How do you choose the correct printing plate for a flexographic machine? | Keshenglong&Shinko Guide
Discover expert guidance for choosing the right flexographic printing plate. Improve print quality, reduce waste, and optimize production with Keshenglong&Shinko.
- How do you choose the correct printing plate for a flexographic machine?
- Understand Plate Types and Materials
- Match Plate Hardness to Substrate
- Consider Print Image Detail and Line Screen
- Factor in Ink Type and Compatibility
- Evaluate Plate Thickness and Backing
- Consider Production Run Length and Cost Efficiency
- Consult Technical Support and Plate Suppliers
- References:
How do you choose the correct printing plate for a flexographic machine?
Selecting the correct printing plate for a flexographic machine is crucial for achieving high-quality prints, efficient production, and reduced waste. Flexo professionals often face challenges in balancing plate durability, ink compatibility, and image detail. This guide provides clear criteria to optimize plate selection.
Understand Plate Types and Materials
- Photopolymer Plates: Most common in modern flexography, offering high resolution; suitable for short and long runs.
- Rubber Plates: Less prevalent now, but still used for simple designs or basic printing.
- Elastomer Plates: Durable, ideal for abrasive substrates and long production runs.
Authoritative Source: *Flexographic Technical Association (FTA)* recommends photopolymer plates for most high-quality commercial applications.
Match Plate Hardness to Substrate
- Soft Plates (Hardness Shore A 35–45): Ideal for rough or textured substrates (e.g., corrugated board).
- Medium Plates (Hardness Shore A 45–55): Suitable for coated or smooth paper, label stock.
- Hard Plates (Hardness Shore A 55–65): Best for film, foil, or other very smooth surfaces.
Consider Print Image Detail and Line Screen
- Fine Detail: Use higher line screen photopolymer plates (100–200 LPI) for intricate graphics or small text.
- Large Solid Areas: Lower line screen or thicker plates prevent pinholing, ensuring solid ink laydown.
- Expert Tip: Fine detail plates often require precise control of impression settings—refer to your press manufacturer’s recommendations.
Factor in Ink Type and Compatibility
- Solvent-based Inks: Choose plates resistant to swelling and wear.
- Water-based Inks: Select plates with optimized surface tension properties for clean ink transfer.
- UV-curable Inks: Use UV-compatible plates to prevent chemical degradation.
Data Point: *According to Smithers’ industry report, 55% of converters now prioritize ink compatibility when investing in new plate materials.*
Evaluate Plate Thickness and Backing
- Standard Thickness (1.14 mm, 1.7 mm, 2.84 mm): Matches industry norms for ease of mounting and consistent print impression.
- Custom Thickness: Custom jobs may require tailored backing for emboss or specialty effects.
Consider Production Run Length and Cost Efficiency
- Short Runs: Digital photopolymer plates offer fast turnaround and cost-effectiveness.
- Long Runs: Elastomer and high-durometer plates reduce wear and rebuild costs.
Consult Technical Support and Plate Suppliers
- Supplier Guidance: Work closely with plate manufacturers or suppliers for recommendations based on your specific press and job requirements.
- Plate Test Data: Request sample runs and comparative data for your applications.
Summary Checklist: Key Considerations for Flexographic Plate Selection
- Match plate type to substrate and expected print run length
- Align plate hardness with substrate texture
- Choose the correct line screen for desired print resolution
- Ensure compatibility with planned ink system
- Factor in cost, availability, and technical support
References:
- Flexographic Technical Association (FTA): (https://www.flexography.org)
- Smithers Flexo Industry Reports & Market Data
For further information or technical support, contact Keshenglong&Shinko’s flexo printing experts. Optimize your printing process with informed plate selection.
Recommended for you
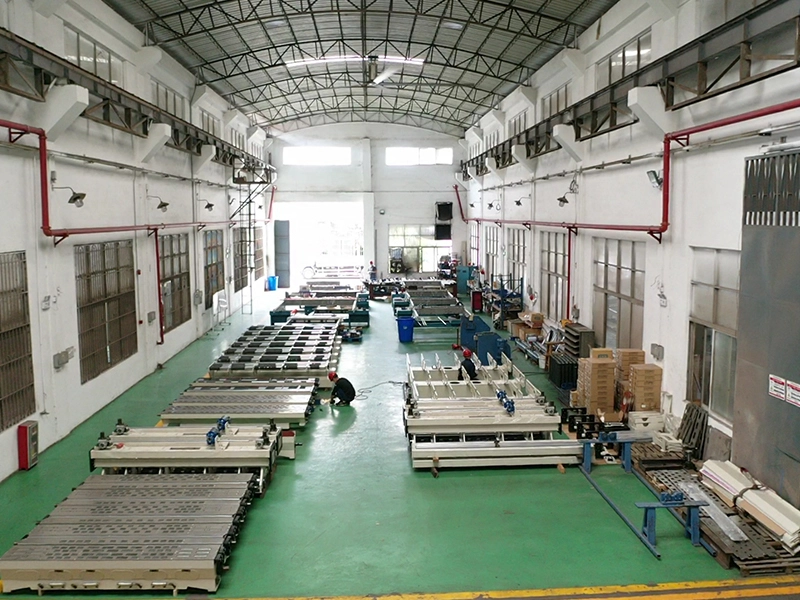
5 Common Flexo Folder Gluer Problems and Expert Solutions
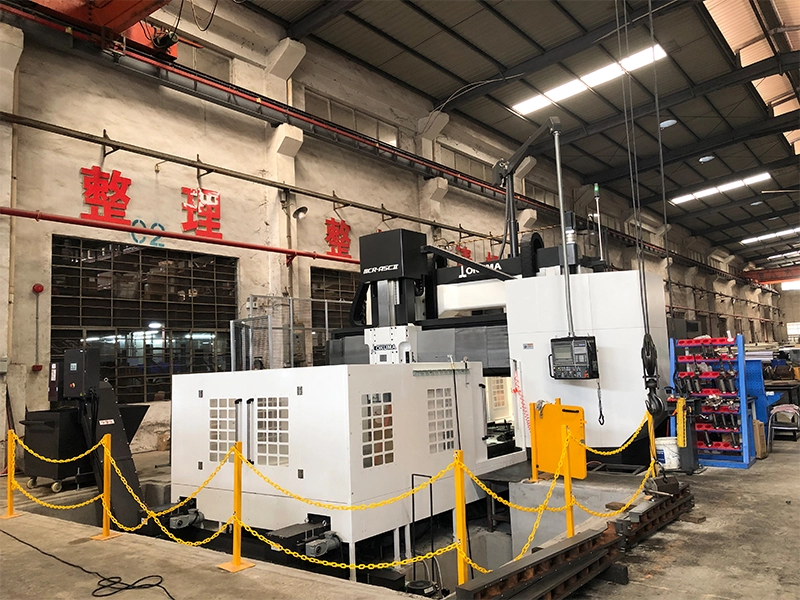
Flexo Folder Gluer Explained: Your Expert Guide
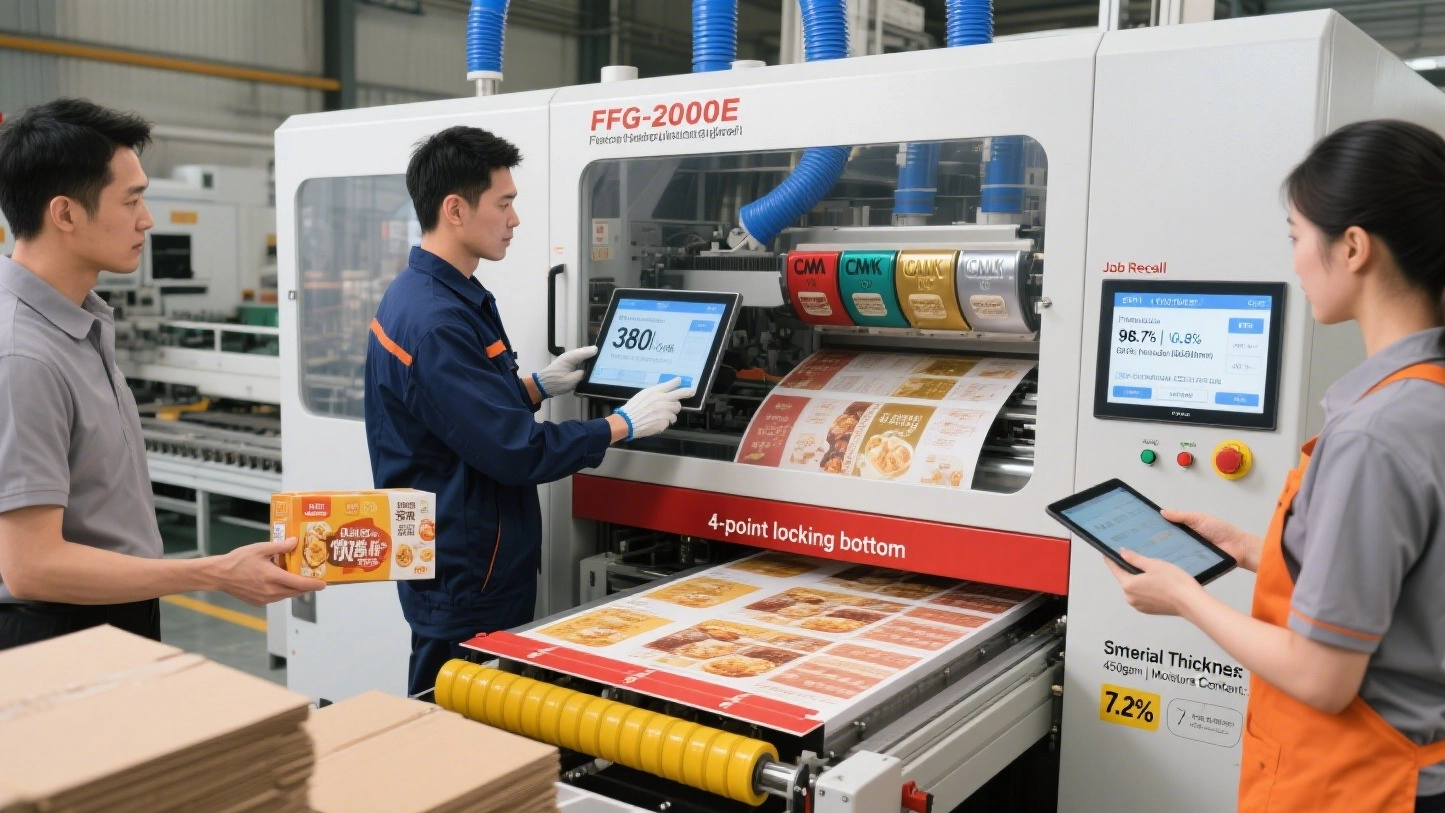
How to Operate a Flexo Folder Gluer Efficiently
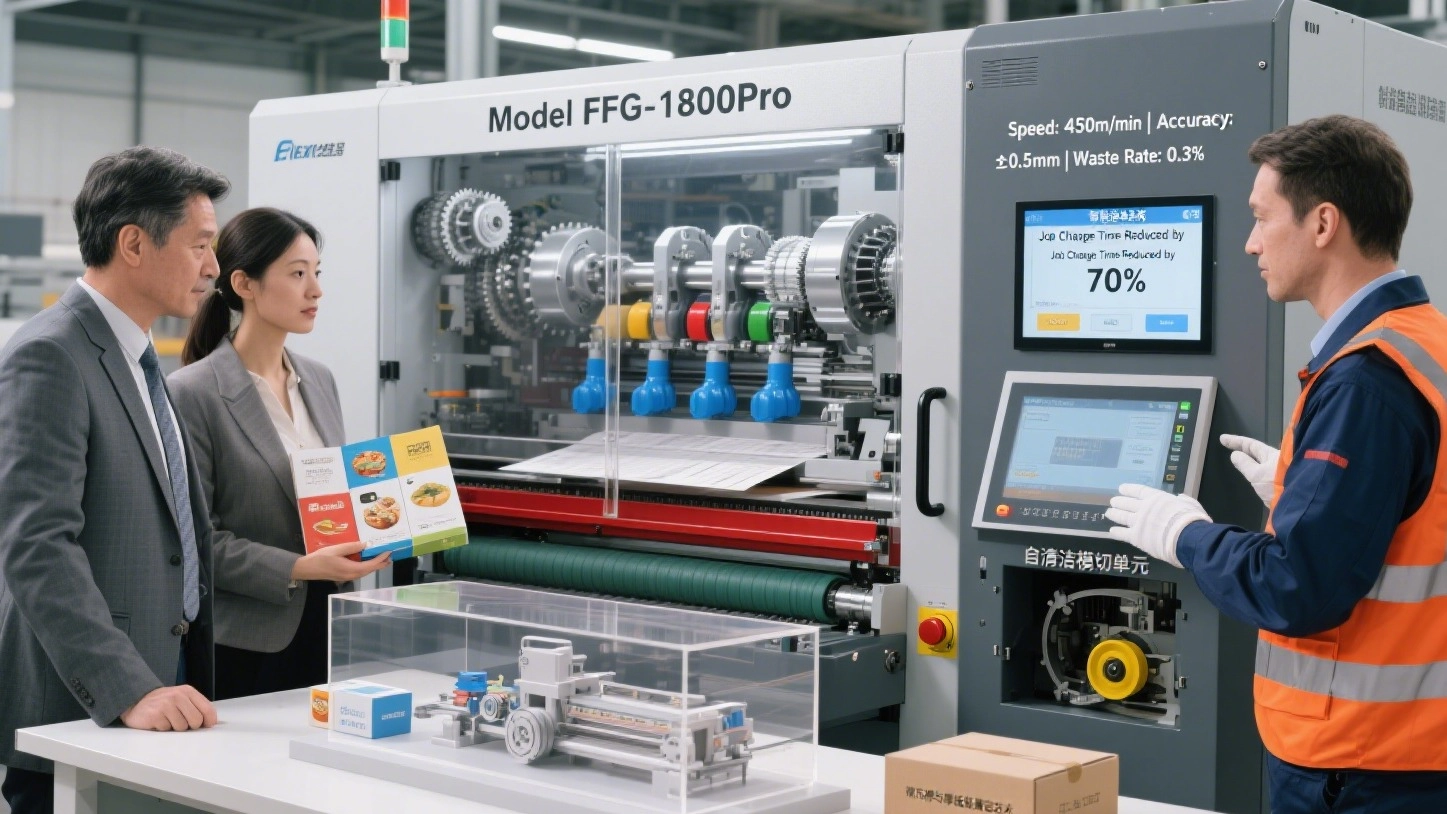
The Ultimate Guide to Flexo Folder Gluer Machines: How to Choose, Operate, and Maintain

Top Corrugated Box Printer Machine Brands
Product
What should I do if the machine jams during operation?
In case of a jam, immediately stop the machine, remove any obstructions, and check for any damage before restarting.
How do I troubleshoot common issues with the folding mechanism?
Common issues can often be resolved by checking the alignment of the folding plates and ensuring there is no debris obstructing the mechanism.
What materials are compatible with your folding carton machines?
Our machines are compatible with a wide range of materials including cardboard, corrugated board, and paperboard.
Industry Solutions
How do your machines comply with industry standards and regulations?
Our machines are manufactured to meet or exceed industry standards and regulations, ensuring safe and compliant operation.
Shipping
How are your machines packaged for safe transportation?
Our machines are securely packaged using high-quality materials to prevent damage during transit.
Leave a message
Have any questions or queries about our products? Please leave us a message here and our team will get back to you promptly.
* Rest assured that your privacy is important to us, and all information provided will be handled with the utmost confidentiality.
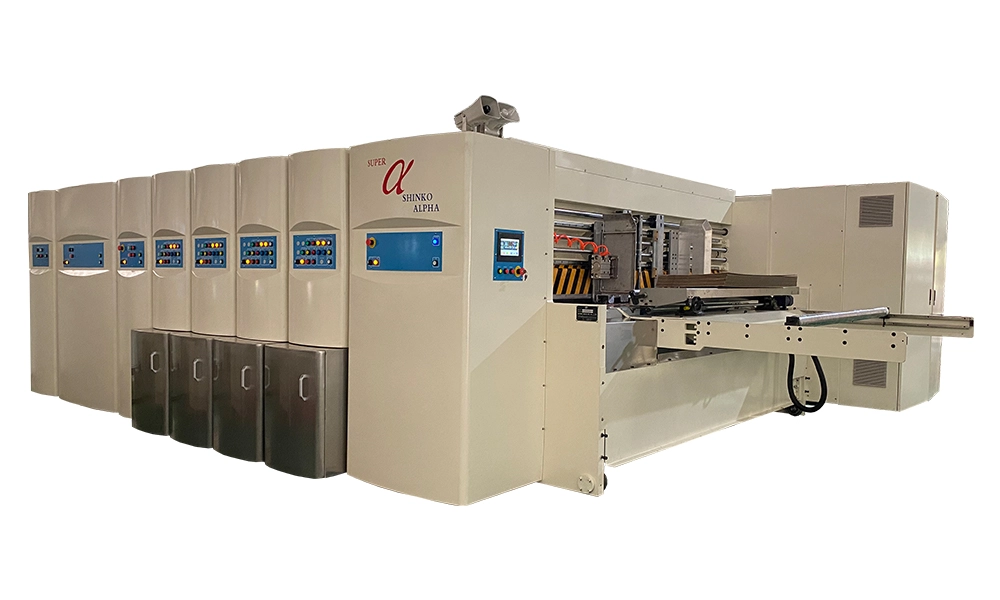
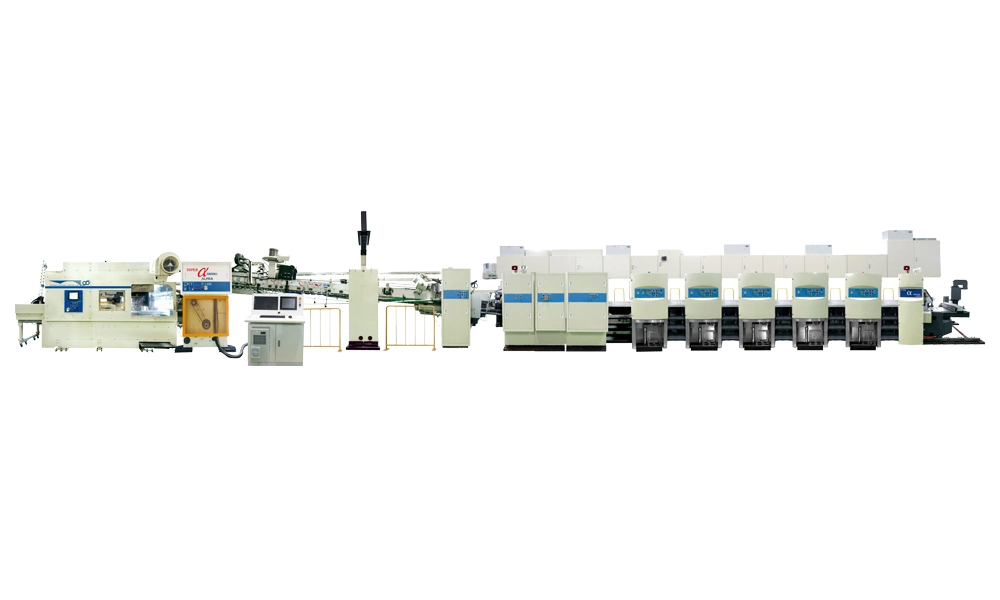
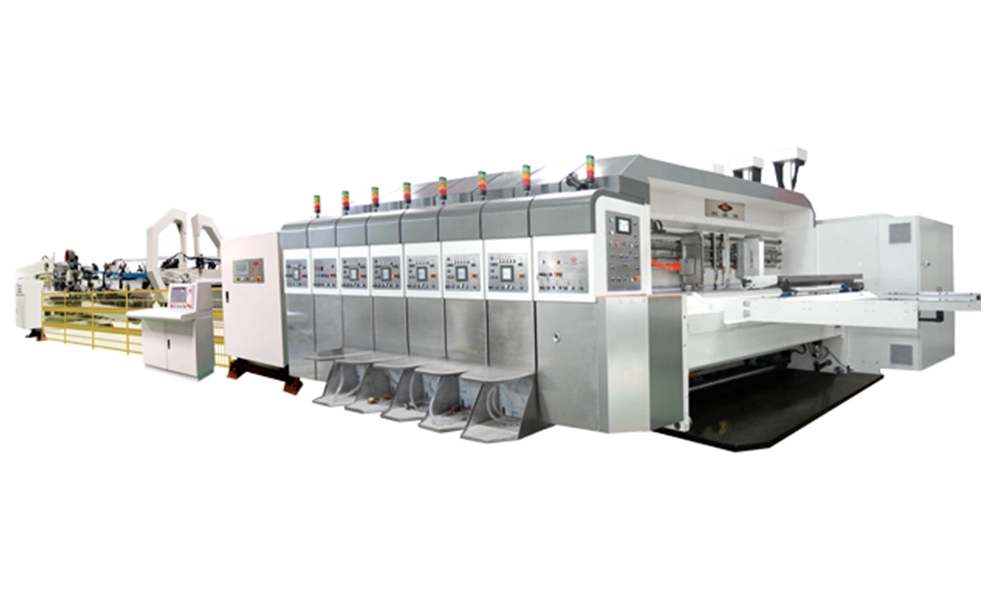
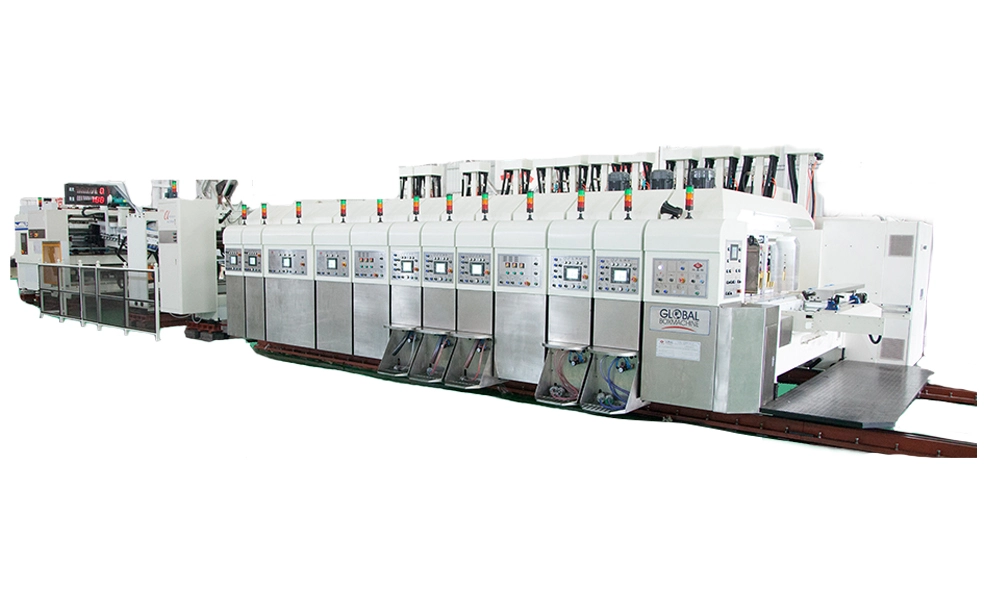
© 2025 Keshenglong & SHINKO All Rights Reserved.
Keshenglong Carton Packing Machine
Keshenglong Carton Packing Machine
Keshenglong Carton Packing Machine
Keshenglong Carton Packing Machine
Keshenglong Carton Packing Machine