How often should color settings be adjusted during a production run? | Keshenglong&Shinko Guide
For best results, adjust color settings at every significant stage: the beginning of a run, after any changeover, and at regular, documented intervals throughout the print job. This ensures high quality, minimizes waste, and maintains industry standards—all essential for competitive flexo printing operations.
- How Often Should Color Settings Be Adjusted During a Production Run?
- Importance of Color Settings in Flexo Printing
- Factors Affecting Color Stability
- Industry Best Practices for Adjusting Color Settings
- Tools and Methods for Efficient Color Control
- Additional Tips for Flexo Printer Professionals
- Authoritative Sources
How Often Should Color Settings Be Adjusted During a Production Run?
Ensuring consistent color quality is a common challenge for professionals in flexo printing. Knowing how often color settings should be adjusted during a production run delivers consistent results, reduces waste, and keeps customers satisfied. This article breaks down the best practices and industry standards every flexo printer should know.
Importance of Color Settings in Flexo Printing
- Color consistency is crucial for brand identity and customer satisfaction.
- Color variations can result from ink viscosity shifts, substrate changes, or plate wear.
- The Flexographic Technical Association (FTA) highlights color control as a top quality priority.
((https://www.flexography.org))
Factors Affecting Color Stability
- Ink density and viscosity: Temperature and press speed can alter ink characteristics.
- Substrate variability: Small changes in paper or film properties affect color absorption.
- Press conditions: Rollers, anilox wear, and doctor blade condition can introduce color shifts.
- Environmental factors: Humidity and ambient temperature impact drying and color.
Industry Best Practices for Adjusting Color Settings
How Often Should You Make Adjustments?
- Start of each run:
- Always perform an initial color check before starting.
- After major changeovers:
- Adjust after substrate, ink, or plate changes.
- At regular intervals:
- Every 30–60 minutes is typical for large jobs (FTA & IDEAlliance guidance).
- For critical jobs, more frequent checks—every 15–20 minutes—may be needed.
- Based on print length:
- For runs under two hours: Check at least 2–3 times.
- For extended runs: Schedule checks at every hour or 5,000 impressions, whichever comes first.
- Upon visual deviation:
- If operators notice color drift, check immediately regardless of schedule.
Tools and Methods for Efficient Color Control
- Spectrophotometers:
- Provide objective, repeatable measurements.
- Color management software:
- Tracks trends, flags deviations, and aids fast adjustments.
- Standardized color bars:
- Help monitor density and trap across the web.
- Consistent SOPs:
- Written procedures minimize variation from operator to operator.
Additional Tips for Flexo Printer Professionals
- Establish and document color standards at job setup.
- Keep ink formulation records for faster troubleshooting.
- Invest in regular training and color theory education for operators.
- Calibrate measurement tools weekly or as recommended by the manufacturer.
Authoritative Sources
- Flexographic Technical Association (FTA):
(https://www.flexography.org)
- IDEAlliance Print Properties Program:
(https://www.idealliance.org)
- Print Industries Market Information and Research Organization (PRIMIR):
(https://www.primir.org)
In summary:
For best results, adjust color settings at every significant stage: the beginning of a run, after any changeover, and at regular, documented intervals throughout the print job. This ensures high quality, minimizes waste, and maintains industry standards—all essential for competitive flexo printing operations.
Recommended for you
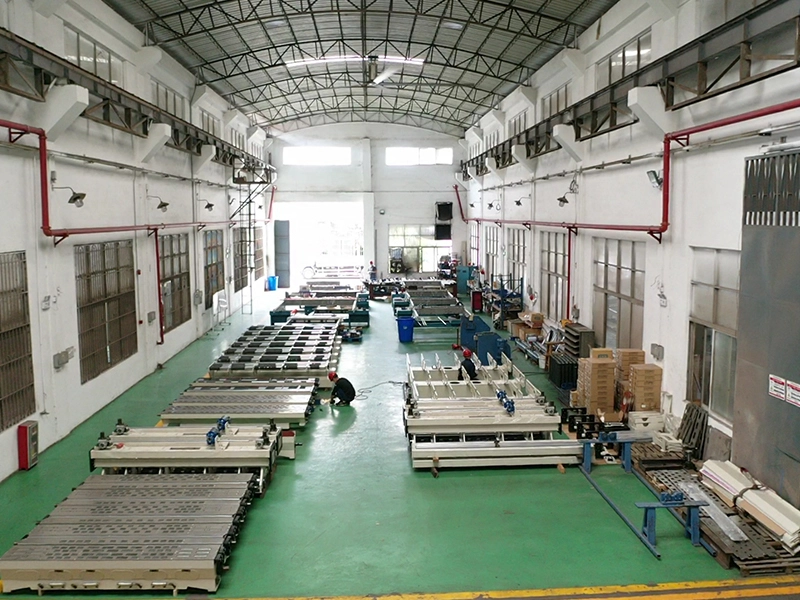
5 Common Flexo Folder Gluer Problems and Expert Solutions
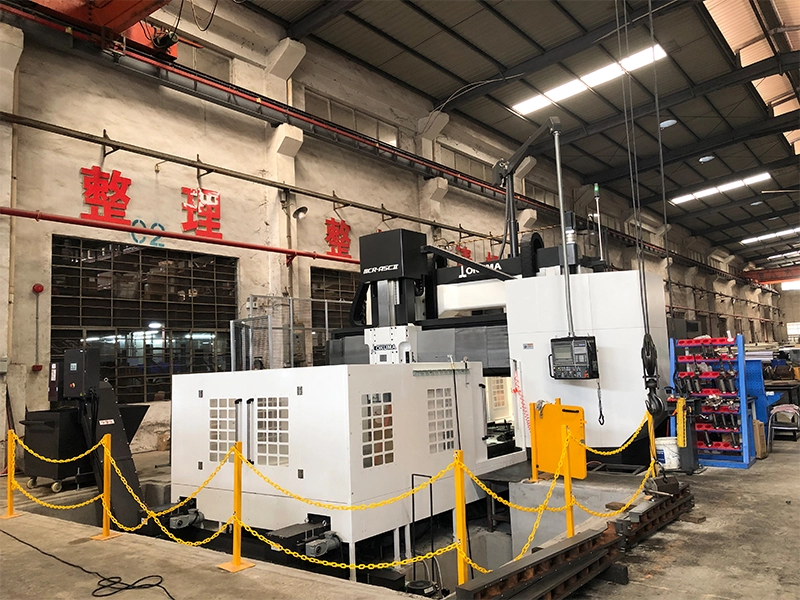
Flexo Folder Gluer Explained: Your Expert Guide
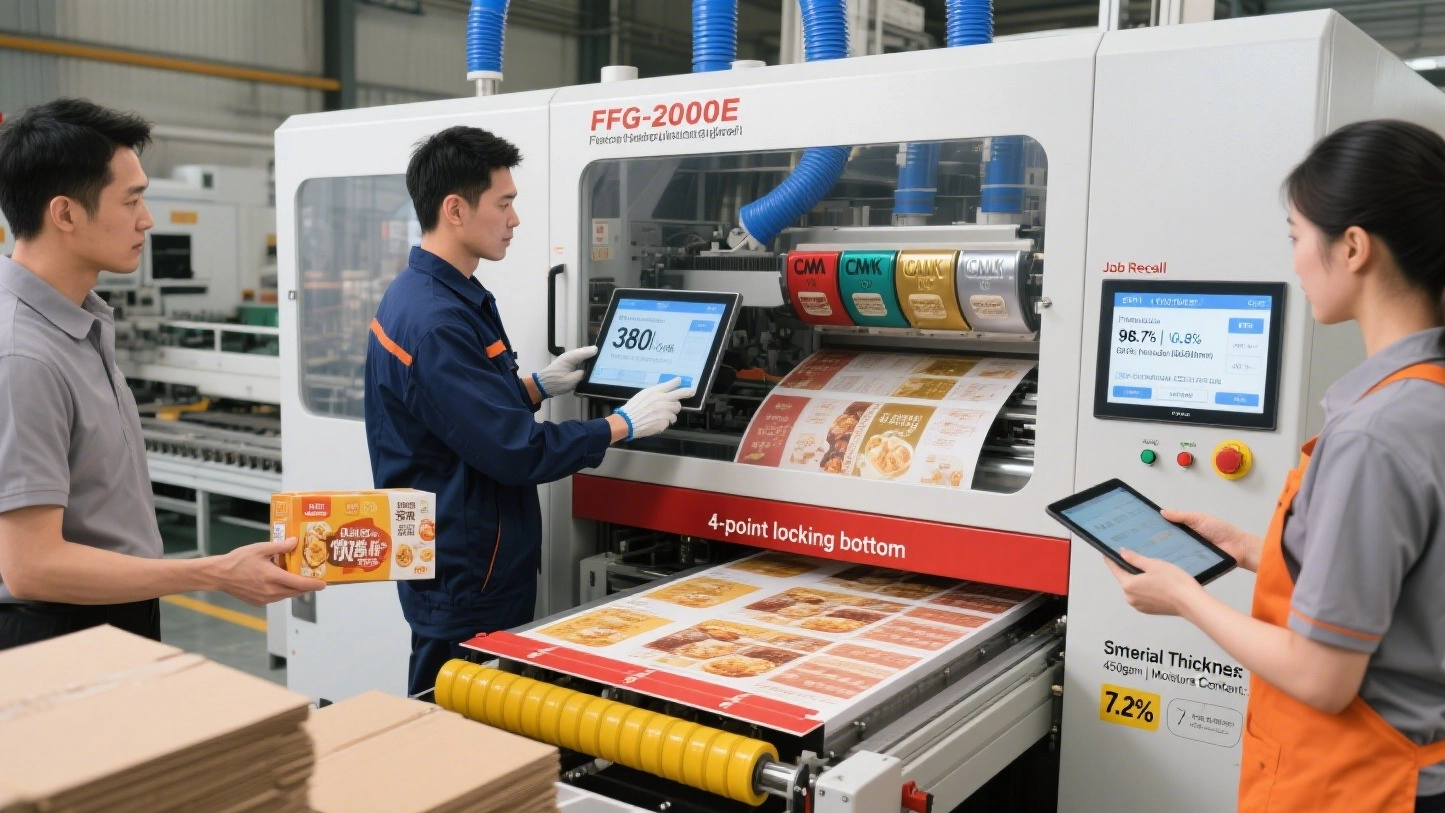
How to Operate a Flexo Folder Gluer Efficiently
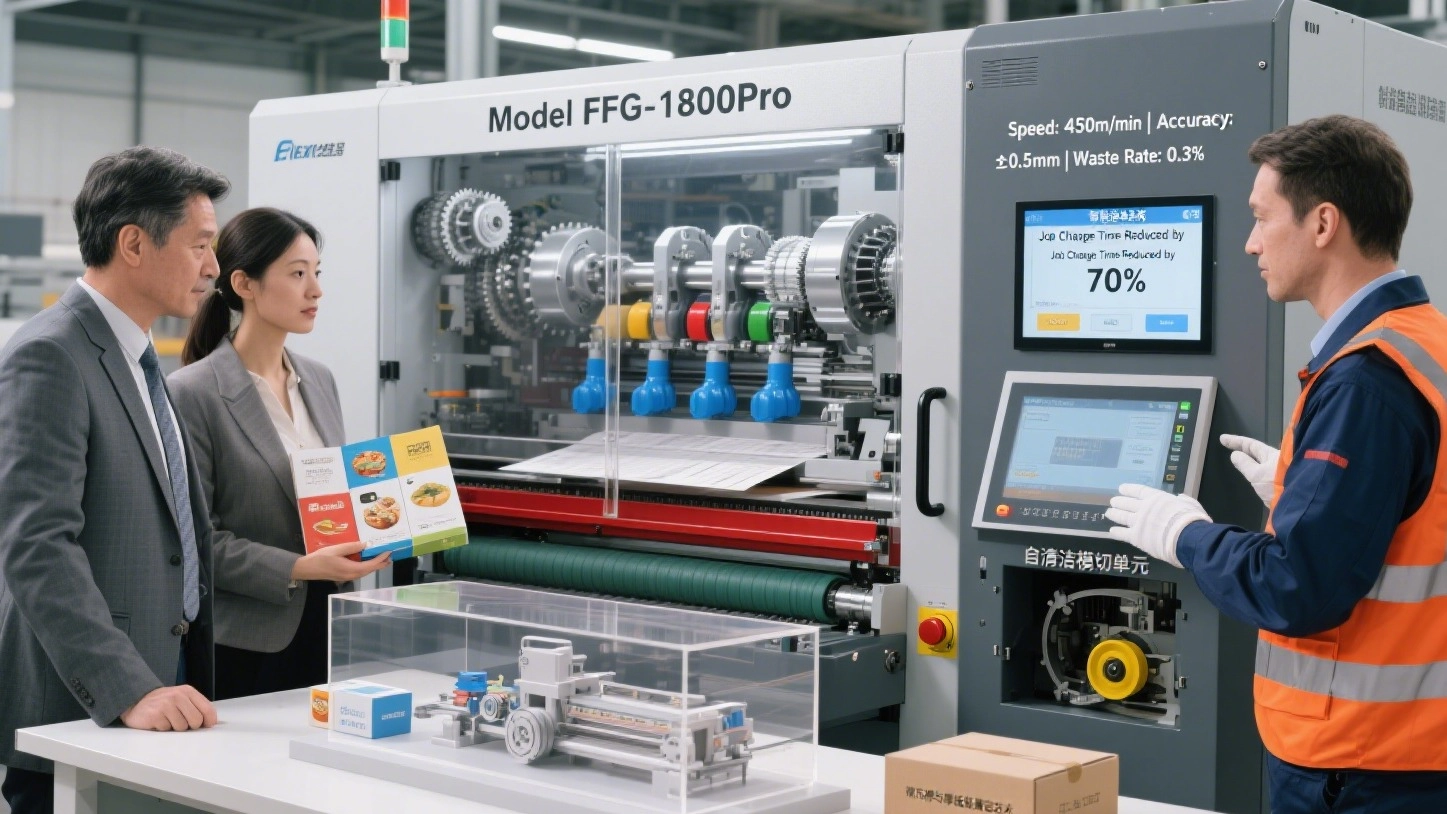
The Ultimate Guide to Flexo Folder Gluer Machines: How to Choose, Operate, and Maintain

Top Corrugated Box Printer Machine Brands
Shipping
How are your machines packaged for safe transportation?
Our machines are securely packaged using high-quality materials to prevent damage during transit.
What are the shipping costs for your folding carton machines?
Shipping costs depend on the destination, machine size, and shipping method. Contact us for a detailed quote.
Product
What should I do if the machine jams during operation?
In case of a jam, immediately stop the machine, remove any obstructions, and check for any damage before restarting.
What materials are compatible with your folding carton machines?
Our machines are compatible with a wide range of materials including cardboard, corrugated board, and paperboard.
Industry Solutions
What industries typically use your folding carton machines?
Our machines are used in various industries including food and beverage, pharmaceuticals, cosmetics, and electronics.
Leave a message
Have any questions or queries about our products? Please leave us a message here and our team will get back to you promptly.
* Rest assured that your privacy is important to us, and all information provided will be handled with the utmost confidentiality.
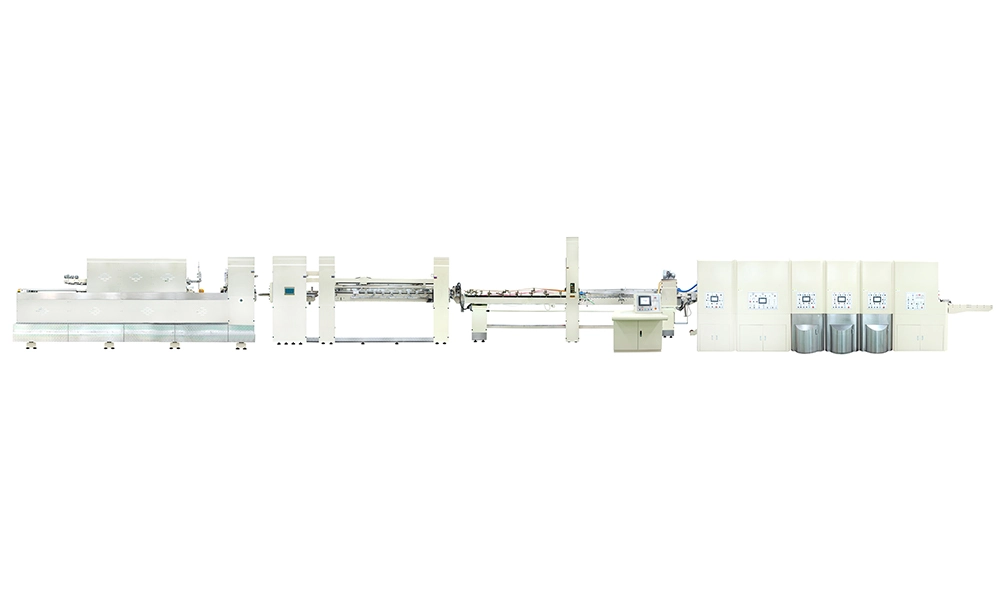
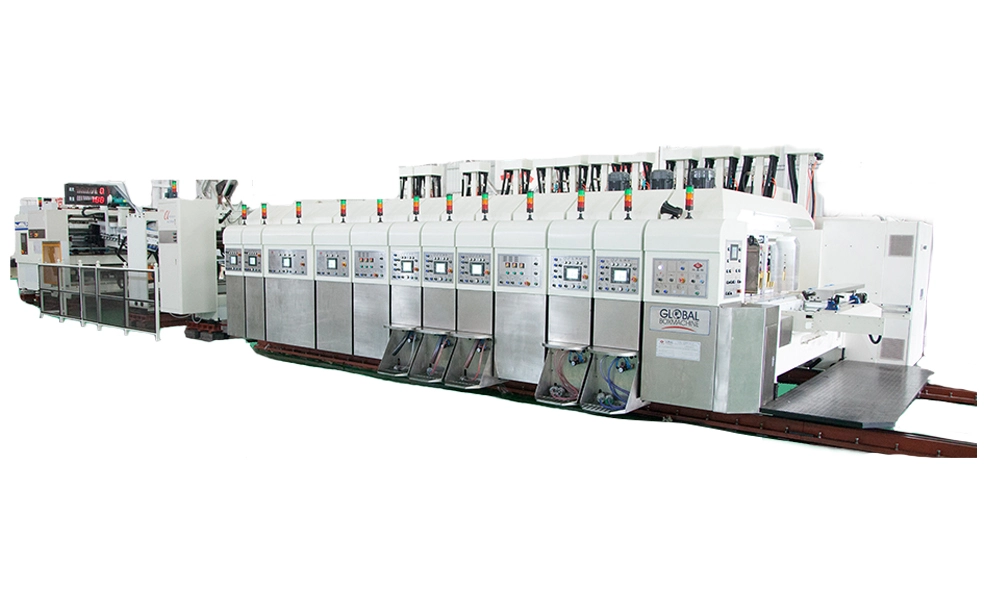
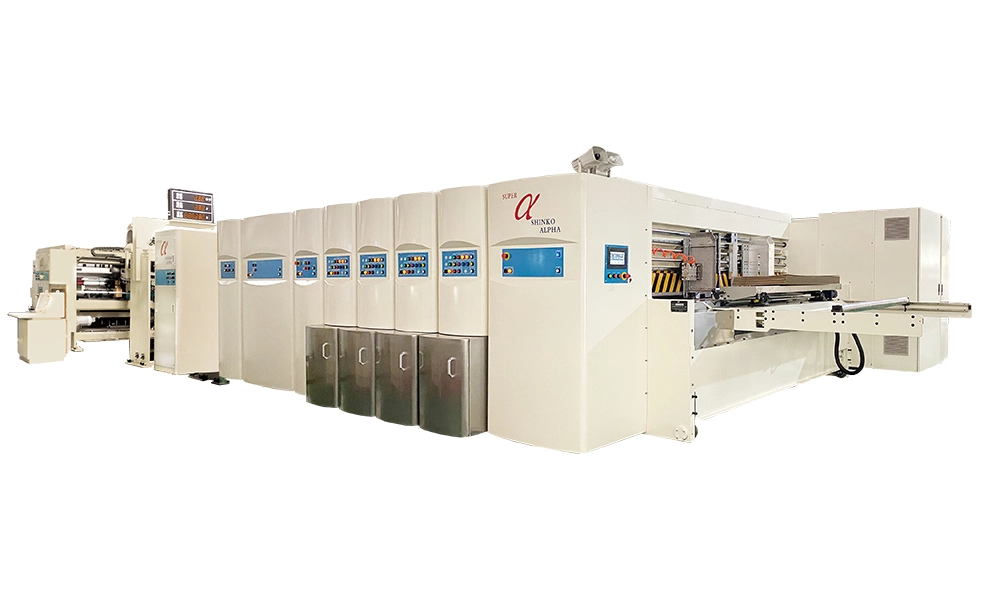
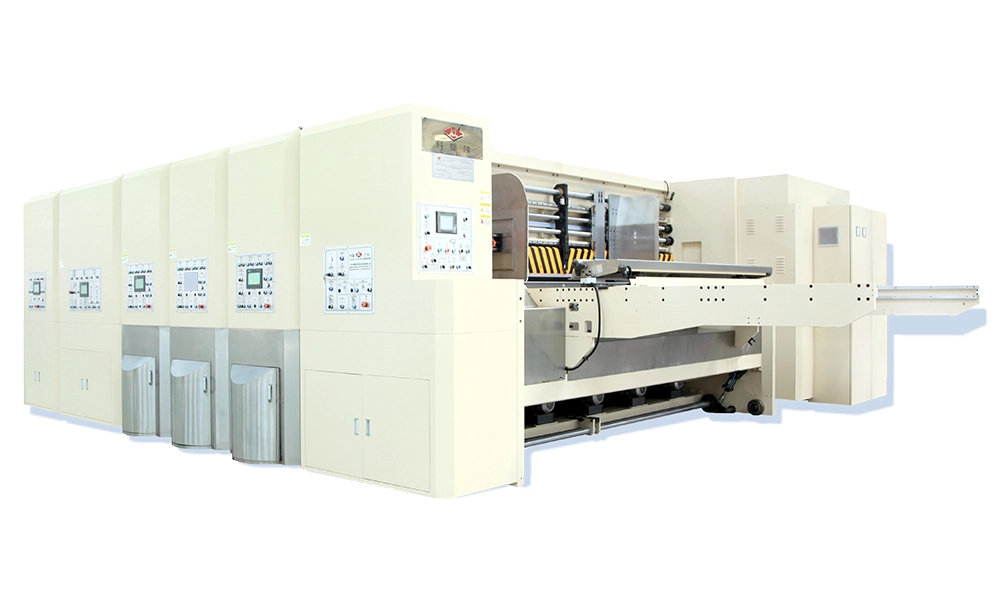
© 2025 Keshenglong & SHINKO All Rights Reserved.
Keshenglong Carton Packing Machine
Keshenglong Carton Packing Machine
Keshenglong Carton Packing Machine
Keshenglong Carton Packing Machine
Keshenglong Carton Packing Machine