What is the maximum production speed in sheets per minute? | Keshenglong&Shinko Expert Guide
Understanding flexo printer production speed, particularly in sheets per minute (SPM) for corrugated, is crucial for procurement. While modern corrugated presses can reach 133-250 SPM (or over 300 SPM for advanced models), and narrow-web machines operate at hundreds of meters per minute, actual speeds depend on factors like substrate, ink drying, complexity, and inline finishing. Higher speed isn't always better; it involves trade-offs in cost, quality, and maintenance. Buyers should consider production volume, job mix, substrate types, and total cost of ownership to select a press that optimizes efficiency and profitability beyond just its maximum theoretical speed.
- Maximize Efficiency: Understanding Flexo Printer Production Speeds
- What is the typical maximum production speed for flexo printers?
- How does the type of flexo press affect production speed?
- What factors limit or influence the actual operational speed of a flexo press?
- Is higher speed always better, and what are the trade-offs?
- What should buyers consider regarding speed when purchasing a new flexo printer?
Maximize Efficiency: Understanding Flexo Printer Production Speeds
In the dynamic world of packaging and label printing, the production speed of a flexographic printer is a critical metric for profitability and operational efficiency. For procurement professionals, understanding 'sheets per minute' (SPM) or 'meters per minute' (MPM) is not just about raw numbers; it's about matching machine capability to business demands. This article delves into the nuances of flexo printer speeds, addressing key questions buyers often have.
What is the typical maximum production speed for flexo printers?
The term 'maximum production speed' is highly variable in flexography, largely depending on the type of press and its intended application. For corrugated board flexo printers, which are often sheet-fed, speeds are commonly measured in sheets per minute (SPM) or sheets per hour (SPH). Modern corrugated presses can typically achieve speeds ranging from 8,000 to 15,000 sheets per hour (SPH), which translates to approximately 133 to 250 sheets per minute (SPM). High-performance, advanced models might even exceed 300 SPM under optimal conditions. For narrow-web and wide-web flexo presses (used for labels, flexible packaging), speeds are measured in linear feet or meters per minute (FPM/MPM), often reaching hundreds or even over a thousand feet/meters per minute. For example, a high-speed narrow web press could operate at 200-300 meters per minute (650-1000 FPM), and some specialized machines even faster.
How does the type of flexo press affect production speed?
The design and function of different flexo presses inherently dictate their maximum achievable speeds:
- Corrugated Flexo Presses: These are designed to print on rigid, thick corrugated cardboard sheets. The handling of large, stiff sheets requires robust feeding and stacking systems, which inherently limit SPM compared to roll-fed processes. Their speeds are typically measured in SPM or SPH, as mentioned above.
- Narrow-Web Flexo Presses: Primarily used for labels, flexible packaging, and tags, these machines process material from a roll (web). The continuous nature of web feeding allows for much higher linear speeds (MPM/FPM) because there's no stop-and-go for sheet feeding.
- Wide-Web Flexo Presses: Used for flexible packaging films, laminates, and large-format printing, these also operate on a roll-to-roll basis. They can achieve high linear speeds similar to narrow-web presses, but also need to handle wider web widths, which can introduce different challenges regarding tension control and drying.
The material's form factor (sheet vs. roll) is a primary differentiator in how speed is quantified and the achievable rates.
What factors limit or influence the actual operational speed of a flexo press?
While a manufacturer may quote a maximum theoretical speed, the actual operational speed in a production environment is influenced by numerous real-world factors:
- Substrate Type: Different materials (paper, film, cardboard) have varying absorption rates, surface tensions, and strength, affecting ink drying and material handling limits.
- Ink Type and Drying: Water-based, solvent-based, or UV-curable inks have different drying characteristics. Efficient drying systems are crucial for high-speed operation, especially for non-absorbent substrates.
- Number of Colors and Print Complexity: More colors require more print units and precise registration, potentially reducing speed. Complex graphics with fine details or heavy ink laydown can also necessitate slower speeds for optimal quality.
- Inline Finishing Processes: Die-cutting, lamination, foiling, varnishing, and other inline converting processes add complexity and can become bottlenecks if not optimized to match the press speed.
- Plate and Anilox Roll Quality: Worn or damaged plates/anilox rolls can lead to print defects, requiring slower speeds or stops for correction.
- Operator Skill and Maintenance: Experienced operators can maintain higher speeds more consistently. Regular and proper machine maintenance is vital to prevent breakdowns and ensure peak performance.
- Automation Level: Highly automated presses with features like automatic wash-up, plate mounting, and job changeovers can maintain higher average speeds by reducing downtime.
Is higher speed always better, and what are the trade-offs?
While impressive, a higher maximum speed isn't always the sole determinant of a press's value. There are significant trade-offs:
- Cost: Faster machines often come with a higher initial purchase price and potentially higher operating costs (e.g., energy consumption, specialized consumables).
- Quality: Pushing a press to its absolute maximum speed can sometimes compromise print quality, leading to issues like misregistration, ink smearing, or ghosting, especially with challenging designs or substrates.
- Spoilage: Higher speeds, if not managed carefully, can lead to increased material waste due to errors, misfeeds, or quality defects that become apparent at faster rates.
- Maintenance and Wear: Running at consistently high speeds can put more strain on mechanical components, potentially leading to increased wear and tear, and more frequent or intensive maintenance requirements.
- Run Length: For very short runs, the time saved by a faster press might be negated by the longer setup and changeover times relative to the actual printing duration.
The ideal speed is one that balances efficiency, quality, and cost-effectiveness for your typical job mix.
What should buyers consider regarding speed when purchasing a new flexo printer?
When procuring a new flexo printer, consider the following points related to speed:
- Your Typical Production Volume and Job Mix: Do you handle mostly long runs or short, frequent jobs? A high-speed press is most beneficial for high-volume, long-run production.
- Substrate Versatility: If you print on a wide range of materials, ensure the press can maintain acceptable speeds across all of them without significant compromises.
- Desired Print Quality: If high-fidelity graphics are paramount, inquire about the press's ability to maintain quality at various speeds.
- Inline Capabilities: Evaluate how integrated finishing processes affect the overall throughput. The slowest part of the process dictates the true production speed.
- Total Cost of Ownership (TCO): Factor in not just the purchase price, but also energy consumption, maintenance costs, and potential spoilage rates at desired operational speeds.
- Future Scalability: Consider if your future production needs might require even higher speeds or different capabilities. Invest in a machine that offers some headroom.
ly, a procurement decision should focus on the 'effective' or 'sustainable operational speed' that consistently delivers desired quality and profitability, rather than just the theoretical maximum.
Recommended for you
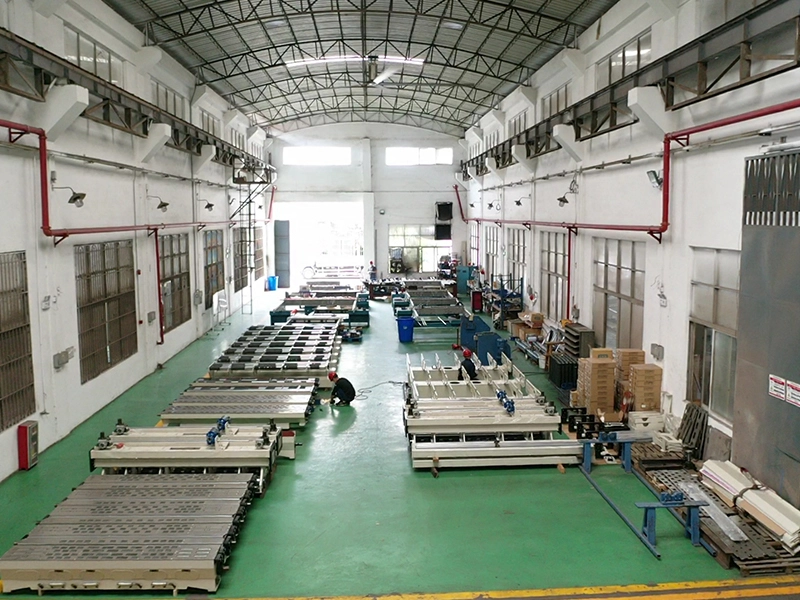
5 Common Flexo Folder Gluer Problems and Expert Solutions
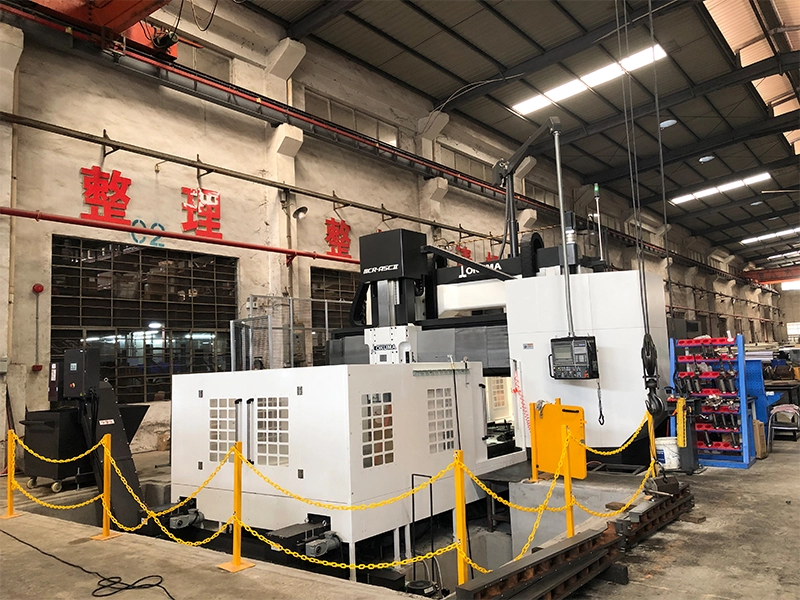
Flexo Folder Gluer Explained: Your Expert Guide
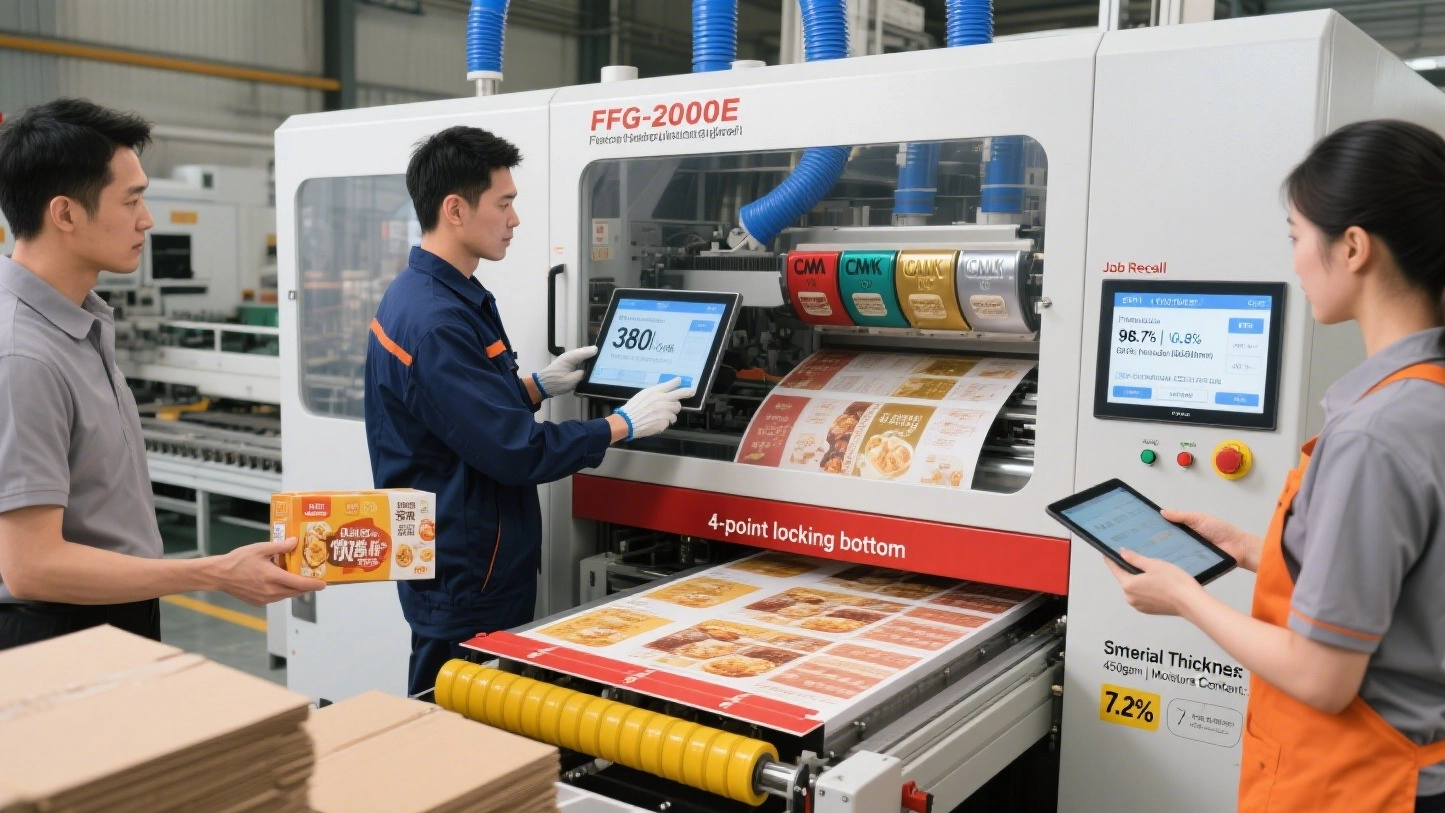
How to Operate a Flexo Folder Gluer Efficiently
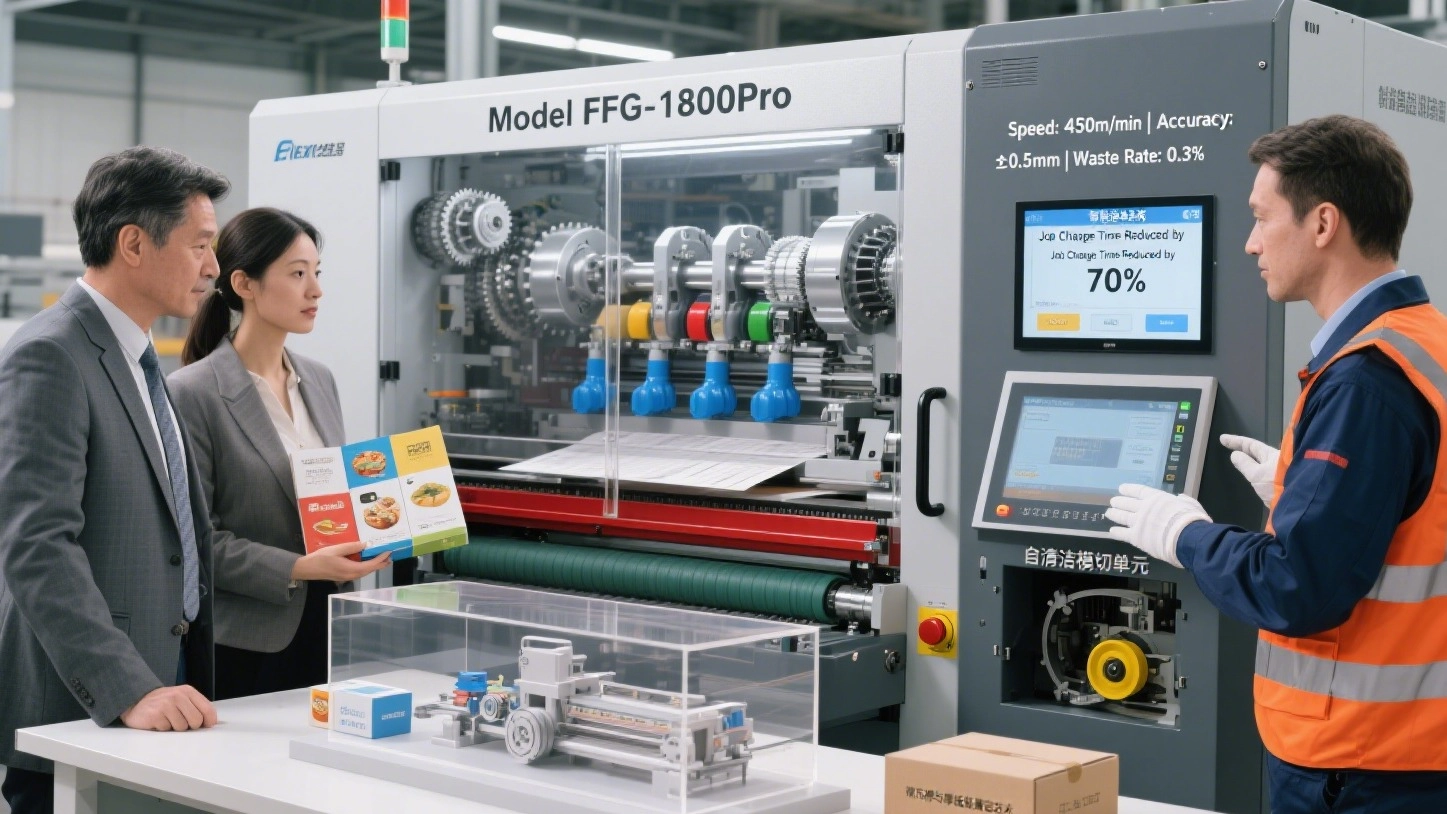
The Ultimate Guide to Flexo Folder Gluer Machines: How to Choose, Operate, and Maintain

Top Corrugated Box Printer Machine Brands
Shipping
Do you offer international shipping for your machines?
Yes, we offer international shipping and can handle all necessary customs documentation.
What should I do if my machine arrives damaged?
If your machine arrives damaged, please contact our customer service immediately to arrange for repairs or replacement.
Product
How do I troubleshoot common issues with the folding mechanism?
Common issues can often be resolved by checking the alignment of the folding plates and ensuring there is no debris obstructing the mechanism.
What is the maximum speed of your folding carton machines?
Our machines can operate at speeds of up to 150 cartons per minute, depending on the model and carton complexity.
What materials are compatible with your folding carton machines?
Our machines are compatible with a wide range of materials including cardboard, corrugated board, and paperboard.
Leave a message
Have any questions or queries about our products? Please leave us a message here and our team will get back to you promptly.
* Rest assured that your privacy is important to us, and all information provided will be handled with the utmost confidentiality.
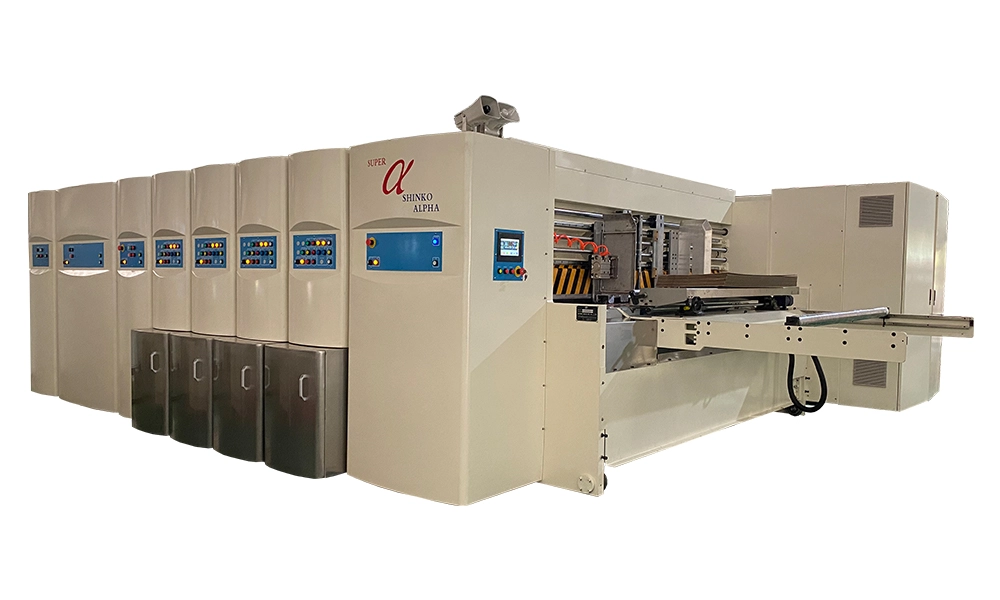
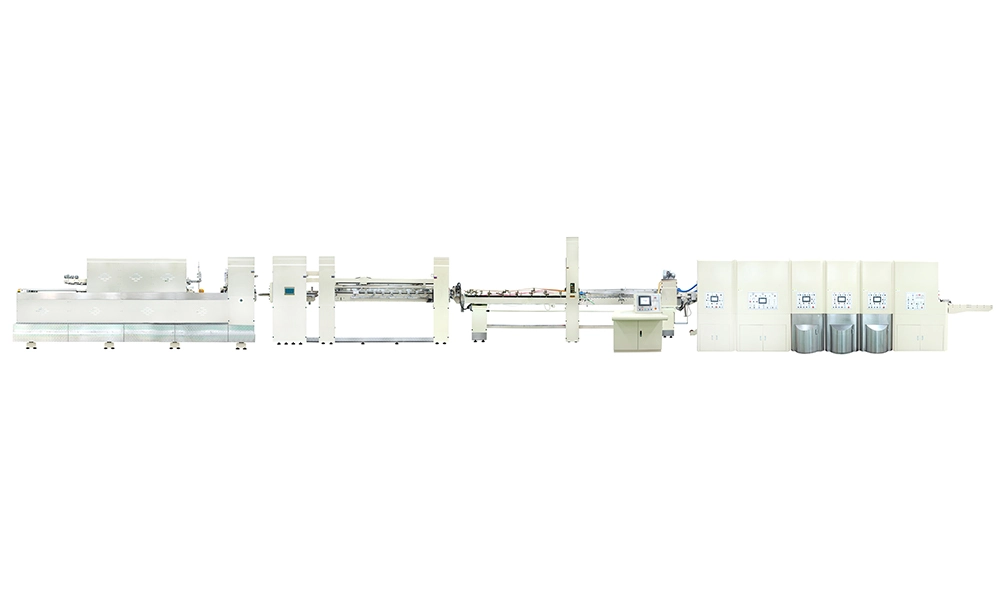
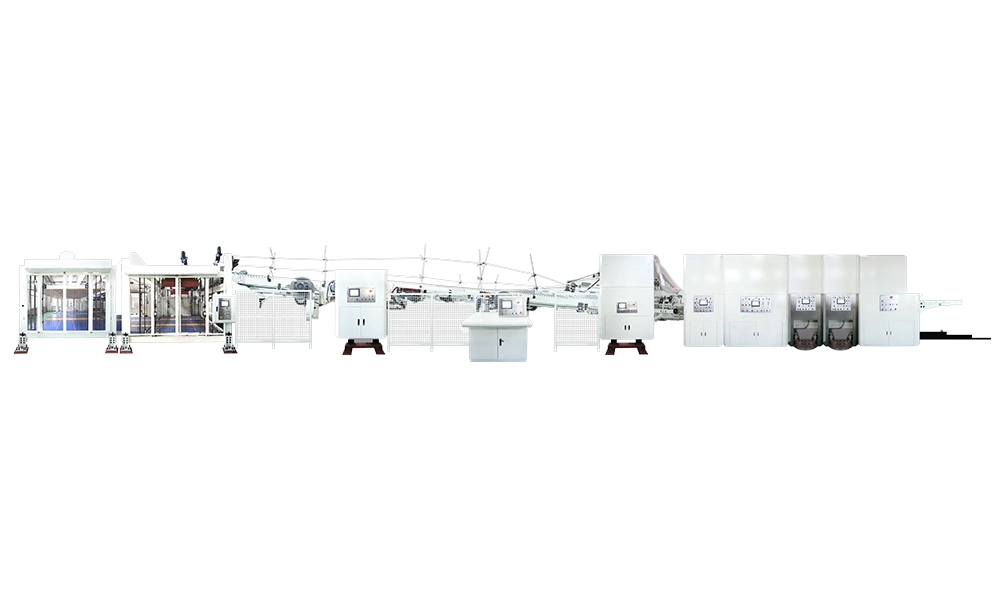
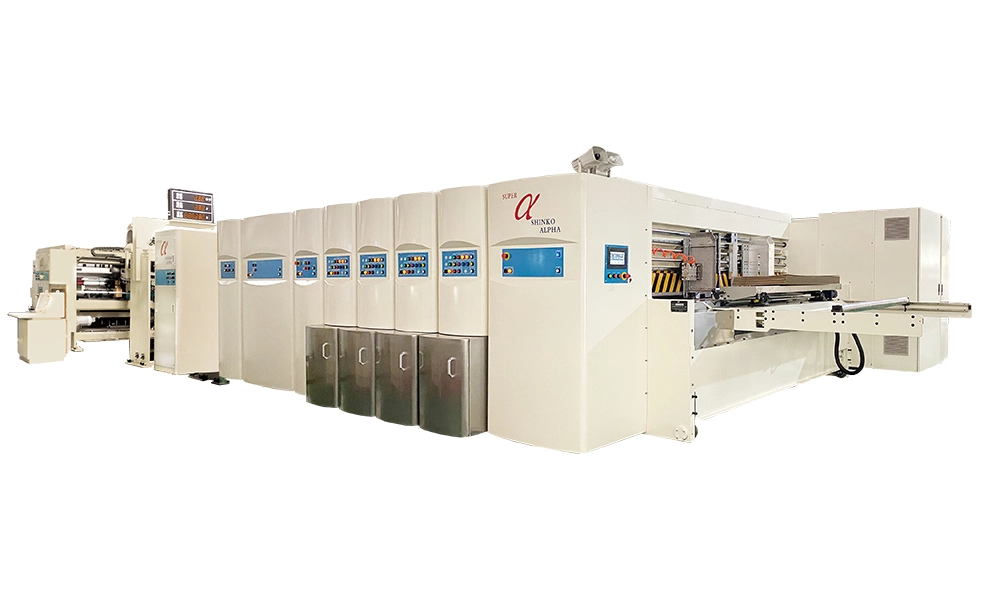
© 2025 Keshenglong & SHINKO All Rights Reserved.
Keshenglong Carton Packing Machine
Keshenglong Carton Packing Machine
Keshenglong Carton Packing Machine
Keshenglong Carton Packing Machine
Keshenglong Carton Packing Machine