Is the slotting and die-cutting process fully automated in the equipment? | Keshenglong&Shinko Expert Guide
Modern flexo printer-slotter-die-cutters offer high levels of automation, though not fully 'lights-out' for all job types. They feature automated setup, digital controls, and integrated systems, significantly boosting efficiency, precision, and waste reduction. Benefits include rapid changeovers, reduced labor dependency, and enhanced quality. Technologies like IIoT and servo drives underpin these advancements. Buyers should evaluate automation based on operational needs, integration, and manufacturer support for optimal investment.
- Is Slotting and Die-Cutting Fully Automated in Modern Flexo Printing Equipment?
- The Current State of Automation in Flexo Converting
- Primary Benefits of Investing in Highly Automated Slotting and Die-Cutting
- What Level of Automation Can You Realistically Expect?
- Key Technologies Driving Automation in Flexo
- What to Look For When Investing in Automated Solutions
Is Slotting and Die-Cutting Fully Automated in Modern Flexo Printing Equipment?
The quest for full automation, often termed lights-out manufacturing, is a significant driver in many industries, including corrugated packaging and flexo printing. When considering new flexo printer-slotter-die-cutters, one common question for buyers is the extent to which the slotting and die-cutting processes are truly automated. While achieving 100% human-free operation from raw material to finished product is still evolving and typically reserved for highly specialized, high-volume repetitive tasks, modern flexo equipment has made tremendous strides towards significant automation, offering substantial benefits.
The Current State of Automation in Flexo Converting
In 2024, the landscape of flexo printer-slotter-die-cutters is characterized by advanced semi-automation and integrated intelligent systems rather than complete lights-out operations for all job types. Top-tier machinery now features highly automated setup, precise digital controls, and sophisticated integration of processes. For instance, recent industry reports and equipment showcases indicate that leading manufacturers are focusing on reducing setup times from hours to minutes, sometimes even under 5 minutes for complex jobs, largely due to automated positioning, quick-lock tooling, and self-cleaning systems. While the human operator still plays a crucial role in oversight, quality checks, and complex problem-solving, the physical intervention required for setup, adjustments, and monitoring has been drastically minimized. This isn't full automation in the sense of a totally unassisted machine, but rather high automation that significantly enhances efficiency.
Primary Benefits of Investing in Highly Automated Slotting and Die-Cutting
For flexo printer businesses, the shift towards higher automation translates directly into compelling competitive advantages:
- Increased Efficiency & Throughput: Automated systems drastically cut down on changeover times and reduce manual intervention during runs. This means more jobs per shift and higher overall production capacity. For example, some advanced machines boast production speeds upwards of 300-400 sheets per minute for corrugated, with minimal setup time between jobs.
- Enhanced Precision & Quality: Digital controls and servo-driven systems ensure repeatable accuracy, leading to fewer defects and higher-quality finished products. This is critical for intricate die-cut designs and precise slotting, where even slight deviations can lead to significant waste.
- Reduced Waste & Material Costs: With better accuracy and faster setup, waste due to misregistration or trial-and-error adjustments is significantly minimized. Industry data suggests waste reduction of 15-25% can be achieved through advanced automation.
- Lower Labor Dependency & Costs: While not eliminating operators, automation reduces the need for highly skilled, hands-on intervention during routine tasks, allowing operators to oversee multiple machines or focus on more complex, value-added activities. This can help mitigate skilled labor shortages and reduce operational costs.
- Improved Operator Safety: Automating hazardous or repetitive tasks reduces the risk of workplace injuries.
What Level of Automation Can You Realistically Expect?
When evaluating new flexo equipment, expect a high degree of automation in specific functions rather than across the entire workflow without any human interface. Key areas of automation include:
- Automated Setup & Changeover: This is perhaps the most impactful area. Features like automatic plate mounting, anilox roll changes, quick-lock die setups, and automated registration systems allow for job changes in minutes. Machines can often store job parameters for quick recall.
- Digital Control & Diagnostics: HMI (Human-Machine Interface) touchscreens for precise control of all parameters (impression settings, ink flow, registration, cutting depth). Integrated diagnostics and predictive maintenance systems provide real-time performance data and alert operators to potential issues before they become critical failures.
- Servo-Driven Systems: Individual servo motors for each print unit, slotting head, and die-cutting station provide unparalleled precision, speed, and energy efficiency, allowing for synchronized control and quick adjustments.
- Integrated Vision Systems: Cameras and sensors for automatic registration, quality inspection, and defect detection, ensuring consistent output and reducing the need for manual inspection.
- Automated Material Handling (Emerging): While less common for diverse jobs, some high-volume lines integrate robotic palletizing or automated guided vehicles (AGVs) for material movement, further reducing manual labor.
Key Technologies Driving Automation in Flexo
Several technological advancements underpin the current levels of automation:
- Industrial Internet of Things (IIoT) & Industry 4.0 Integration: Machines are increasingly connected, allowing for data exchange, remote monitoring, and integration with broader factory management systems (MES/ERP). This enables predictive maintenance, optimized scheduling, and real-time performance analysis.
- Advanced Robotics & Cobots: While full robotic loading/unloading is still niche, collaborative robots (cobots) are being explored for tasks like material feeding or offloading, particularly for repetitive, heavy tasks.
- Artificial Intelligence (AI) & Machine Learning (ML): AI algorithms are being used for process optimization, anomaly detection, and even predictive quality control, learning from past runs to fine-tune machine parameters automatically.
- Digital Workflow Solutions: Software integration from pre-press to post-press reduces manual data entry and potential errors, streamlining the entire production workflow.
What to Look For When Investing in Automated Solutions
When procuring new flexo equipment, consider these aspects related to automation:
- Level of Automation vs. Your Needs: Do you need highly automated setup for frequent short runs, or robust semi-automation for long runs? Match the machine's capabilities to your typical job mix.
- Ease of Integration: Can the new machine integrate seamlessly with your existing MES/ERP systems and other factory equipment?
- User-Friendliness: Despite high automation, an intuitive HMI is crucial for operators to manage and troubleshoot effectively.
- Service & Support: Ensure the manufacturer provides robust technical support, remote diagnostics capabilities, and accessible parts/service for these sophisticated automated systems.
- Scalability: Can the machine's automation features be upgraded or expanded in the future as your business needs evolve?
- Energy Efficiency: Highly automated, servo-driven machines often offer significant energy savings compared to older, less automated models.
In conclusion, while fully automated may still be a futuristic ideal for all flexo operations, the modern flexo printer-slotter-die-cutter is undeniably a highly automated machine, engineered to deliver unparalleled efficiency, precision, and cost savings. Investing in these advanced solutions is a strategic move for any flexo converter aiming to stay competitive and future-proof their operations.
Recommended for you
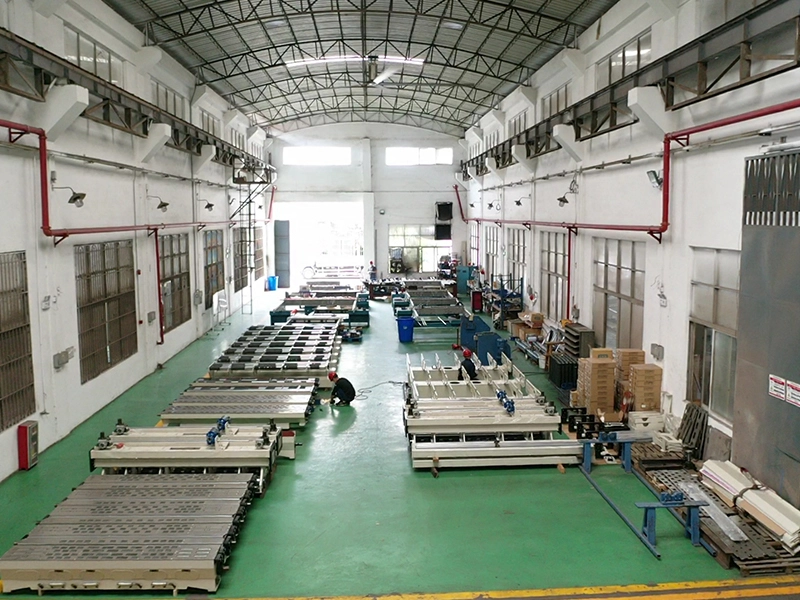
5 Common Flexo Folder Gluer Problems and Expert Solutions
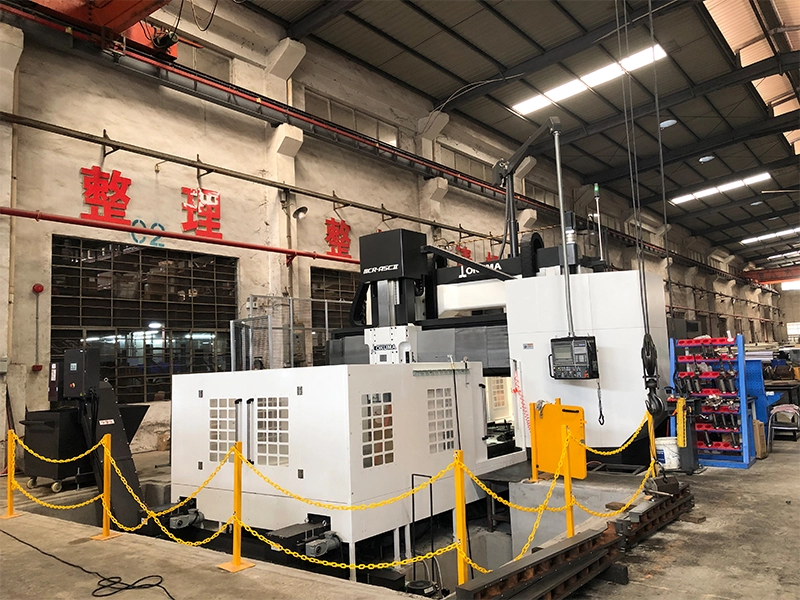
Flexo Folder Gluer Explained: Your Expert Guide
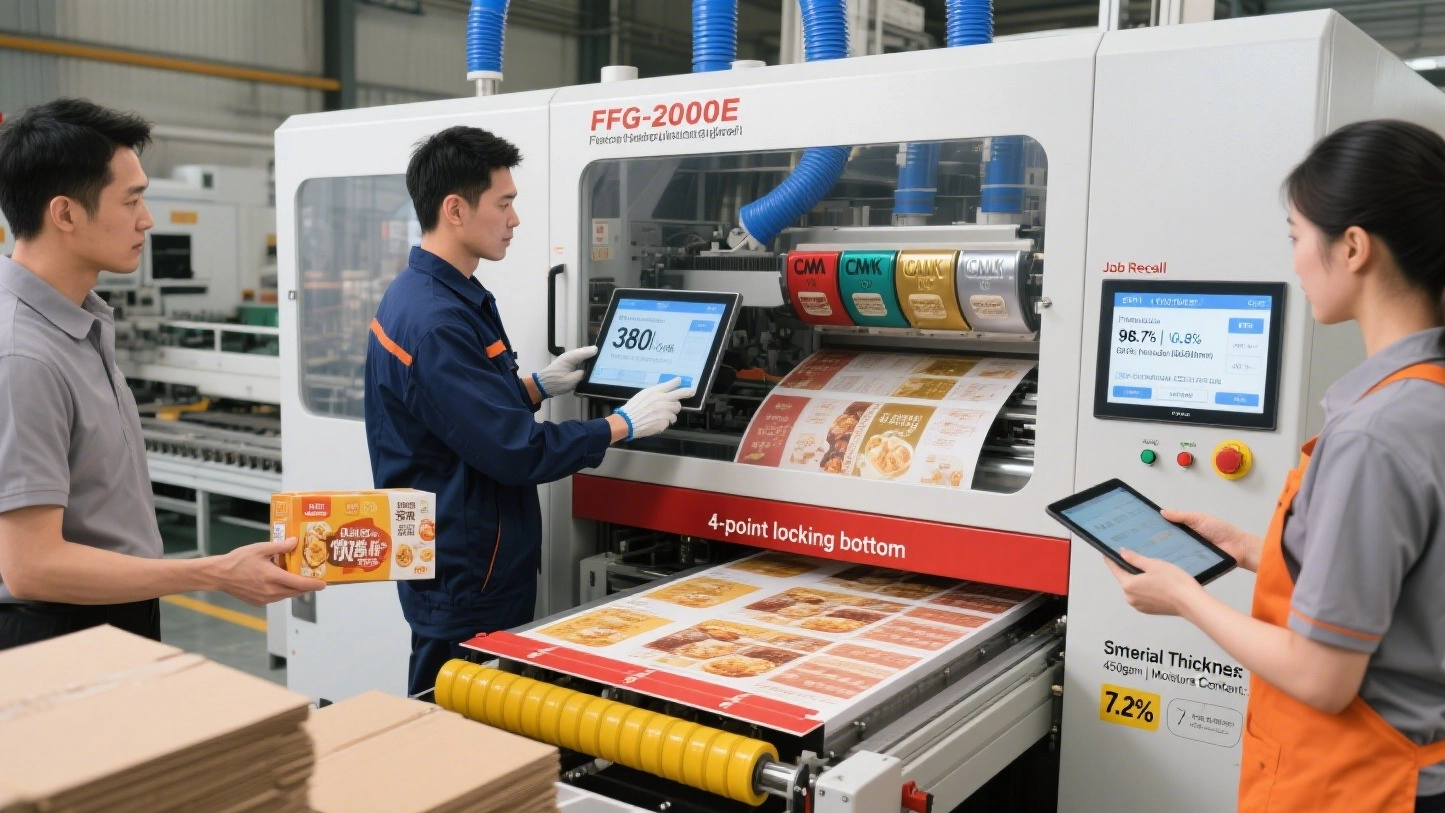
How to Operate a Flexo Folder Gluer Efficiently
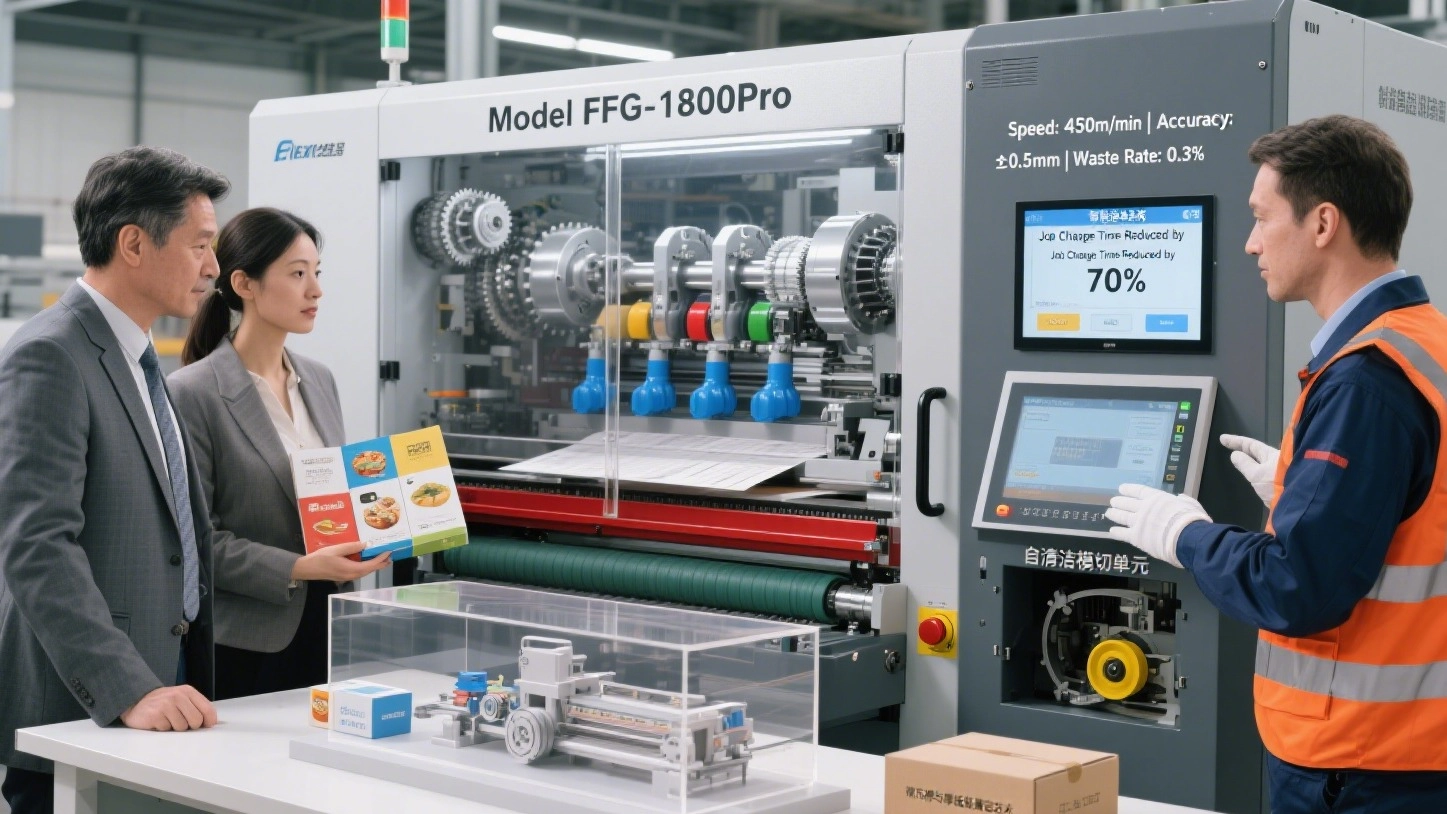
The Ultimate Guide to Flexo Folder Gluer Machines: How to Choose, Operate, and Maintain

Top Corrugated Box Printer Machine Brands
Industry Solutions
How can your folding carton machines benefit my packaging business?
Our machines increase production efficiency, reduce labor costs, and ensure high-quality, consistent carton production.
How can your machines improve my production workflow?
By automating carton production, our machines streamline your workflow, increase output, and reduce downtime.
Product
Can your machines handle custom carton designs?
Yes, our machines can be customized to handle various carton designs and specifications.
How do I troubleshoot common issues with the folding mechanism?
Common issues can often be resolved by checking the alignment of the folding plates and ensuring there is no debris obstructing the mechanism.
Shipping
Do you provide installation services upon delivery?
Yes, we offer on-site installation and training services to ensure your machine is set up correctly.
Leave a message
Have any questions or queries about our products? Please leave us a message here and our team will get back to you promptly.
* Rest assured that your privacy is important to us, and all information provided will be handled with the utmost confidentiality.
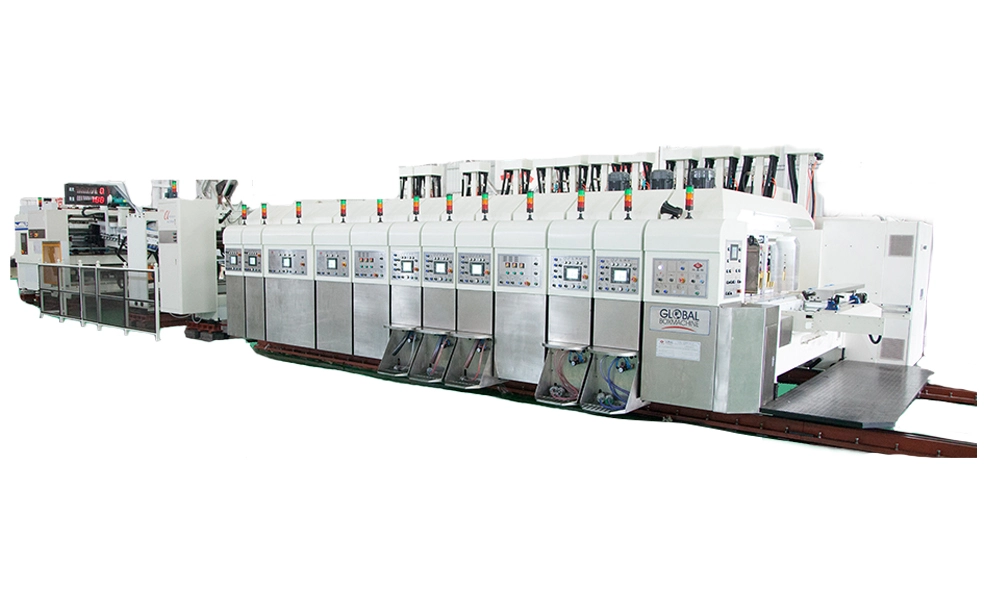
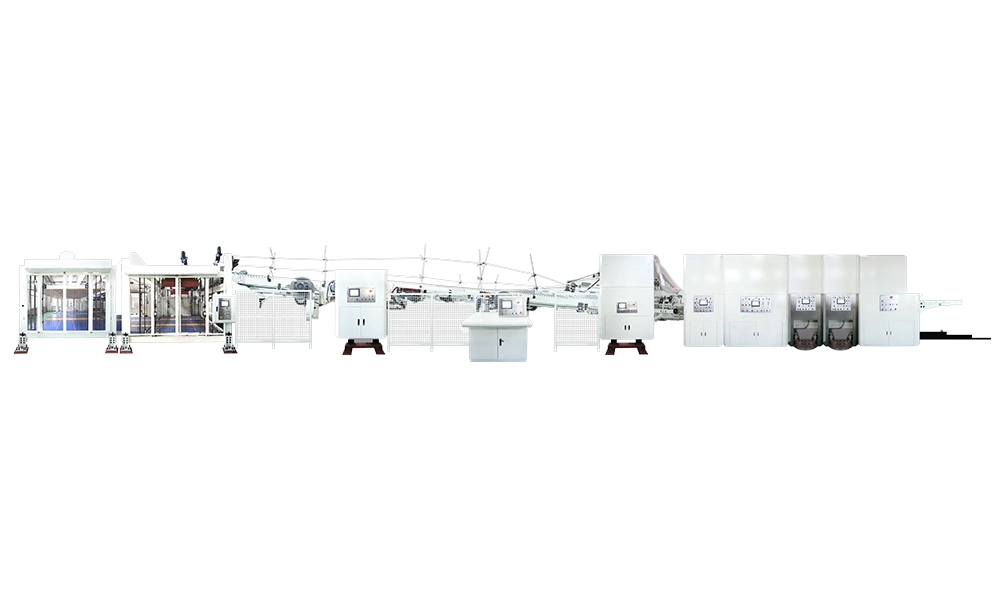
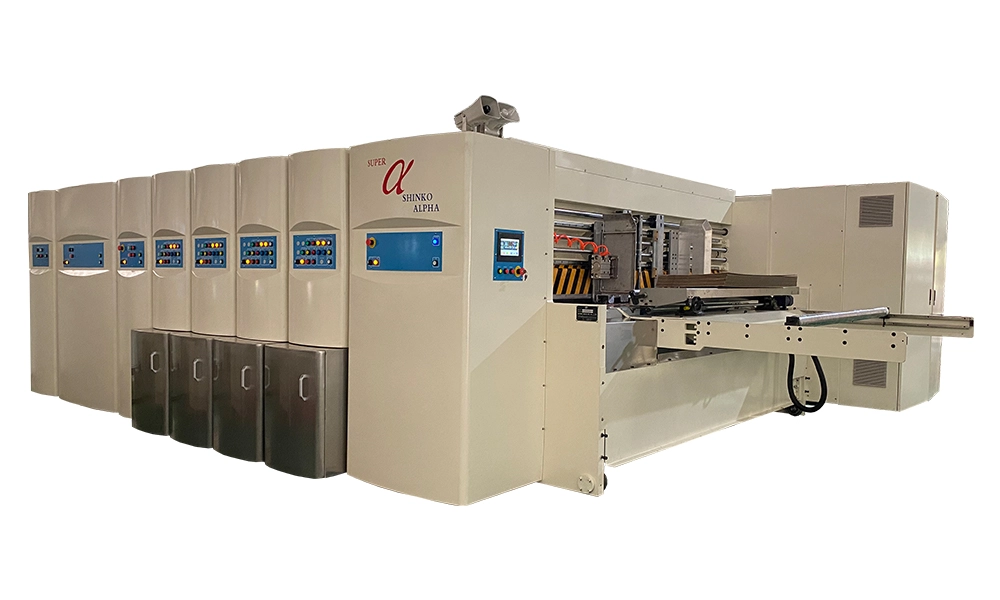
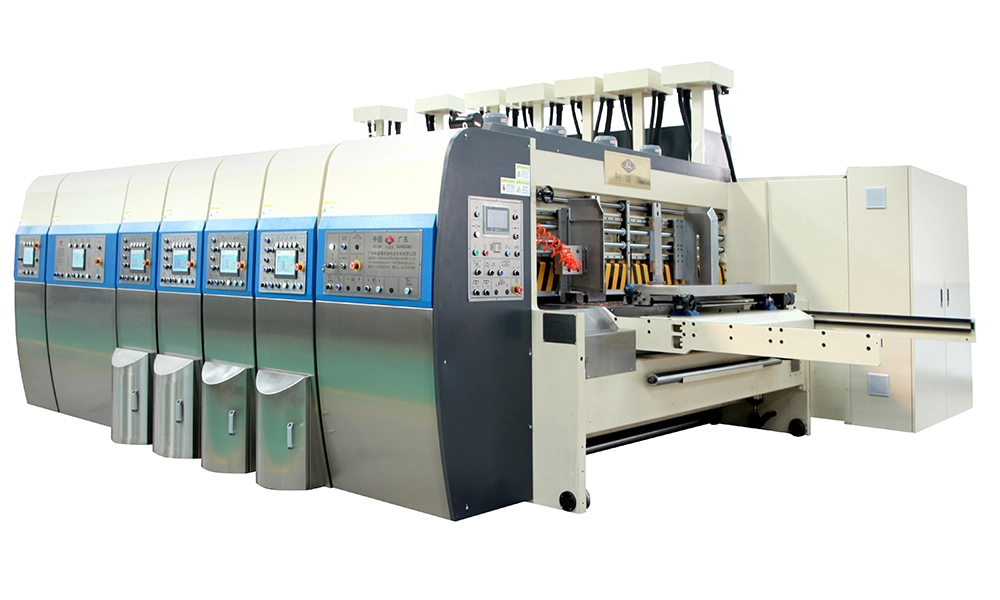
© 2025 Keshenglong & SHINKO All Rights Reserved.
Keshenglong Carton Packing Machine
Keshenglong Carton Packing Machine
Keshenglong Carton Packing Machine
Keshenglong Carton Packing Machine
Keshenglong Carton Packing Machine