How to choose the right die cutting machine for corrugated boxes? | Keshenglong&Shinko Expert Guide
Selecting the optimal die-cutting machine for corrugated boxes is crucial for flexo printers aiming for efficiency and profitability. This guide delves into the core differences between high-speed rotary and precision flatbed technologies, helping you determine which best suits your production needs for corrugated materials. We explore critical specifications like speed, sheet size, and accuracy, alongside the impact of automation on ROI. Discover how advanced features enhance performance and learn key considerations for total cost of ownership, ensuring a wise investment in your packaging operations. Finally, we highlight the strengths of leading brands like Keshenglong and Shinko in the corrugated machinery market.
- Understanding the Core Die-Cutting Technologies: Rotary vs. Flatbed for Corrugated
- What Key Specifications (Speed, Sheet Size, Accuracy) Should I Prioritize?
- How Do Automation and Integration Capabilities Impact Efficiency and ROI?
- What Factors Influence the Total Cost of Ownership (TCO) and Return on Investment (ROI)?
- Beyond Speed, What Advanced Features or Technologies Enhance Die-Cutting Performance and Versatility?
- Keshenglong & Shinko: Leading Brands in Corrugated Die-Cutting Machinery
Understanding the Core Die-Cutting Technologies: Rotary vs. Flatbed for Corrugated
For flexo printers specializing in corrugated packaging, the choice of a die-cutting machine profoundly impacts efficiency, product quality, and profitability. The primary decision often revolves around two fundamental technologies: rotary and flatbed die cutters. Each offers distinct advantages tailored to specific production requirements for corrugated board.
- Rotary Die Cutters: These machines utilize a cylindrical die that rotates against an anvil roll, cutting the corrugated board as it passes through. They are renowned for their high speed, making them ideal for long production runs of simpler designs like Regular Slotted Cartons (RSC) and standard pizza boxes. Typical operating speeds for corrugated rotary die cutters can range from 8,000 to 12,000 sheets per hour, depending on the machine and job complexity. However, they may offer slightly less precision for intricate designs compared to flatbed systems, with tolerances often around +/- 1-2mm.
- Flatbed Die Cutters: In contrast, flatbed machines use a reciprocating platen that presses a flat steel rule die onto the corrugated sheet. This method provides superior precision and the ability to handle more complex designs, intricate cutouts, and perforations, which are common in Point-of-Purchase (POP) displays or custom packaging. While generally slower than rotary systems, modern automatic flatbed die cutters for corrugated can still achieve speeds of 2,000 to 5,000 sheets per hour for larger formats, with precision tolerances often within +/- 0.5mm. They are also highly versatile in handling a wider range of corrugated board thicknesses, from E-flute up to triple-wall boards (e.g., up to 15mm thick), making them suitable for heavy-duty packaging.
Your choice depends on your primary production volume, design complexity, and desired precision. High-volume, simple box production often favors rotary, while diverse, intricate, and high-quality jobs benefit from flatbed technology.
What Key Specifications (Speed, Sheet Size, Accuracy) Should I Prioritize?
Beyond the technology type, several core specifications dictate a machine's suitability for your operations:
- Speed: As mentioned, this directly impacts throughput. Consider your average job size and daily production targets. A machine producing 10,000 sheets/hour on paper might only produce 3,000 sheets/hour on double-wall corrugated due to material handling challenges. Ensure the advertised speed aligns with your actual corrugated material needs.
- Sheet Size Capacity: This is critical. Machines are typically specified by their maximum and minimum sheet dimensions (e.g., 1600mm x 2800mm or 2200mm x 3200mm are common for large corrugated blanks). Ensure the machine can handle your largest typical blank, as well as efficiently process smaller, multi-up jobs.
- Accuracy & Repeatability: Precision in cutting and creasing is vital for packaging integrity and efficient downstream processes like gluing. Flatbed machines generally offer higher accuracy, crucial for perfectly aligning flaps and graphics. Rotary machines have improved significantly, but the inherent nature of the rolling cut can sometimes lead to minor deviations, especially with worn dies.
- Corrugated Board Thickness Range: Verify the machine can handle the full range of flutes and board thicknesses you process, from micro-flutes (E, F) to heavy-duty double-wall (BC, EB) and even triple-wall boards. Some machines are optimized for specific ranges.
How Do Automation and Integration Capabilities Impact Efficiency and ROI?
Modern die-cutting machines are far more than just cutters; they are integrated systems designed to maximize efficiency and reduce labor costs. Key automation features include:
- Automatic Feeder: Essential for continuous operation and high speeds, reducing manual loading.
- Automatic Stripping Unit: Removes waste material (trim and internal cut-outs) from the cut sheets, significantly reducing manual labor and speeding up the process. Automated stripping can reduce manual finishing time by up to 70-80% for many jobs.
- Automatic Stacker: Stacks finished blanks neatly, ready for the next process or shipping, improving material handling and preventing damage.
- Inline Integration: The most advanced setups integrate the die cutter directly with a flexo printer, a folder-gluer, or even digital finishing equipment. This creates a seamless workflow, minimizing material handling, reducing bottlenecks, and drastically cutting lead times. For a corrugated plant, an integrated flexo printer-slotter-die-cutter can boost overall line efficiency by 20-30% compared to separate units.
While automation adds to the initial investment, it leads to a significant Return on Investment (ROI) through reduced labor costs, increased throughput, minimized waste due to human error, and faster turnaround times, directly improving profitability.
What Factors Influence the Total Cost of Ownership (TCO) and Return on Investment (ROI)?
The initial purchase price is only one component of the Total Cost of Ownership (TCO). A comprehensive evaluation should include:
- Purchase Price: A new, high-speed corrugated die cutter can range from $300,000 for a basic model to over $1.5 million for fully automated, large-format systems.
- Tooling Costs: Flexible dies for rotary machines are generally cheaper per die (often < $500), but wear faster and are specific to a job. Steel rule dies for flatbed machines are more expensive initially (from $1,000 to several thousands depending on complexity) but are more durable and offer greater precision. For very long runs, the flexible die's low per-unit cost can be advantageous, but for diverse, shorter runs, the versatility and durability of steel rule dies can offer better value.
- Energy Consumption: Larger, higher-speed machines consume more power. Modern machines often feature energy-saving modes and efficient motor designs.
- Maintenance and Spare Parts: Factor in routine maintenance, consumable parts (e.g., cutting pads for rotary, knives), and the availability and cost of spare parts. A well-maintained machine can have a lifespan of 15-25 years.
- Labor Costs: Automation significantly reduces the number of operators required. The savings in labor often form a major part of the ROI calculation.
- Material Waste Reduction: Precise die-cutting and efficient stripping reduce waste, directly impacting raw material costs. Studies show that optimized die-cutting processes can reduce material waste by 5-10%.
Calculate your expected output, labor savings, and material efficiency gains against the total investment to project your ROI, typically looking for a payback period of 3-5 years.
Beyond Speed, What Advanced Features or Technologies Enhance Die-Cutting Performance and Versatility?
Modern die-cutting machines offer a range of advanced features that go beyond basic cutting:
- Quick Die Changeover Systems: Minimizes downtime between jobs, crucial for plants handling multiple short-to-medium runs. Some systems allow die changes in less than 15 minutes.
- Creasing and Perforation Capabilities: Essential for producing functional and easy-to-assemble boxes. High-quality creasing prevents board cracking, especially on coated or digital print surfaces.
- Registration Systems: Advanced camera-based or sensor-driven registration ensures precise alignment of the die cut with pre-printed corrugated sheets, critical for high-graphic packaging. Accuracy often improves with these systems by up to 50%.
- Digital Die-Cutting (for prototyping/short runs): While not a traditional die-cutting machine, digital cutters (like those using router bits or oscillating knives) offer tool-less cutting directly from CAD files. They are perfect for sampling, prototyping, and extremely short runs, offering unparalleled flexibility without the need for physical dies.
- Human-Machine Interface (HMI) & Job Memory: Intuitive touchscreens for machine control, with the ability to store job parameters for quick recall, reducing setup times and operator errors.
Keshenglong & Shinko: Leading Brands in Corrugated Die-Cutting Machinery
When considering your investment, two names frequently stand out in the corrugated machinery market: Keshenglong and Shinko. Both offer distinct advantages:
- Keshenglong: A prominent Chinese manufacturer, Keshenglong is highly regarded for its comprehensive range of corrugated packaging machinery, including integrated flexo printer slotter die-cutters. They are known for providing robust, high-performance machines that offer excellent value, incorporating advanced automation features for efficient corrugated box production. Their strength lies in delivering complete solutions that are reliable and competitive in the global market, particularly for large-scale production needs.
- Shinko: A distinguished Japanese brand, Shinko is synonymous with precision, durability, and high-speed rotary die-cutting technology for corrugated. Their machines are engineered for exceptional reliability and long service life, often favored by companies prioritizing consistent, high-quality output and minimal downtime. Shinko's reputation is built on meticulous Japanese engineering, ensuring that their rotary die cutters deliver consistent performance and accuracy, making them a High Quality choice for demanding corrugated applications.
Both brands represent significant investments but offer the professional capabilities required by leading flexo printers to meet the growing demands of the corrugated packaging industry.
Recommended for you
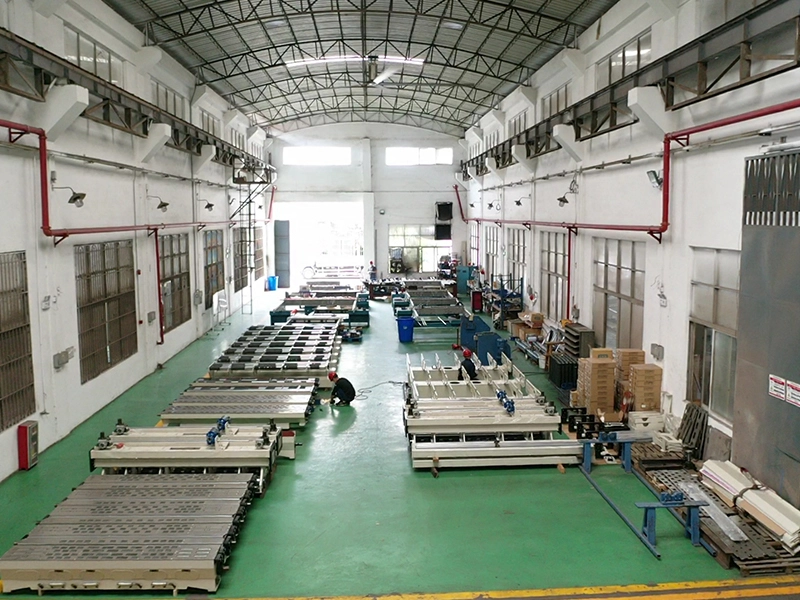
5 Common Flexo Folder Gluer Problems and Expert Solutions
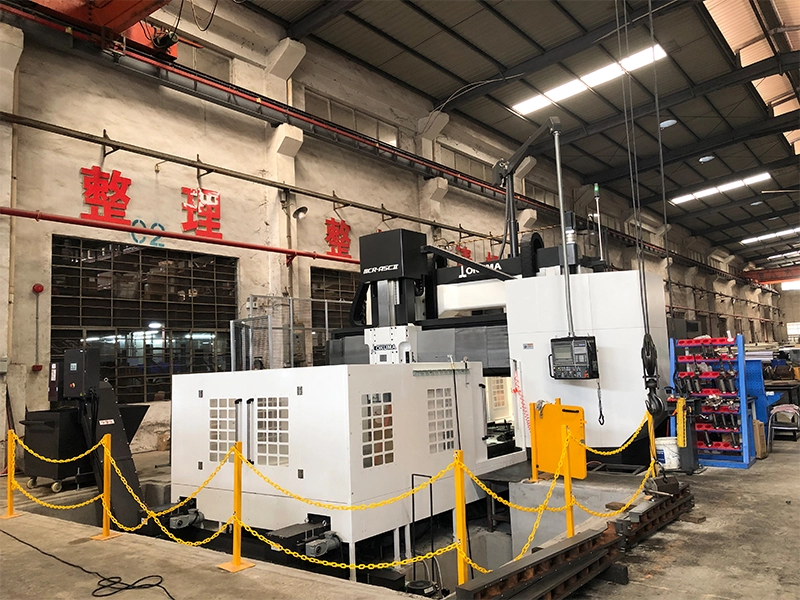
Flexo Folder Gluer Explained: Your Expert Guide
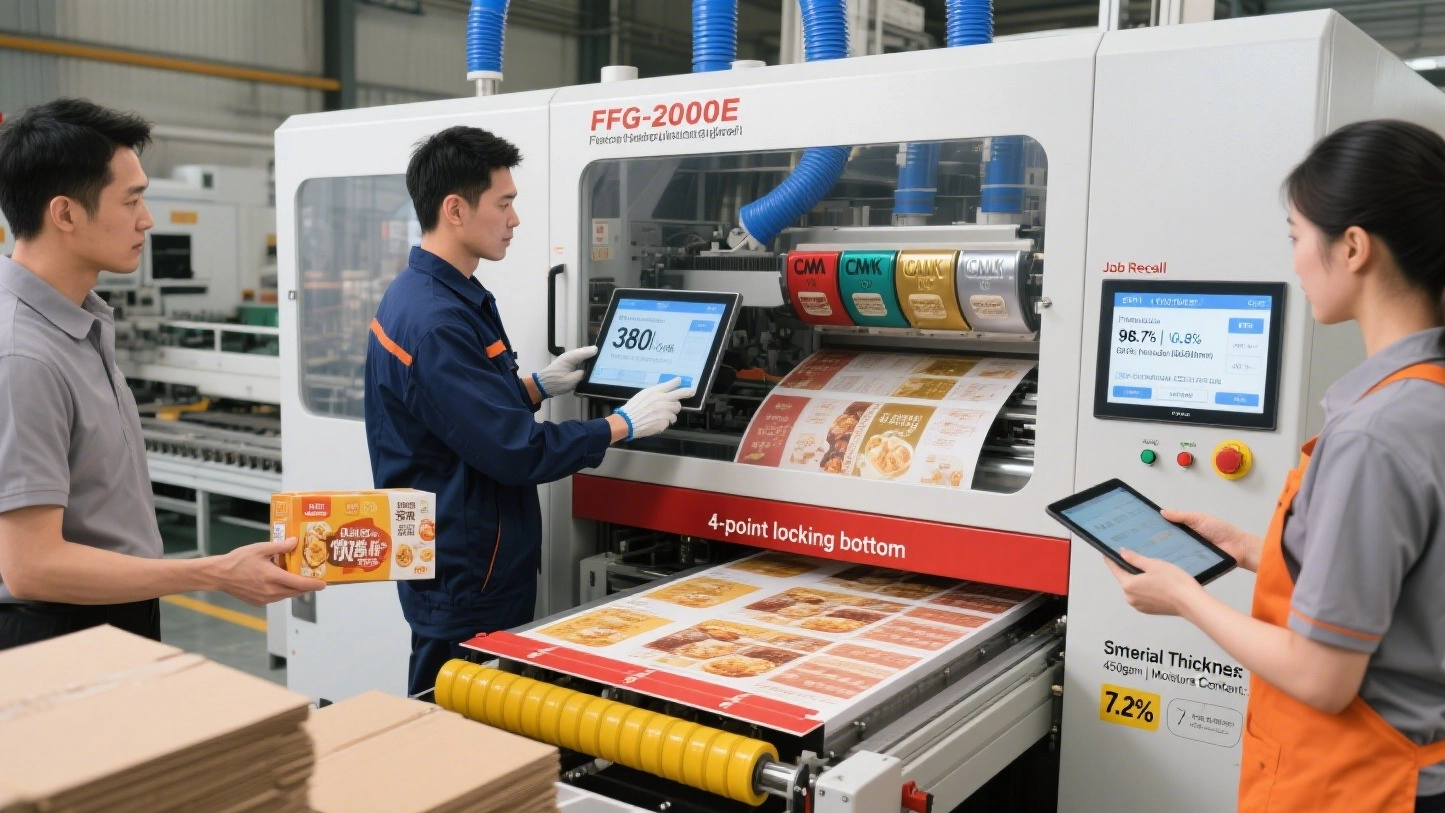
How to Operate a Flexo Folder Gluer Efficiently
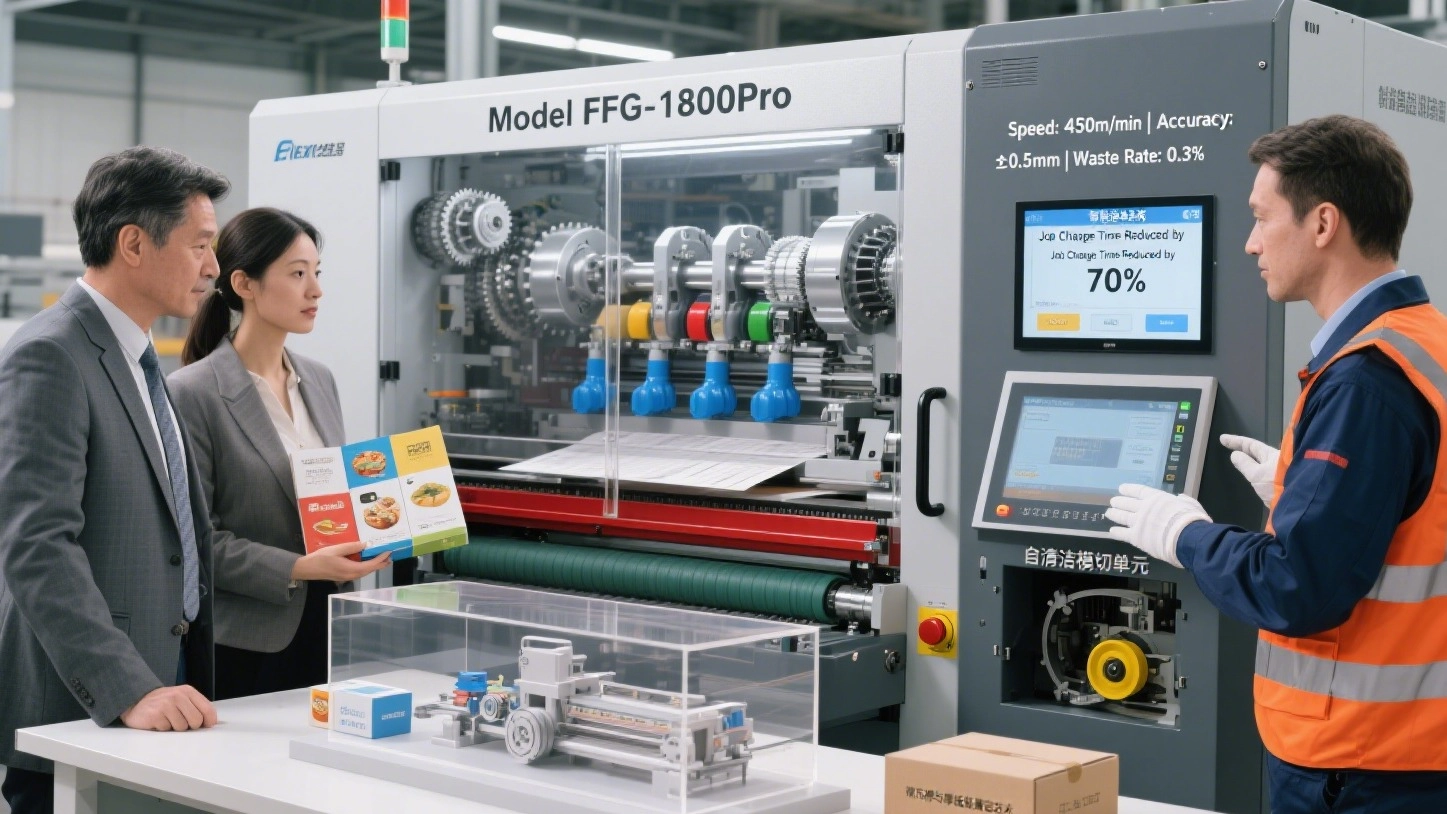
The Ultimate Guide to Flexo Folder Gluer Machines: How to Choose, Operate, and Maintain

Top Corrugated Box Printer Machine Brands
Shipping
Can I track my shipment once it has been dispatched?
Yes, we provide tracking information for all shipments so you can monitor the delivery status.
What are the shipping dimensions and weight of your folding carton machines?
Shipping dimensions and weight vary by model; please refer to the specific product details for accurate information.
What should I do if my machine arrives damaged?
If your machine arrives damaged, please contact our customer service immediately to arrange for repairs or replacement.
What is the estimated delivery time for your machines?
Delivery times vary based on location and order size, but we typically estimate 4-6 weeks for delivery.
Product
What materials are compatible with your folding carton machines?
Our machines are compatible with a wide range of materials including cardboard, corrugated board, and paperboard.
Leave a message
Have any questions or queries about our products? Please leave us a message here and our team will get back to you promptly.
* Rest assured that your privacy is important to us, and all information provided will be handled with the utmost confidentiality.
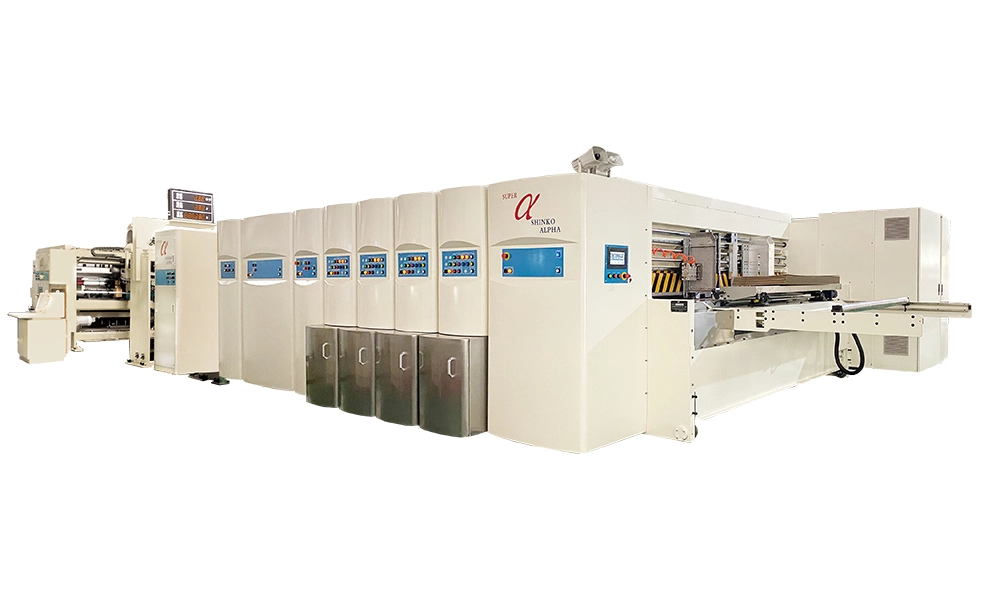
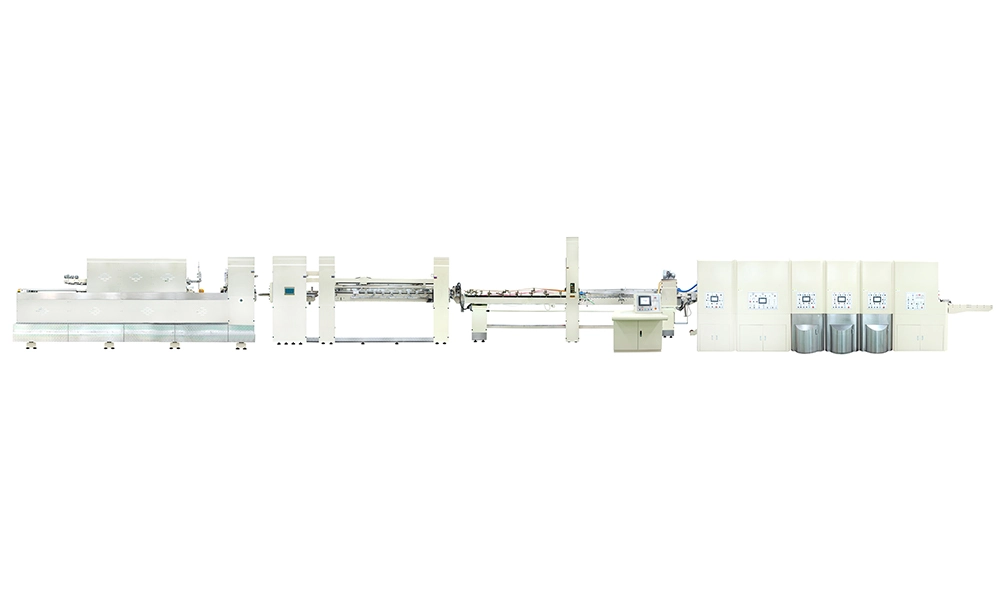
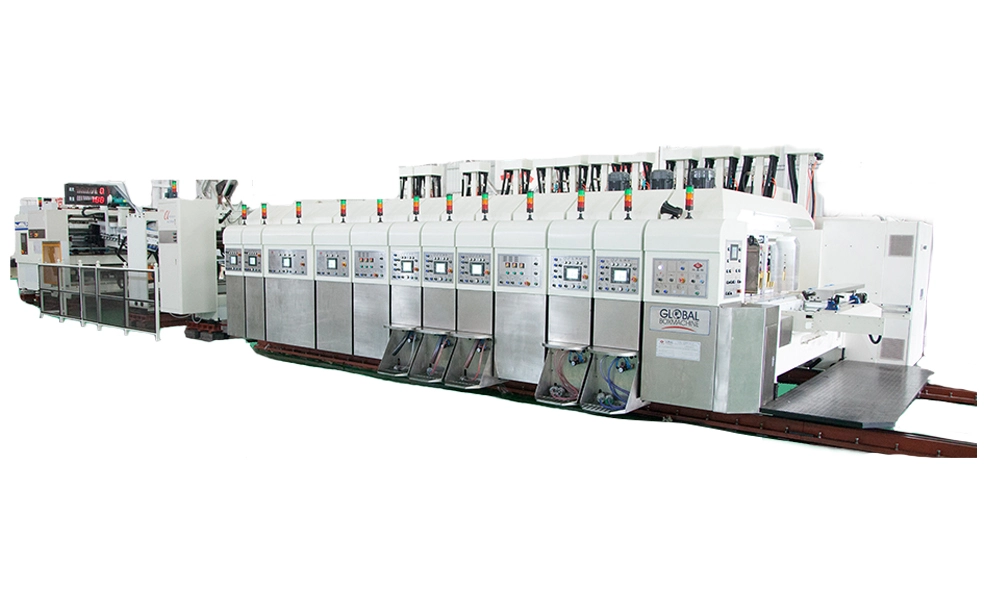
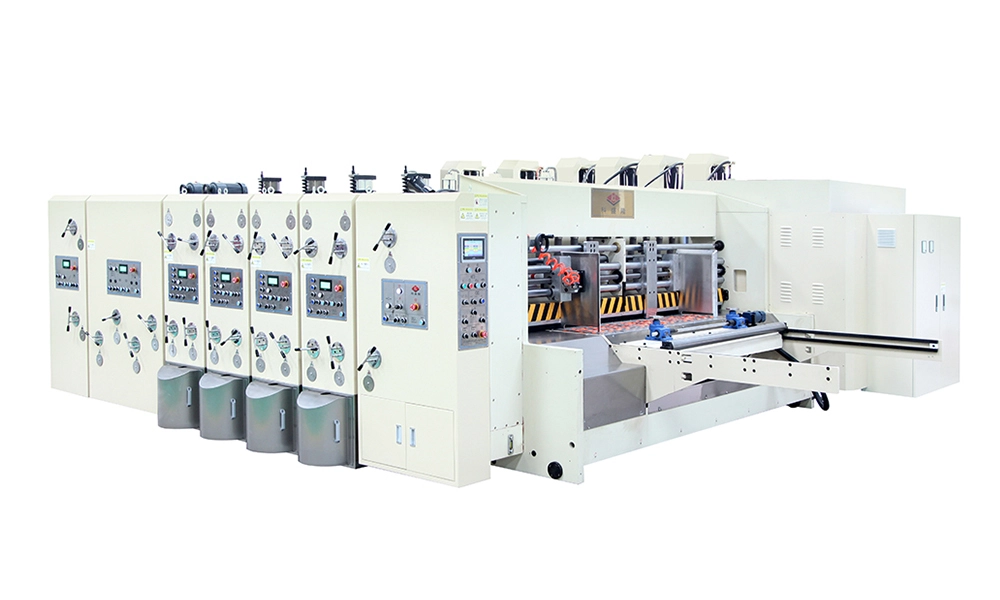
© 2025 Keshenglong & SHINKO All Rights Reserved.
Keshenglong Carton Packing Machine
Keshenglong Carton Packing Machine
Keshenglong Carton Packing Machine
Keshenglong Carton Packing Machine
Keshenglong Carton Packing Machine