What does a die cutting machine do? | Keshenglong&Shinko Expert Guide
Die-cutting machines are crucial for transforming flexo-printed rolls into finished labels and packaging. For flexo professionals repurchasing, understanding technology nuances, workflow integration, and innovations is vital. This guide covers core functions, evaluates types, outlines key investment factors, and offers insights into optimizing production efficiency and waste reduction for a profitable upgrade.
- What Does a Die-Cutting Machine Do? An Essential Guide for Flexo Printers
- Beyond the Cut: Why is Die Cutting Crucial for Flexo Printing?
- What are the Main Types of Die-Cutting Technologies Relevant to Flexo Production?
- Key Considerations When Repurchasing a Die-Cutting Machine for Your Flexo Print Shop
- How Can Die-Cutting Technology Optimize Your Flexo Workflow and Reduce Waste?
- What are the Latest Innovations in Die Cutting for the Flexo Industry?
What Does a Die-Cutting Machine Do? An Essential Guide for Flexo Printers
In the dynamic world of flexographic printing, precision and efficiency are paramount. While flexo presses lay down vibrant designs, it's the die-cutting machine that transforms continuous rolls of printed material into the finished, perfectly shaped labels, flexible packaging, or specialty products we encounter daily. For flexo print shop owners and operators contemplating a machinery repurchase, understanding the intricacies of modern die-cutting technology is not just about replacing old equipment; it's about investing in enhanced capabilities, greater efficiency, and a competitive edge.
At its core, a die-cutting machine uses a specialized cutting tool, known as a die, to cut, crease, perforate, or emboss material into specific shapes. Unlike simple cutting, die cutting ensures consistent, repeatable shapes at high speeds, which is indispensable for large-volume production in the flexo industry.
Beyond the Cut: Why is Die Cutting Crucial for Flexo Printing?
Die cutting is the critical post-press process that brings flexo-printed products to life. Without it, a roll of beautifully printed labels remains just that – a roll. For labels, die cutting defines the very shape of each individual label, creating intricate designs, simple squares, or unique contours. For flexible packaging, it can create pouches, sachets, or specialized cut-outs. In essence, it completes the product by:
- Shaping & Sizing: Precisely cutting individual units from a printed web.
- Waste Matrix Stripping: Removing the surrounding waste material (matrix) to leave only the finished product on the liner or ready for further processing.
- Adding Functionality: Incorporating features like perforations for easy tearing, kiss-cuts for peel-off labels, or scoring for folding lines in cartons.
- Ensuring Consistency: Delivering identical cuts across millions of units, vital for brand consistency and automated application systems.
Often, die-cutting units are integrated directly inline with flexo presses, forming a seamless, high-speed production line from raw material to finished product.
What are the Main Types of Die-Cutting Technologies Relevant to Flexo Production?
The flexo industry primarily relies on a few key die-cutting technologies, each with its advantages:
- Rotary Die Cutting: This is the workhorse of the flexo label and flexible packaging industry. It uses cylindrical dies mounted on a rotating cylinder. As the web passes between the die and an anvil roll, the die cuts or scores the material.
- Pros: Extremely high speed (often exceeding 500-1000 feet per minute for continuous runs), high accuracy (e.g., +/- 0.005 inches), ideal for long runs and pressure-sensitive labels.
- Cons: High initial tooling cost for custom rotary dies, less flexible for very short runs or constantly changing designs.
- Flatbed Die Cutting: While less common for inline flexo label production due to its slower speed, flatbed systems are prevalent for thicker materials, folding cartons, or specialized, non-label converting. They use a flat die pressed onto the material.
- Pros: Excellent for thick materials and complex creasing, lower tooling cost for short runs.
- Cons: Slower speeds, not suitable for high-volume label production.
- Laser Die Cutting: A rapidly growing technology, especially for digital finishing lines. Laser cutters use a focused laser beam to cut the material based on a digital file, eliminating the need for physical dies.
- Pros: No tooling costs (apart from machine investment), instant job changeovers, ideal for intricate designs, short runs, and variable data applications.
- Cons: Slower than rotary for high-volume production, potential for burnt edges on some materials, higher energy consumption per cut than rotary.
Key Considerations When Repurchasing a Die-Cutting Machine for Your Flexo Print Shop
When upgrading or expanding, flexo professionals should look beyond the basic function and consider the total cost of ownership and operational efficiency:
- Speed & Throughput: Does it match or exceed your flexo press speed? Can it handle your projected production volumes?
- Accuracy & Registration: Critical for multi-lane labels and precise cuts. Look for advanced registration systems (e.g., vision systems).
- Tooling Investment & Lifespan: Evaluate the cost of new dies and their expected durability. Consider magnetic cylinders for flexible dies.
- Material Versatility: Can it effectively cut various substrates you use (paper, film, foil, laminates, tag stock)?
- Automation Features: Automatic matrix stripping, waste rewinding, automatic job setup, and quick-change systems significantly reduce downtime and labor costs.
- Integration & Modularity: Can it seamlessly integrate with your existing or future flexo presses? Are there modular options for future upgrades (e.g., adding lamination, hot foil, slitting)?
- Ease of Use & Maintenance: User-friendly interfaces reduce operator training time. Robust construction and accessible components minimize maintenance downtime.
- Energy Efficiency: Modern machines often offer significant energy savings compared to older models, contributing to lower operating costs.
- After-Sales Support & Parts Availability: Crucial for ensuring maximum uptime and quick resolution of any issues.
How Can Die-Cutting Technology Optimize Your Flexo Workflow and Reduce Waste?
Optimizing die-cutting operations directly impacts the profitability of your flexo print shop:
- Reduced Setup Times: Machines with automated or semi-automated setup features, quick-change die systems, and pre-registration capabilities drastically cut downtime between jobs.
- Efficient Waste Matrix Stripping: Advanced stripping mechanisms ensure clean, fast removal of waste material, preventing jams and increasing overall throughput. Some systems can rewind waste separately, improving recycling efforts.
- Precision & Consistency: High-precision die cutting minimizes material waste due to misregistration or poor cuts, especially important with expensive substrates.
- Higher Speeds: The ability to run at faster speeds directly translates to higher output per shift, fulfilling orders quicker and increasing capacity.
- Multi-Up Production: Maximizing the number of labels or products cut across the web width boosts efficiency significantly.
By investing in a modern, well-engineered die-cutting solution, you can expect tangible improvements in production speed, material utilization, and overall operational efficiency, directly contributing to your bottom line.
What are the Latest Innovations in Die Cutting for the Flexo Industry?
The die-cutting landscape is continually evolving, driven by demands for greater flexibility, efficiency, and integration:
- Hybrid Finishing Lines: Combining traditional rotary die cutting with digital technologies like laser cutting or digital embellishment (e.g., digital varnish, foil) in a single pass.
- Automated Job Changeovers: Further advancements in automation are reducing manual intervention for die loading, registration, and waste stripping.
- Smart Tooling: Dies equipped with RFID or other sensors to track usage, monitor performance, and alert for maintenance, optimizing die lifespan.
- Advanced Vision Systems: Cameras and intelligent software for ultra-precise registration, defect detection, and quality control, especially vital for complex multi-layer labels or variable data.
- Modular & Configurable Systems: Machines designed with a modular approach, allowing print shops to add new capabilities (e.g., screen printing units, slitting, inspection) as their needs evolve, future-proofing their investment.
Keshenglong & Shinko: Leading the Way in Flexo Finishing Solutions
When considering a new die-cutting machine for your flexo operations, brands like Keshenglong and Shinko stand out in the market for their commitment to innovation, reliability, and performance. Both brands are renowned for developing robust, high-precision converting equipment that integrates seamlessly with modern flexo presses.
- Keshenglong: Often recognized for its comprehensive range of high-speed, multi-function converting and finishing machines. Their solutions typically emphasize efficiency, stability, and versatility, offering advanced features for precise die-cutting, slitting, and rewinding that meet the demanding requirements of label and packaging producers.
- Shinko: Known for engineering durable and technologically advanced machinery, Shinko often focuses on delivering superior cutting accuracy and robust construction. Their equipment is designed for high-volume production, ensuring consistent quality and reduced operational downtime, making them a trusted choice for serious flexo converters.
Both Keshenglong and Shinko provide solutions that are built to enhance productivity, reduce waste, and deliver a strong return on investment for flexo printers looking to elevate their finishing capabilities.
Recommended for you
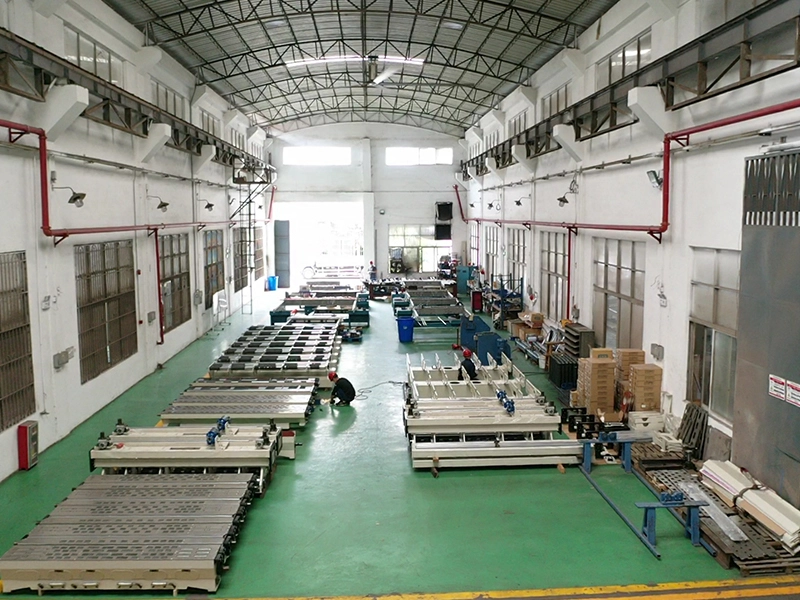
5 Common Flexo Folder Gluer Problems and Expert Solutions
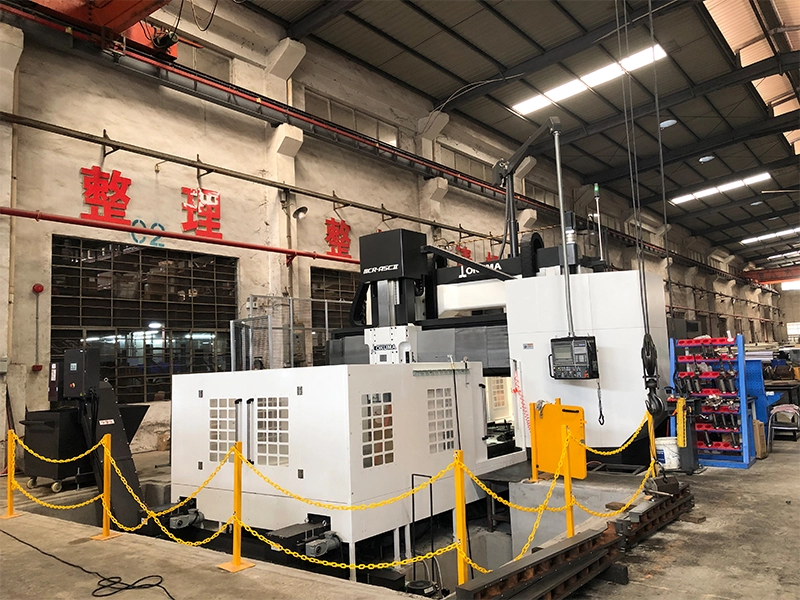
Flexo Folder Gluer Explained: Your Expert Guide
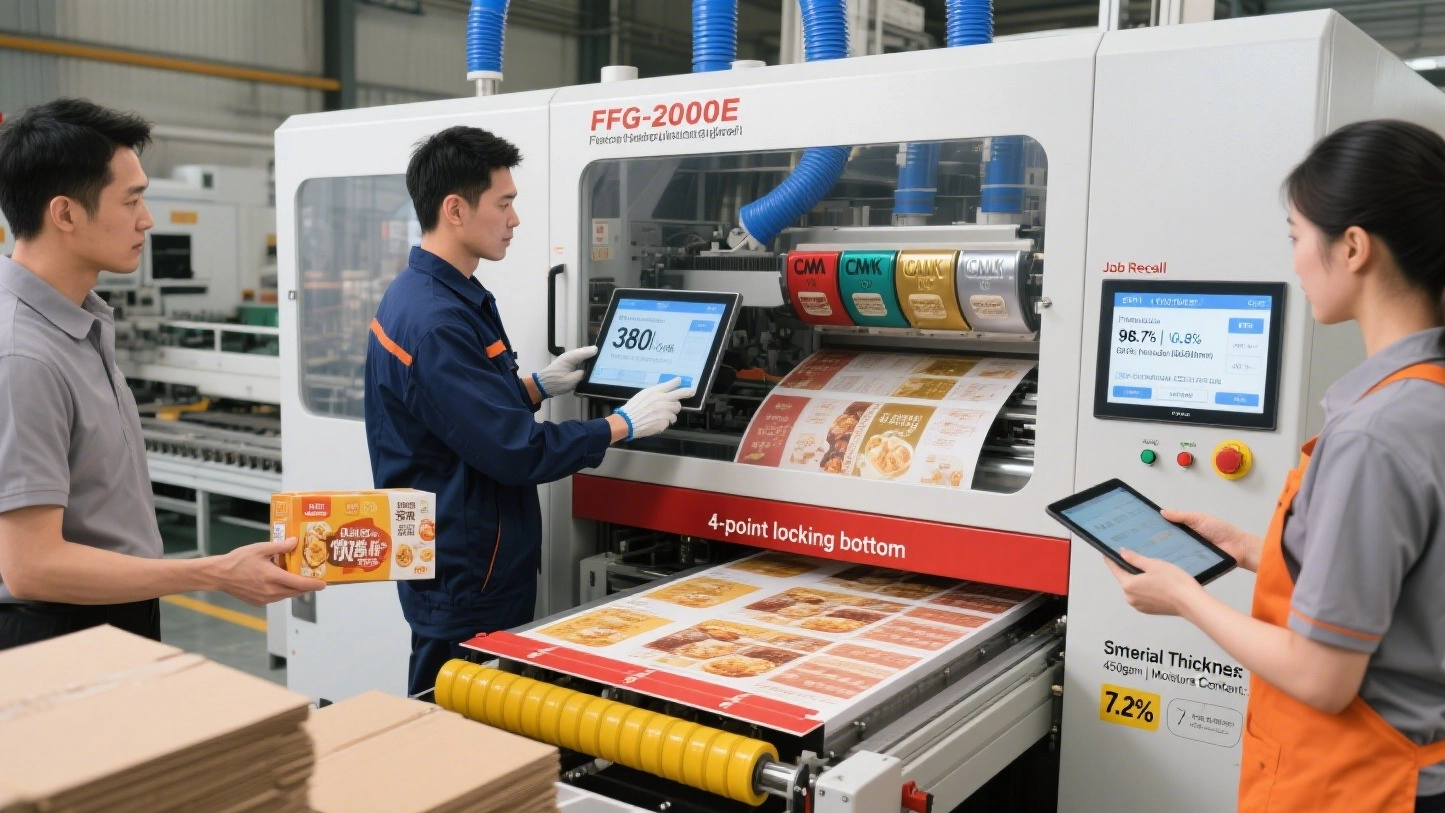
How to Operate a Flexo Folder Gluer Efficiently
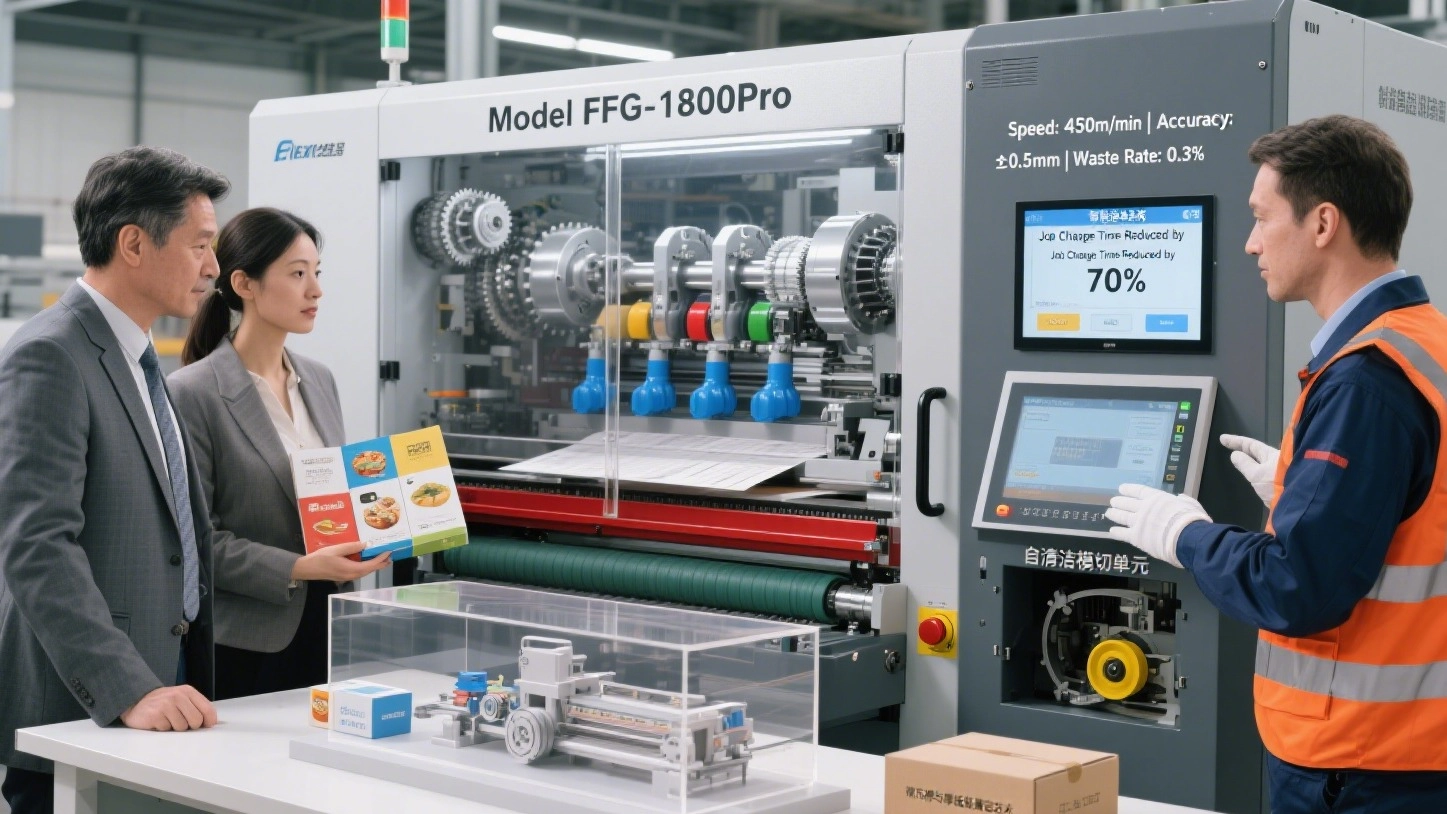
The Ultimate Guide to Flexo Folder Gluer Machines: How to Choose, Operate, and Maintain

Top Corrugated Box Printer Machine Brands
Shipping
Do you provide installation services upon delivery?
Yes, we offer on-site installation and training services to ensure your machine is set up correctly.
How are your machines packaged for safe transportation?
Our machines are securely packaged using high-quality materials to prevent damage during transit.
Product
Can your machines handle custom carton designs?
Yes, our machines can be customized to handle various carton designs and specifications.
What should I do if the machine jams during operation?
In case of a jam, immediately stop the machine, remove any obstructions, and check for any damage before restarting.
How do I troubleshoot common issues with the folding mechanism?
Common issues can often be resolved by checking the alignment of the folding plates and ensuring there is no debris obstructing the mechanism.
Leave a message
Have any questions or queries about our products? Please leave us a message here and our team will get back to you promptly.
* Rest assured that your privacy is important to us, and all information provided will be handled with the utmost confidentiality.
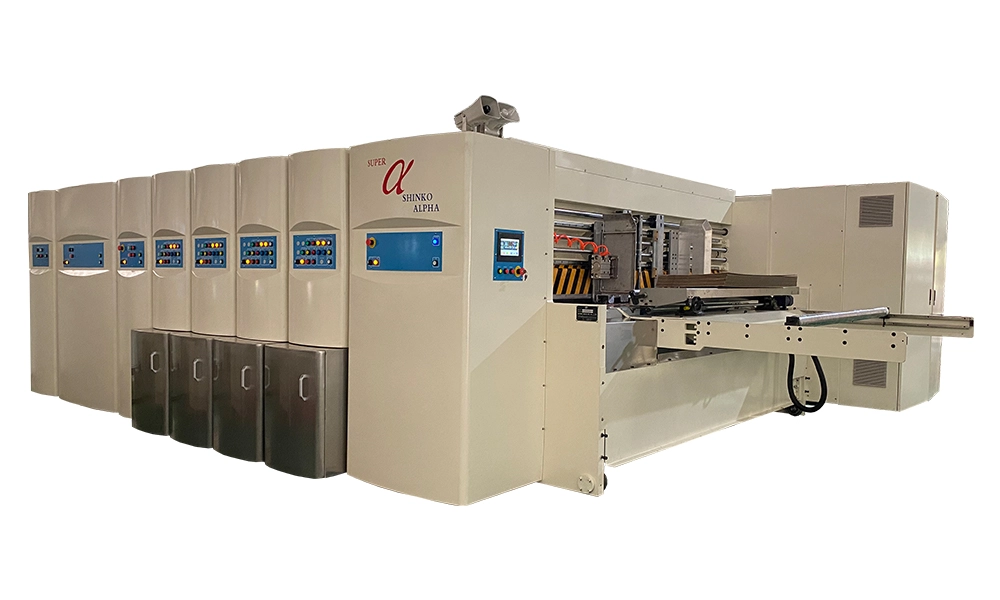
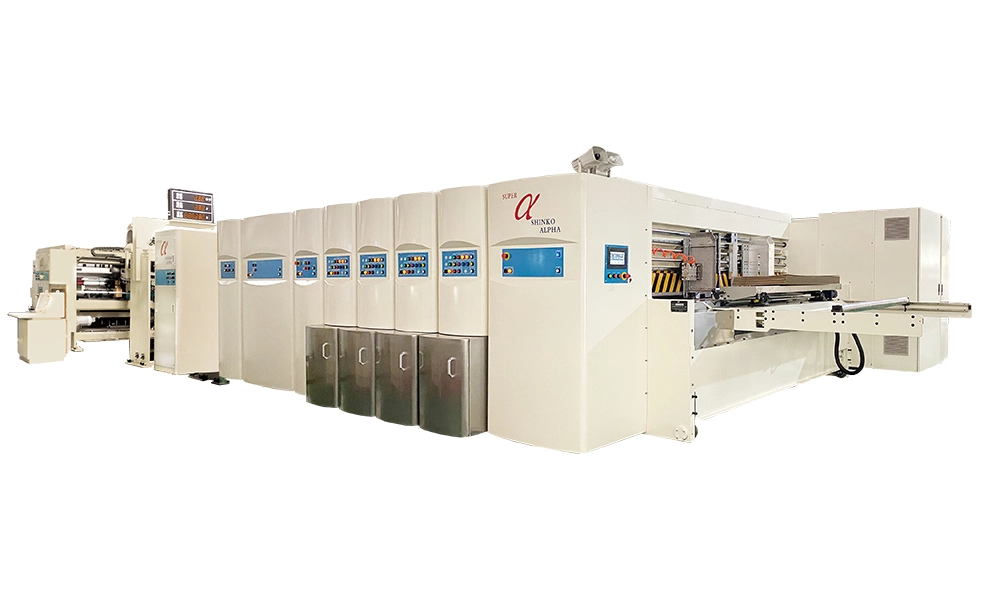
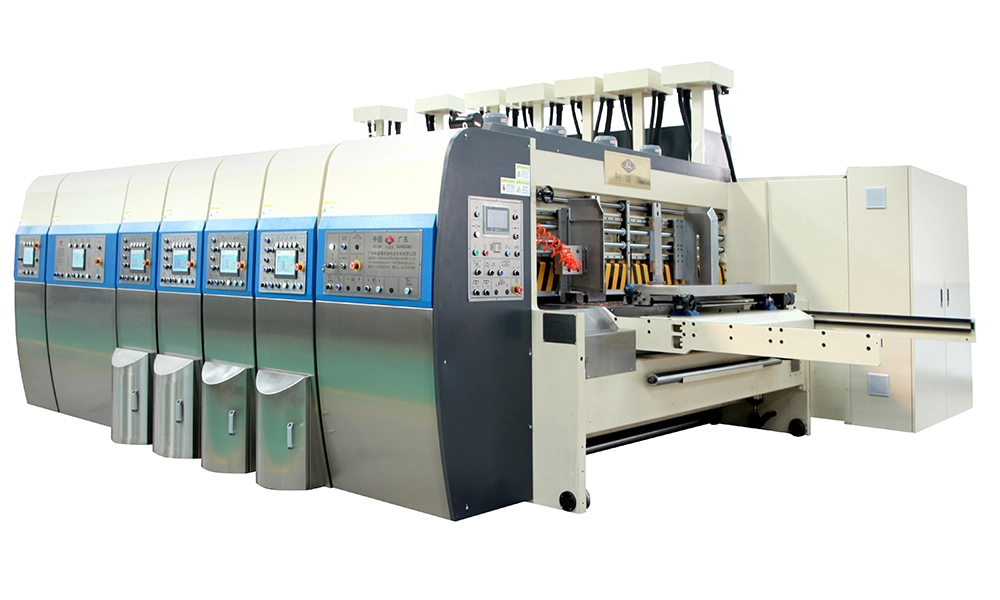
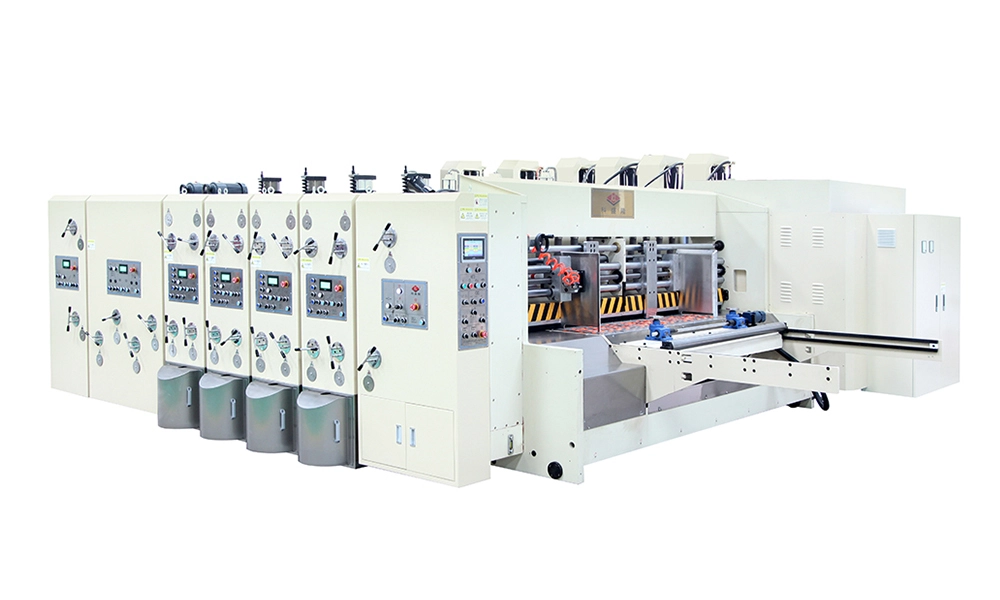
© 2025 Keshenglong & SHINKO All Rights Reserved.
Keshenglong Carton Packing Machine
Keshenglong Carton Packing Machine
Keshenglong Carton Packing Machine
Keshenglong Carton Packing Machine
Keshenglong Carton Packing Machine