Can the flexo printing machine perform double-sided printing on corrugated cardboard? | Keshenglong&Shinko Expert Guide
For industry professionals, understanding flexo printer capabilities is crucial. Standard flexo machines excel in single-sided corrugated printing, but true simultaneous double-sided printing in one pass is generally not feasible due to technical complexities. This article explores how double-sided print effects are achieved, inherent challenges, and key considerations for your procurement strategy, including alternative methods like digital printing for specific needs.
- Can Flexo Printing Machines Perform Double-Sided Printing on Corrugated Cardboard?
- Is True Single-Pass Double-Sided Flexo Printing on Corrugated Possible?
- How is a Double-Sided Print Effect Typically Achieved on Corrugated Cardboard with Flexo?
- What Are the Key Technical Challenges of Attempting Two-Sided Flexo Printing for Corrugated?
- When Is Double-Sided Printing on Corrugated Cardboard Necessary or Beneficial?
- Alternatives to Flexo for Double-Sided Corrugated Printing.
Can Flexo Printing Machines Perform Double-Sided Printing on Corrugated Cardboard?
Is True Single-Pass Double-Sided Flexo Printing on Corrugated Possible?
In the realm of corrugated packaging, conventional flexographic printing machines are primarily designed for single-sided operation. Unlike some narrow-web flexo presses used for labels or flexible packaging, which can incorporate turn bars for front-and-back printing in a single pass, the robust nature and thickness of corrugated cardboard present significant challenges. Therefore, for corrugated, a true single-pass, simultaneous double-sided print capability on a standard flexo press is not common and generally not achievable. The complexity of handling rigid, often large sheets, ensuring precise registration on both sides, and managing ink drying within a single pass makes it impractical for high-volume corrugated production.How is a Double-Sided Print Effect Typically Achieved on Corrugated Cardboard with Flexo?
While simultaneous double-sided printing is rare, achieving a double-sided print effect with flexo on corrugated is done through a multi-pass approach. This typically involves:1. First Pass: Printing on one side of the corrugated sheet.2. Flipping and Second Pass: The sheets are then either manually or automatically flipped, and fed back through the same flexo press or a separate one to print the second side.This method requires careful handling to maintain registration, particularly for designs that need to align across both sides or if multiple colors are involved on the second pass. It significantly increases production time and material handling, making it less efficient than a theoretical single-pass solution. For internal printing visible upon opening (e.g., e-commerce boxes), only the inside liner needs printing, which is done as part of a two-pass process.What Are the Key Technical Challenges of Attempting Two-Sided Flexo Printing for Corrugated?
Attempting two-sided printing on corrugated cardboard, even with a multi-pass approach, introduces several technical hurdles:- Registration Accuracy: Maintaining precise alignment between the first and second print passes, especially on large, flexible corrugated sheets, is challenging. Any slight shift can lead to misregistration, impacting print quality.
- Ink Drying and Set-off: Flexo inks are water-based or UV-curable, but corrugated board's absorbency varies. Printing the second side too soon before the first side is fully dry risks ink set-off (transferring wet ink to the next sheet or rollers) or smudging. Adequate drying time or inter-station drying is critical.
- Board Stability and Warp: Corrugated cardboard can be prone to warp or curl due to moisture absorption from water-based inks, affecting subsequent passes. Ensuring flat and stable board handling throughout both print runs is crucial.
- Material Handling Complexity: Flipping large, heavy corrugated sheets efficiently and accurately for the second pass adds complexity, labor, and potential for damage or misfeeds.
- Cost and Efficiency: The need for two separate passes doubles the press time, labor, and energy consumption, making the process less economical for high-volume standard packaging.
When Is Double-Sided Printing on Corrugated Cardboard Necessary or Beneficial?
The demand for double-sided printing on corrugated has grown, driven by evolving market trends, particularly in:- E-commerce Packaging: To enhance the unboxing experience, brands are increasingly printing on the inside of shipping boxes. This allows for branding, marketing messages, or unique designs to surprise and engage customers upon opening, transforming a utilitarian box into a marketing touchpoint.
- Retail-Ready Packaging (RRP) / Shelf-Ready Packaging (SRP): Some RRP designs require internal printing to display product information or branding once the outer layer is removed for shelf display.
- Promotional and Display Packaging: Specific promotional campaigns or point-of-purchase (POP) displays might benefit from internal graphics to reinforce a message or extend brand storytelling.
- Sustainability Messaging: Brands might use the inside of the box to communicate sustainability initiatives, recycling instructions, or other brand values.
Alternatives to Flexo for Double-Sided Corrugated Printing.
Given the limitations of conventional flexo for true double-sided corrugated printing, other technologies offer viable alternatives, especially for high-quality or on-demand needs:- Digital Printing: Single-pass digital inkjet presses for corrugated are rapidly advancing. Machines like the EFI Nozomi C18000 Plus or the HP PageWide T1190s are capable of extremely high-quality, high-speed printing and can often handle printing on both sides either in-line (with a turning mechanism) or through efficient two-pass operations with excellent registration. Digital offers flexibility for variable data and short runs, making it ideal for customized unboxing experiences.
- Litho-Lamination (Offset + Corrugated): This process involves offset printing high-resolution graphics onto a thin paper liner, which is then laminated onto a single-face corrugated board. This method provides the highest graphic quality, making it suitable for High Quality retail packaging or displays where photographic imagery and fine details are crucial. Double-sided effects are achieved by laminating a separate pre-printed liner to the inside, or by printing directly onto the inside liner before it's assembled.
- Pre-Print Flexo: While still a flexo process, this involves printing the liner before it is combined with the fluting to form the corrugated board. This allows for higher print quality and better registration than post-print flexo. If both inner and outer liners need specific printing, they would both be pre-printed before the board is constructed.
Recommended for you
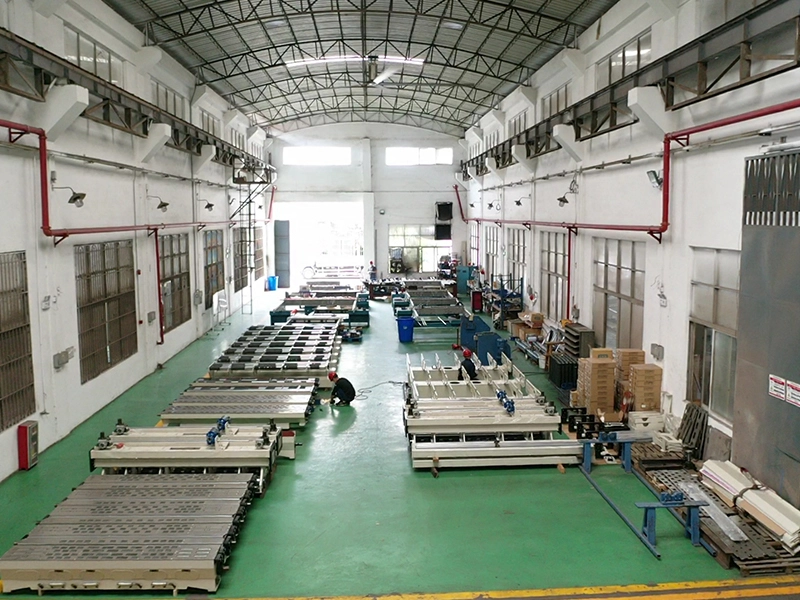
5 Common Flexo Folder Gluer Problems and Expert Solutions
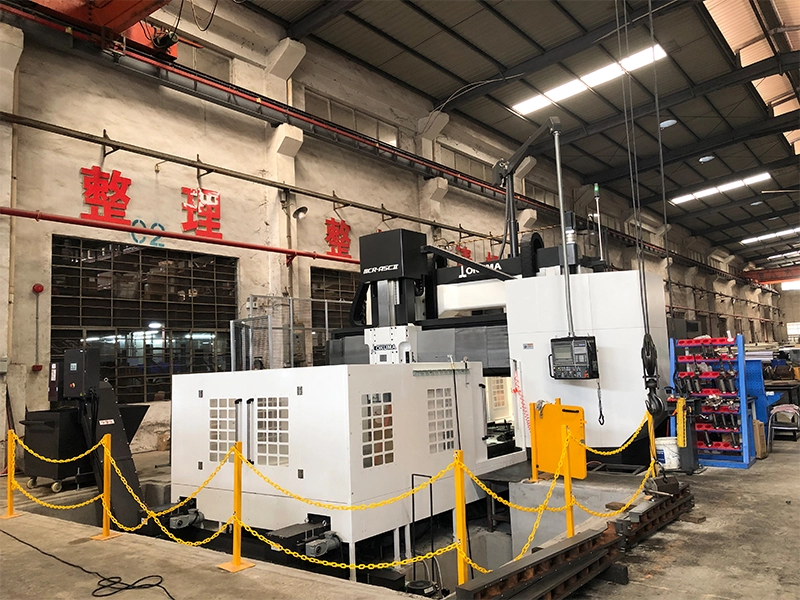
Flexo Folder Gluer Explained: Your Expert Guide
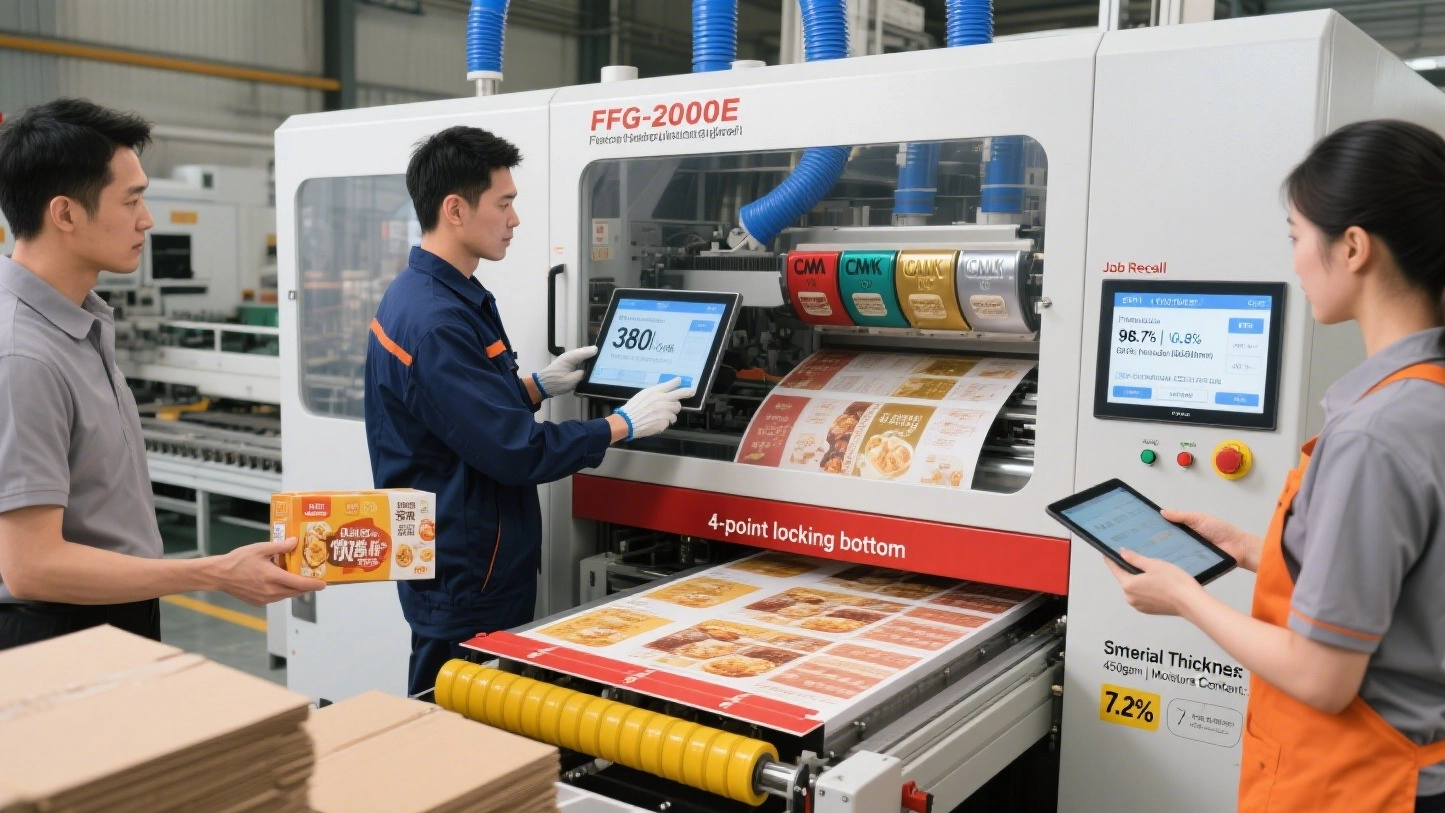
How to Operate a Flexo Folder Gluer Efficiently
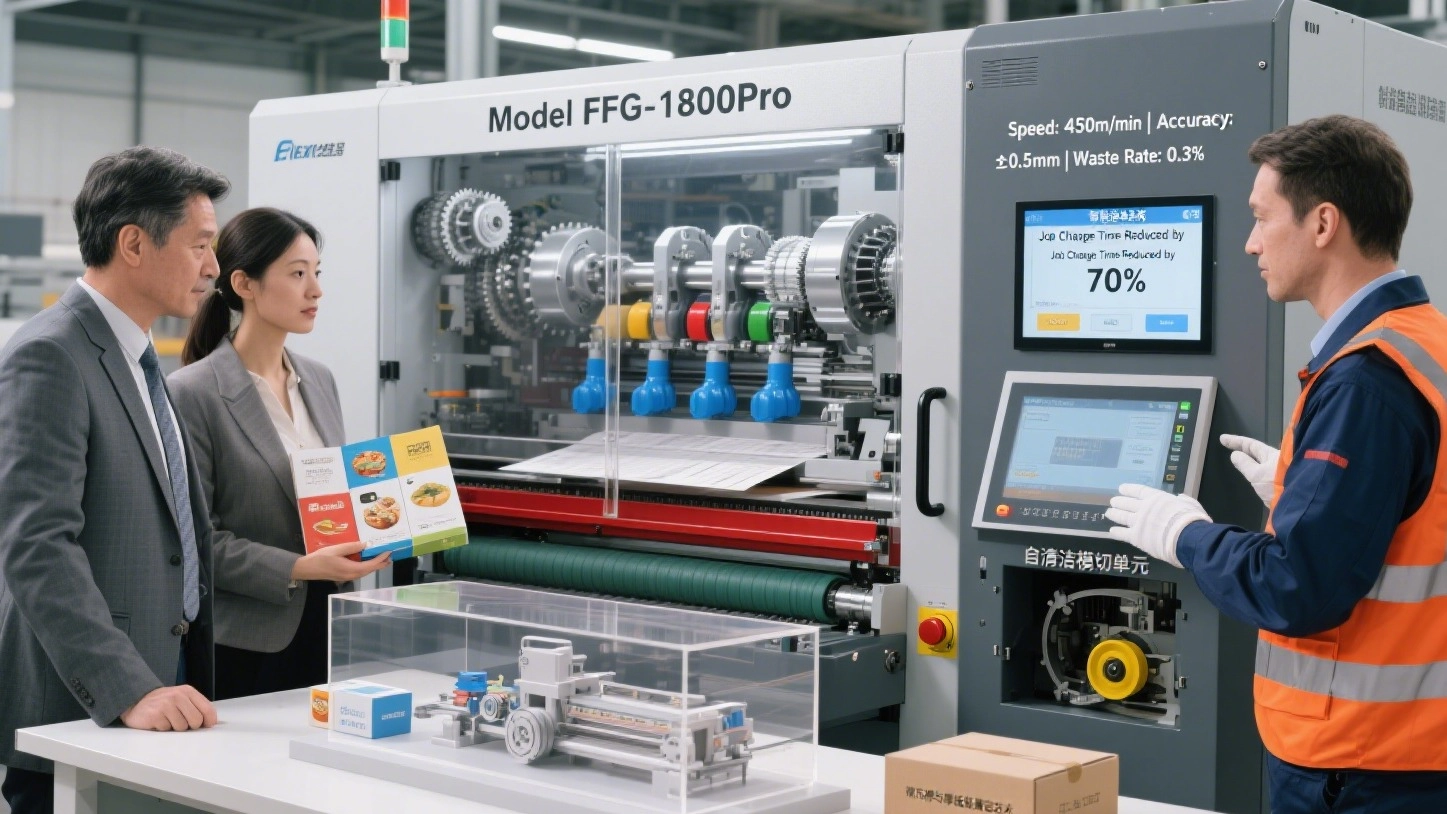
The Ultimate Guide to Flexo Folder Gluer Machines: How to Choose, Operate, and Maintain

Top Corrugated Box Printer Machine Brands
Shipping
What are the shipping dimensions and weight of your folding carton machines?
Shipping dimensions and weight vary by model; please refer to the specific product details for accurate information.
Product
What is the maximum speed of your folding carton machines?
Our machines can operate at speeds of up to 150 cartons per minute, depending on the model and carton complexity.
Can your machines handle custom carton designs?
Yes, our machines can be customized to handle various carton designs and specifications.
Industry Solutions
What is the lifespan of your folding carton machines?
With proper maintenance, our machines are built to last for many years, providing long-term value for your investment.
What kind of technical support do you offer for industry applications?
We provide comprehensive technical support, including installation, maintenance, and troubleshooting services.
Leave a message
Have any questions or queries about our products? Please leave us a message here and our team will get back to you promptly.
* Rest assured that your privacy is important to us, and all information provided will be handled with the utmost confidentiality.
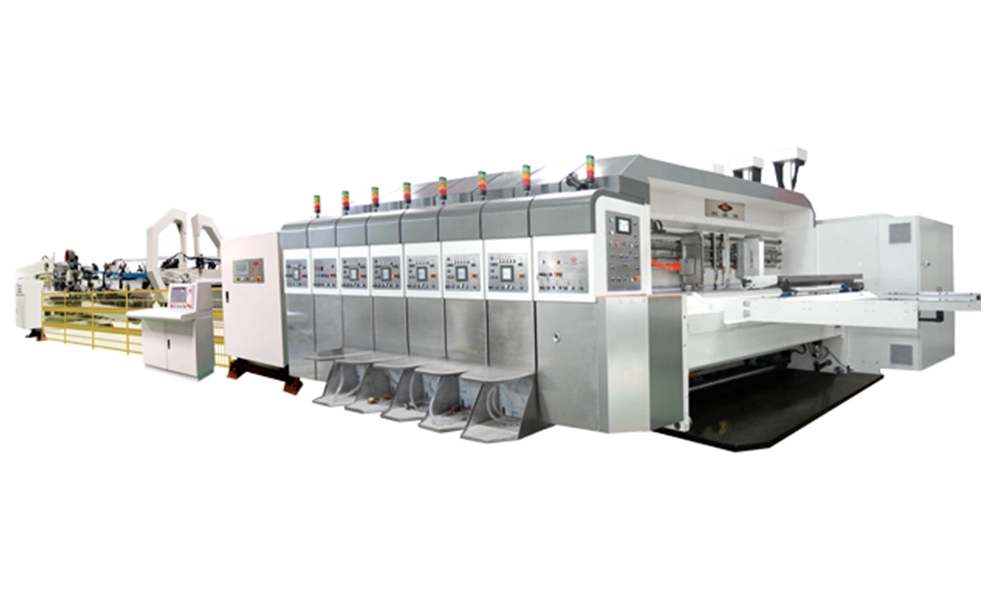
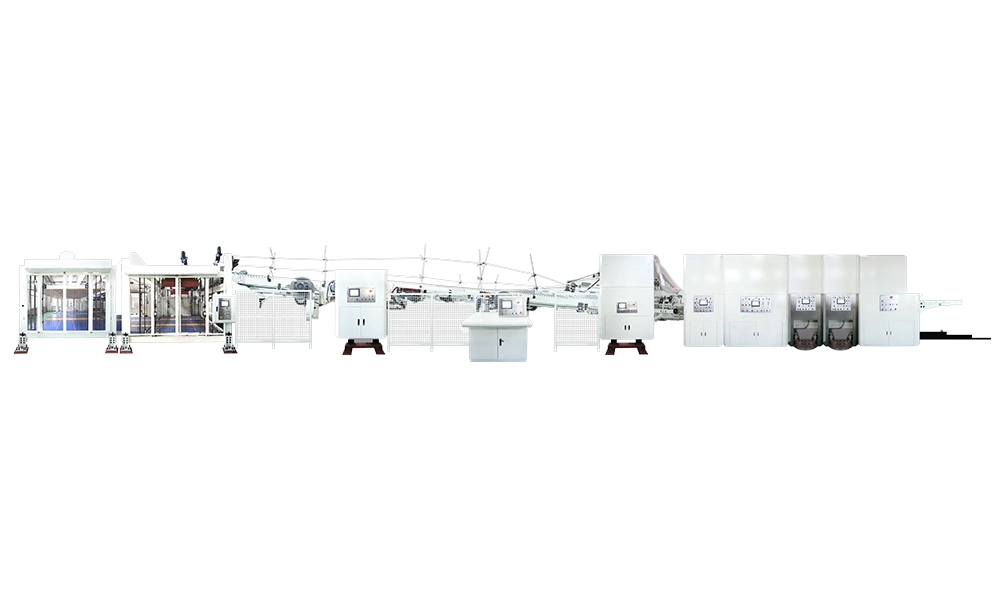
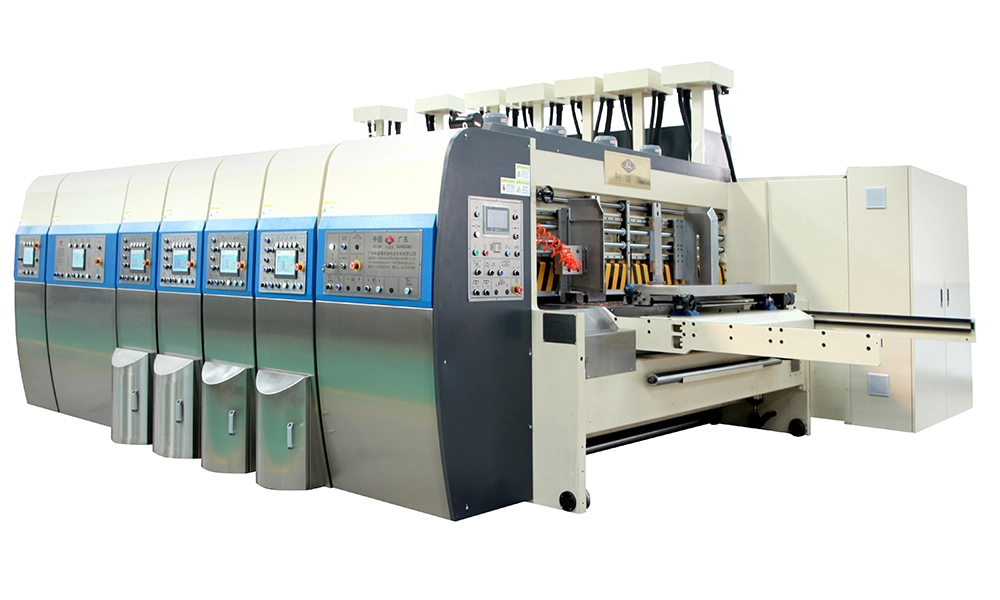
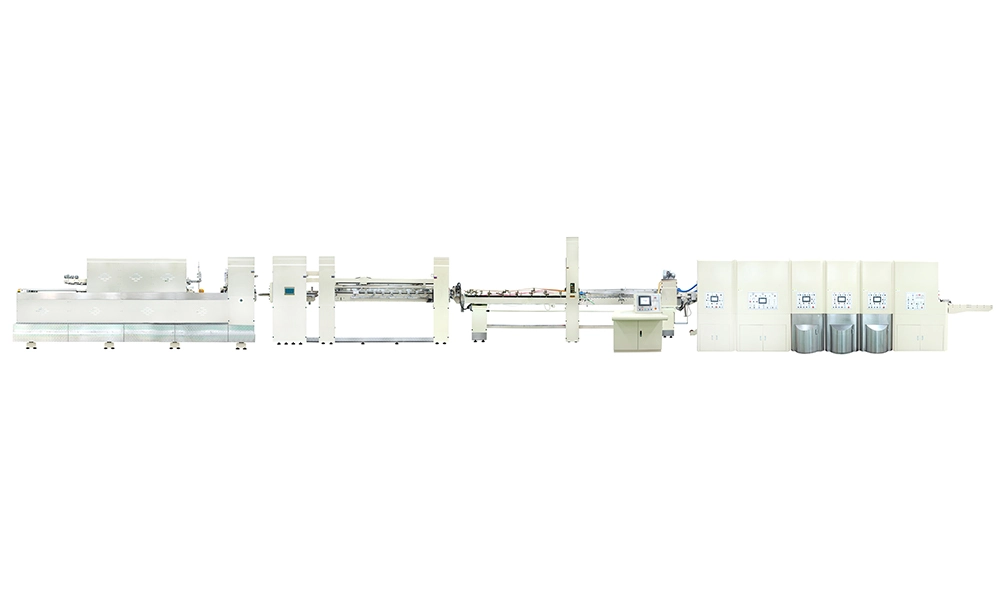
© 2025 Keshenglong & SHINKO All Rights Reserved.
Keshenglong Carton Packing Machine
Keshenglong Carton Packing Machine
Keshenglong Carton Packing Machine
Keshenglong Carton Packing Machine
Keshenglong Carton Packing Machine