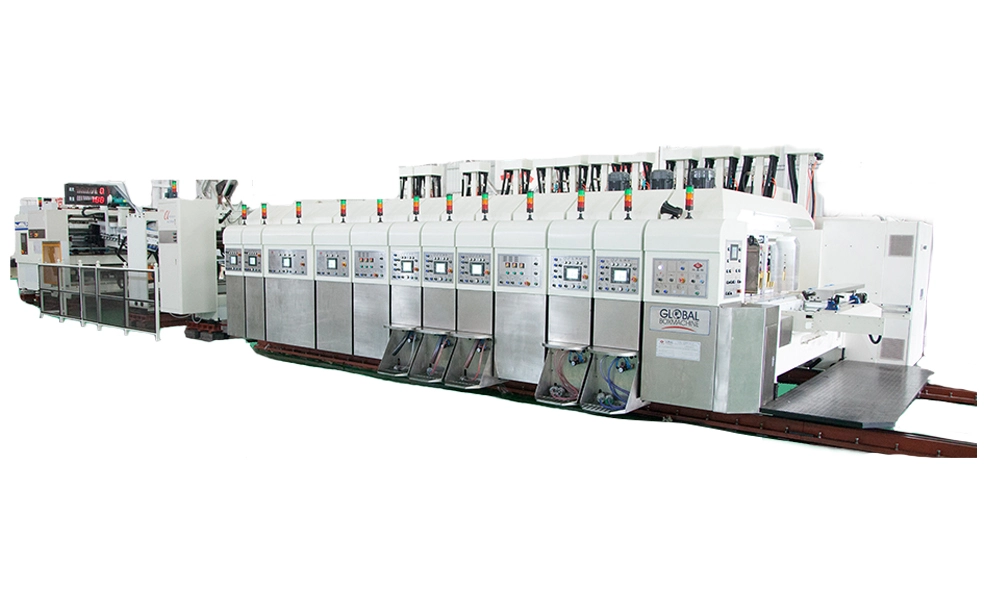
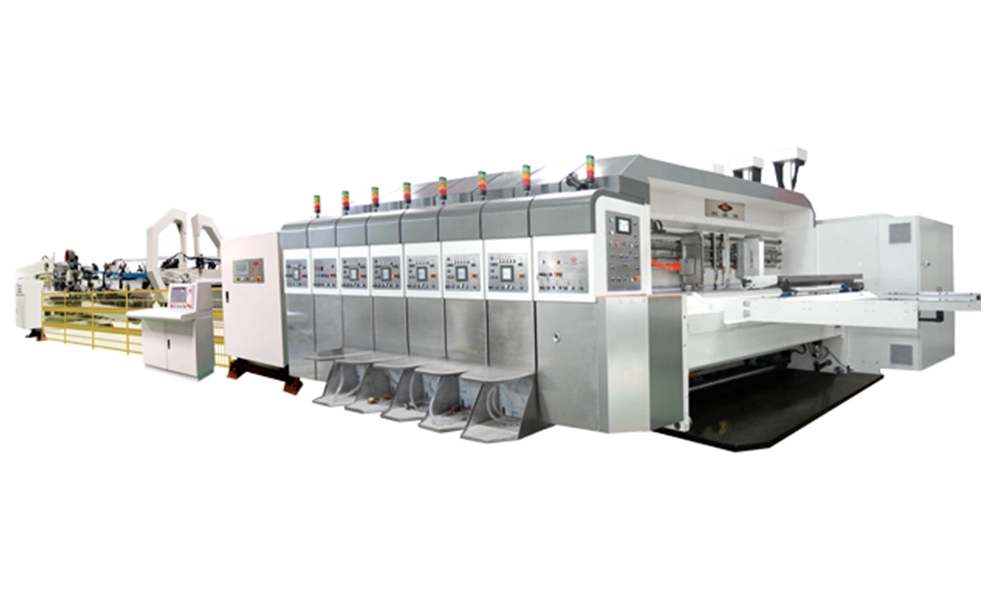
© 2025 Keshenglong & SHINKO All Rights Reserved.
Keshenglong Carton Packing Machine
Keshenglong Carton Packing Machine
Keshenglong Carton Packing Machine
Keshenglong Carton Packing Machine
Keshenglong Carton Packing Machine