what is top bottom flexo printing machine? | Keshenglong&Shinko Expert Guide
Discover the specialized world of top-bottom flexo printing machines, essential for high-efficiency, dual-sided, or complex substrate printing. This guide for procurement professionals explores their unique configurations, significant advantages in speed and registration, and diverse applications in packaging and labels. Learn key purchasing considerations and operational insights to optimize your investment in advanced flexographic technology.
- Navigating the World of Top-Bottom Flexo Printing Machines
- What Distinguishes a Top-Bottom Flexo Printing Machine?
- What Key Advantages Do Top-Bottom Flexo Presses Offer?
- Where Are Top-Bottom Flexo Machines Most Commonly Applied?
- Crucial Considerations When Investing in a Top-Bottom Flexo Machine
- Operational & Maintenance Insights for Top-Bottom Flexo Printers
Navigating the World of Top-Bottom Flexo Printing Machines
What Distinguishes a Top-Bottom Flexo Printing Machine?
A 'top-bottom' flexo printing machine, while not a universal standard classification, typically refers to two main configurations within the flexographic industry, particularly relevant for specialized applications: 1. Duplex Printing Capability: This refers to machines designed to print on both sides (top and bottom) of a substrate in a single pass. This is crucial for applications like flexible packaging, pouches, or certain labels where both sides require print, often achieved through specialized turn-bars or re-register units. 2. Specific Print Unit Arrangement: In some heavy-duty applications, particularly in corrugated post-print, 'top-bottom' might refer to machines where print units are configured to print on the top and bottom surfaces of a sheet as it passes through, facilitating complex box designs. Unlike traditional stack presses or central impression (CI) presses, these machines are engineered for precise registration and efficient material handling for dual-sided or specific substrate flow, optimizing throughput for multi-sided print jobs.What Key Advantages Do Top-Bottom Flexo Presses Offer?
The advantages of top-bottom flexo machines are primarily centered on efficiency, quality, and versatility, which directly translate to lower operational costs and enhanced product quality. Key benefits include:- Increased Throughput & Efficiency: By printing both sides simultaneously or managing complex substrate flows, these machines significantly reduce the need for multiple passes or separate machinery, leading to faster production cycles.
- Superior Registration Accuracy: Especially in duplex systems, advanced tension control and registration systems ensure precise alignment of print on both sides, critical for intricate designs and brand consistency.
- Versatility in Substrates: They are adept at handling a wide range of materials, from thin films for flexible packaging to thicker corrugated boards, expanding product capabilities.
- Reduced Waste & Downtime: Efficient single-pass operation minimizes material waste associated with re-runs and reduces setup times compared to multi-machine processes.
- Optimized Footprint: Consolidating two-sided printing into one machine can save valuable factory floor space.
Where Are Top-Bottom Flexo Machines Most Commonly Applied?
Top-bottom flexo printing machines are indispensable in sectors demanding high-volume, high-quality, and often dual-sided printing. Their primary applications include:- Flexible Packaging: A dominant sector, including pouches for food and beverages, snack bags, and shrink sleeves, where both internal and external surfaces may carry print.
- Labels: Especially wrap-around labels, multi-layer labels, and specialty labels requiring printing on the adhesive side or backing.
- Corrugated Board: For pre-print or post-print applications on corrugated boxes and displays, particularly when complex graphics need to cover multiple faces of the box, or when internal printing for brand messaging is required.
- Folding Cartons: For certain carton designs that benefit from single-pass, dual-sided printing.
- Industrial Films: For various industrial applications where films require specific printed information on both sides.
Crucial Considerations When Investing in a Top-Bottom Flexo Machine
Procuring a top-bottom flexo printing machine requires careful evaluation beyond the initial price tag. Key factors for a judicious investment include:- Production Needs: Assess your current and projected volume, number of colors required (often 8-10 colors or more for complex designs), and desired printing speed (modern machines can exceed 300-400 m/min).
- Substrate Versatility: Ensure the machine can handle the range of materials you intend to print on, considering web tension control, drying systems (UV, EB, hot air), and substrate thickness capabilities.
- Automation & Technology: Look for features like automatic registration control, job changeover automation, inline inspection systems, and advanced tension control. The trend towards industry 4.0 integration for real-time monitoring and predictive maintenance is significant.
- Energy Efficiency & Sustainability: Evaluate power consumption, solvent recovery systems, and compatibility with water-based or UV-LED inks, aligning with increasing environmental regulations and operational cost savings.
- Service & Support: Post-sales service, spare parts availability, and technical support from the manufacturer are paramount for minimizing downtime.
- Total Cost of Ownership (TCO): Factor in not just purchase price, but also installation, training, consumables (inks, plates), maintenance, and energy costs over the machine's lifespan.
Operational & Maintenance Insights for Top-Bottom Flexo Printers
Optimizing the performance and longevity of a top-bottom flexo machine hinges on diligent operational practices and a robust maintenance strategy. Key insights include:- Operator Training: Due to the complexity of dual-sided printing and advanced automation, thorough training for operators on machine operation, troubleshooting, and quality control is vital.
- Preventative Maintenance Schedules: Adhere strictly to manufacturer-recommended maintenance schedules, including regular cleaning of anilox rolls, plate cylinders, and doctor blade systems. Lubrication of moving parts, inspection of bearings, and calibration of sensors are critical to prevent costly breakdowns.
- Ink Management: Proper ink viscosity control, pH balance (for water-based inks), and temperature management are essential for consistent print quality and optimal ink transfer.
- Plate & Anilox Care: Careful handling and cleaning of printing plates and anilox rolls prolong their lifespan and ensure sharp, consistent prints.
- Technological Upgrades: Stay informed about potential software and hardware upgrades offered by the manufacturer to enhance machine efficiency, add new capabilities, or improve energy consumption.
- Data Monitoring & Analytics: Leverage integrated monitoring systems to track machine performance, identify bottlenecks, and facilitate predictive maintenance, reducing unexpected downtimes. Modern flexo presses are increasingly incorporating IoT capabilities for this purpose.
Recommended for you
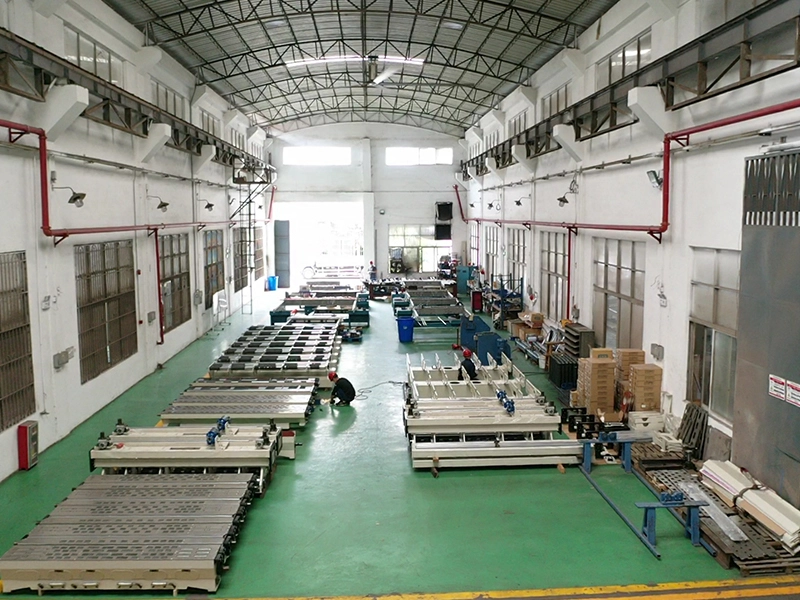
5 Common Flexo Folder Gluer Problems and Expert Solutions
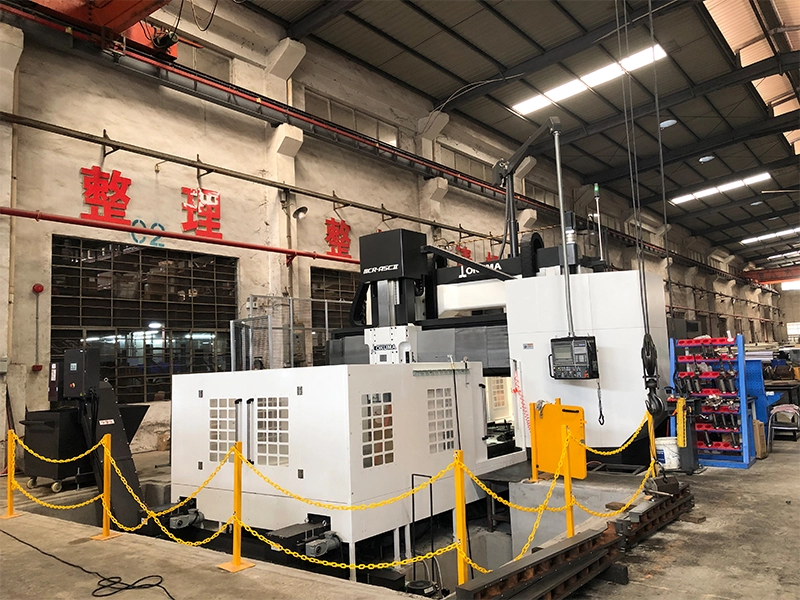
Flexo Folder Gluer Explained: Your Expert Guide
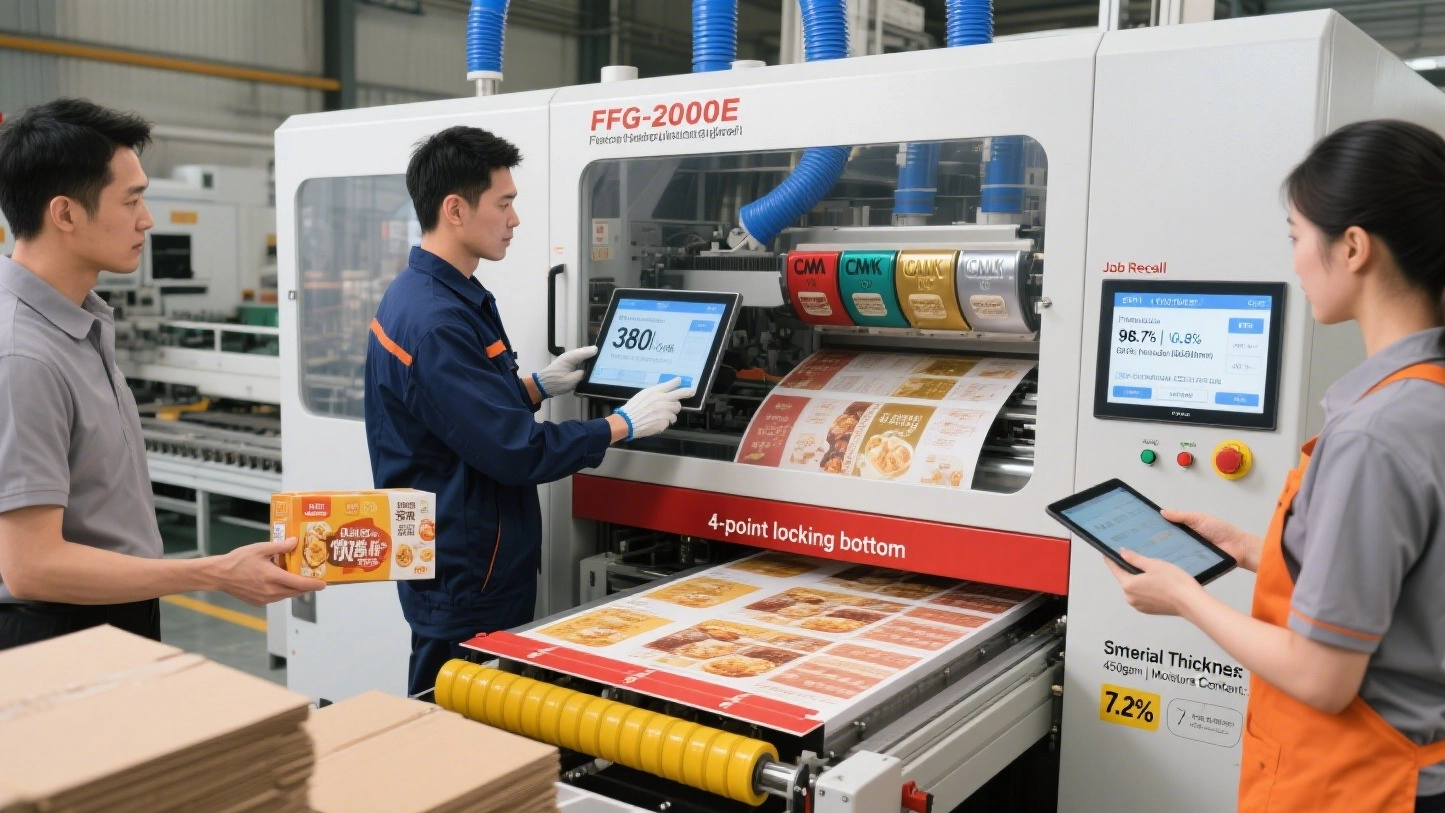
How to Operate a Flexo Folder Gluer Efficiently
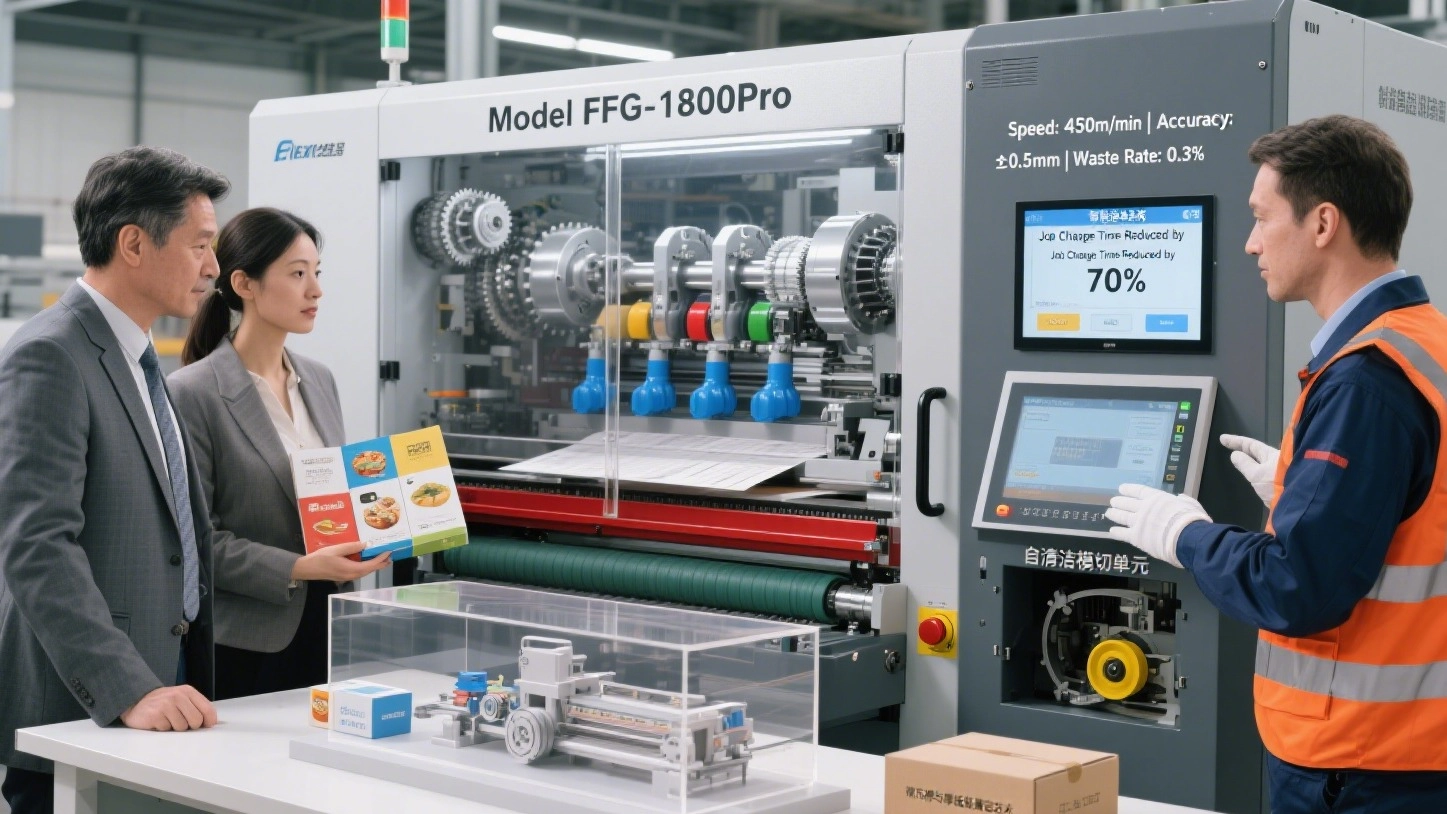
The Ultimate Guide to Flexo Folder Gluer Machines: How to Choose, Operate, and Maintain

Top Corrugated Box Printer Machine Brands
Product
How do I troubleshoot common issues with the folding mechanism?
Common issues can often be resolved by checking the alignment of the folding plates and ensuring there is no debris obstructing the mechanism.
What should I do if the machine jams during operation?
In case of a jam, immediately stop the machine, remove any obstructions, and check for any damage before restarting.
What materials are compatible with your folding carton machines?
Our machines are compatible with a wide range of materials including cardboard, corrugated board, and paperboard.
How do I adjust the machine settings for different carton sizes?
Machine settings can be adjusted using the intuitive control panel, which allows for quick changes to accommodate different carton sizes.
Industry Solutions
Can your machines be integrated with digital printing technology?
Yes, our machines are compatible with digital printing systems for custom, high-quality printing on cartons.
Leave a message
Have any questions or queries about our products? Please leave us a message here and our team will get back to you promptly.
* Rest assured that your privacy is important to us, and all information provided will be handled with the utmost confidentiality.
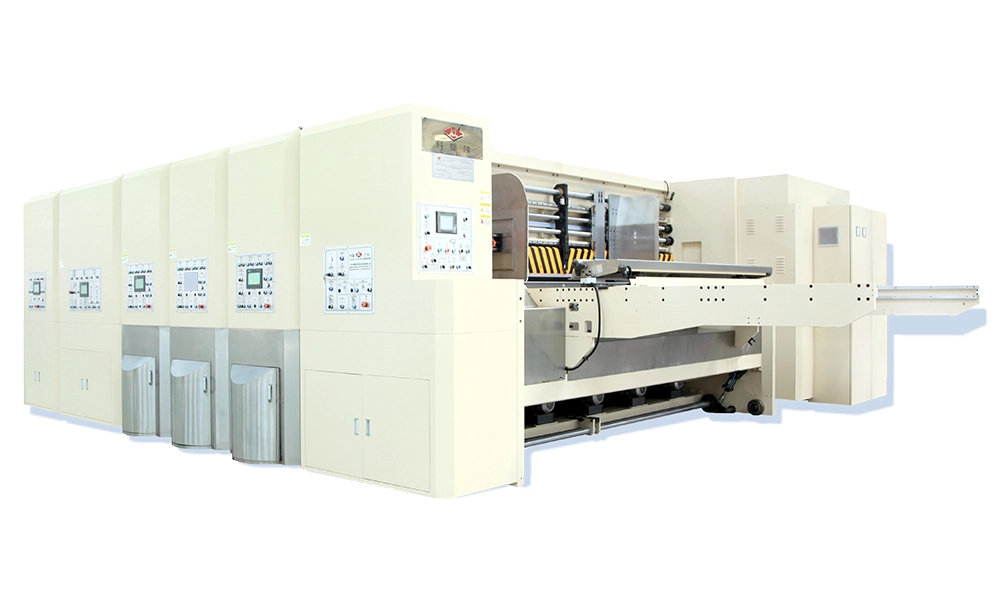
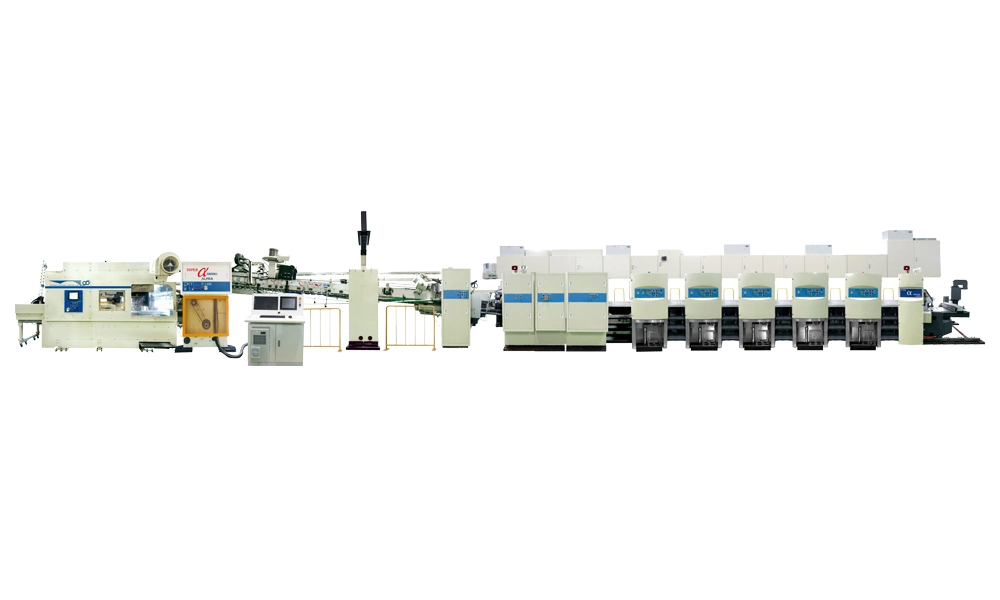
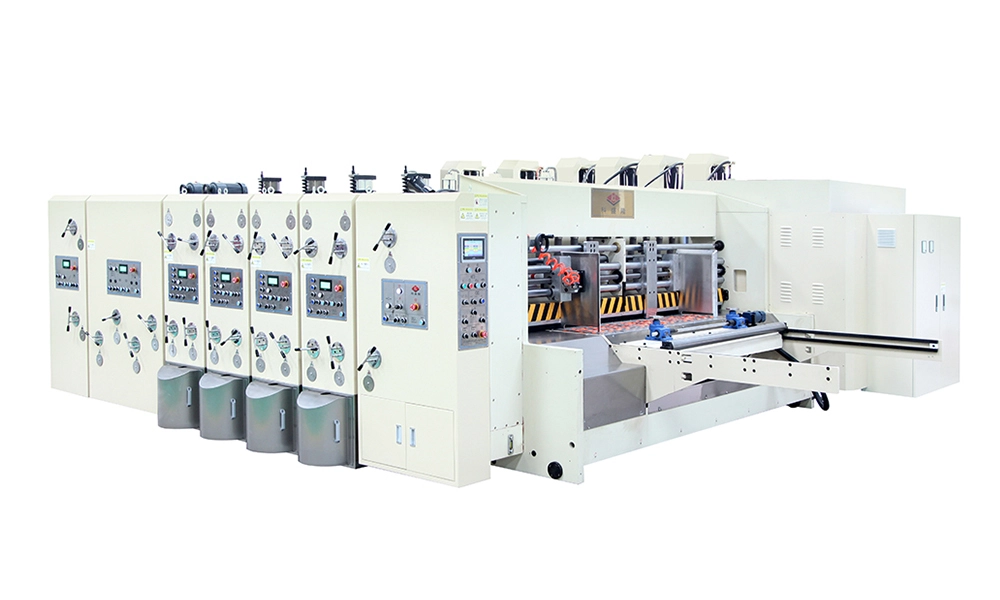
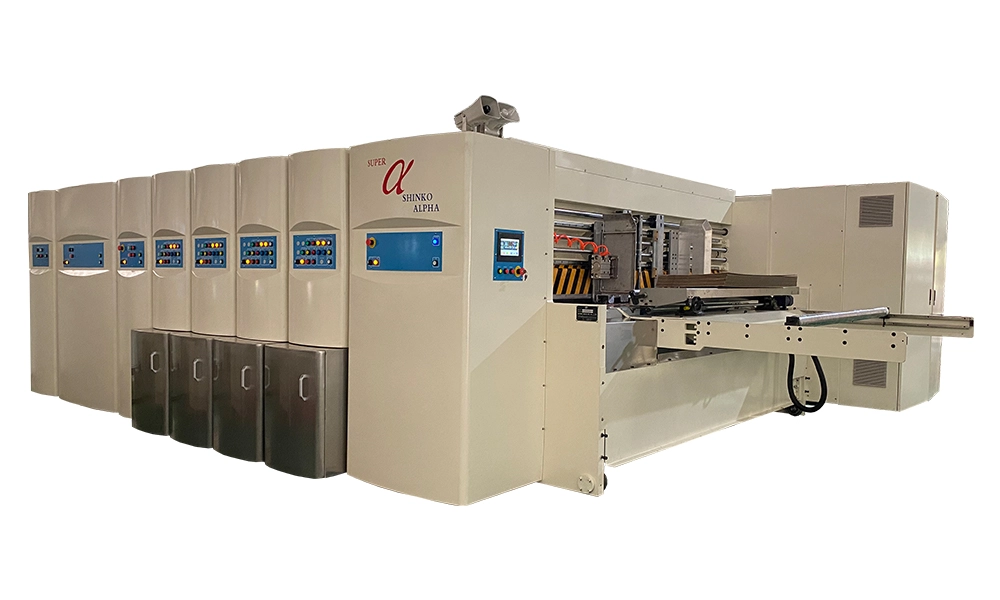
© 2025 Keshenglong & SHINKO All Rights Reserved.
Keshenglong Carton Packing Machine
Keshenglong Carton Packing Machine
Keshenglong Carton Packing Machine
Keshenglong Carton Packing Machine
Keshenglong Carton Packing Machine