What are common problems in die cutting and how to fix them? | Keshenglong&Shinko Expert Guide
Explore common die cutting problems in the flexo printing industry and discover effective solutions to enhance production efficiency and product quality.
Common Die Cutting Issues in Flexo Printing and Their Solutions
Die cutting is a critical process in the flexo printing industry, shaping materials into precise forms. However, several challenges can arise, affecting both efficiency and product quality. Below are five prevalent die cutting problems and their corresponding solutions:
1. Incomplete or Uneven Cutting
Problem Details:
Some areas of the material remain uncut, requiring additional force to separate.
Inconsistent cutting depth can hinder subsequent processes like folding and assembly, reducing overall production efficiency.
Possible Causes:
Insufficient Cutting Pressure: Improperly calibrated pressure systems lead to uneven pressure distribution, resulting in incomplete cuts.
Blade Wear: Over time, blades can become dull or deformed, diminishing their ability to effectively cut through materials.
Uneven Cutting Plate or Cushion: Prolonged pressure exposure can cause indentations or deformations, affecting force distribution during cutting.
Solutions:
Adjust Cutting Pressure: Gradually increase pressure to ensure even distribution across the material.
Replace or Sharpen Blades: Regularly inspect and maintain blades to ensure they remain sharp and effective.
Replace Cutting Plate or Cushion: Ensure these components are in good condition to maintain uniform pressure distribution.
2. Rough or Frayed Cutting Edges
Problem Details:
Cut edges appear rough with visible fraying, impacting the product's aesthetic quality.
Multi-layered materials may not be cleanly cut, leading to fiber pull and compromising the final product's integrity.
Possible Causes:
Dull Cutting Blade: Prolonged use or inadequate maintenance can dull blades, preventing smooth cuts.
Improper Pressure Setting: Incorrect pressure can cause material deformation or tearing.
Inappropriate Material Moisture Content: Excessively dry or moist materials can lead to debris or structural weakening during cutting.
Solutions:
Sharpen or Replace Blades: Regularly maintain blades to ensure they remain sharp.
Optimize Pressure Settings: Adjust pressure to balance between complete cuts and material preservation.
Control Material Moisture: Ensure materials are within optimal moisture ranges to prevent issues during cutting.
3. Excessive or Insufficient Creasing
Problem Details:
Excessive creasing can cause visible cracks or damage to the material's surface.
Insufficient creasing may fail to form clear fold lines, complicating subsequent folding and assembly processes.
Possible Causes:
Improper Gap Between Creasing Rule and Counterplate: An incorrect gap can lead to either excessive compression or insufficient pressure.
Variations in Material Thickness: Inconsistent material thickness can result in uneven creasing depths.
Blade Wear: Worn creasing blades may not form ideal crease lines.
Solutions:
Adjust Gap Settings: Precisely calibrate the gap based on material thickness and properties.
Implement Specification Management: Establish a system to select appropriate creasing tools for different materials.
Regular Equipment Maintenance: Inspect and replace worn creasing blades to maintain optimal performance.
4. Misalignment Issues
Problem Details:
Final products may exhibit noticeable misalignment compared to the original design.
Die-cut edges may not align correctly with printed patterns, affecting visual appeal and processing steps.
Possible Causes:
Inaccurate Material Positioning: Mechanical wear or electronic control deviations can lead to misalignment.
Machine Miscalibration: Installation errors or mechanical shifts can cause misalignment between the die and reference position.
Material Size Variations: Environmental factors can cause material dimensions to fluctuate, leading to positioning errors.
Solutions:
Regular Maintenance: Routinely inspect and calibrate feeder systems to ensure high positioning accuracy.
Standard Calibration Procedures: Periodically check and adjust the die-cutting machine’s reference positions.
Environmental Control: Regulate production environments to prevent material dimension fluctuations.
5. Tool Breakage
Problem Details:
- Tool breakage can disrupt production and increase costs.
Possible Causes:
Incorrect Feed Rate or Cutting Speed: Using inappropriate settings can stress tools, leading to breakage.
Poor Tool Material Selection: Using tools not suited for the material can result in premature failure.
Tool Wear and Tear: Continuous use without proper maintenance can weaken tools.
Solutions:
Match Tool to Material: Ensure tools are appropriate for the material being processed.
Adjust Feed Rates: Optimize feed rates to balance efficiency and tool longevity.
Regular Inspections: Routinely check tools for signs of wear and replace them as needed.
Conclusion
Addressing these common die cutting issues is essential for maintaining high-quality standards in the flexo printing industry. Regular maintenance, proper calibration, and attention to material properties can significantly enhance production efficiency and product quality. Brands like Keshenglong and Shinko are renowned for their commitment to quality and innovation, offering solutions that address these challenges effectively. Their advanced technologies and customer-centric approaches make them valuable partners in achieving optimal die cutting performance.
Recommended for you
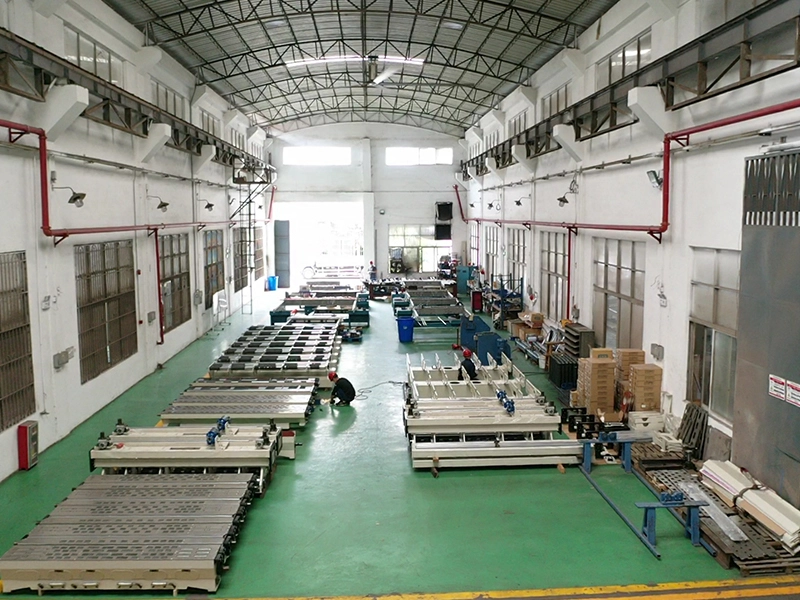
5 Common Flexo Folder Gluer Problems and Expert Solutions
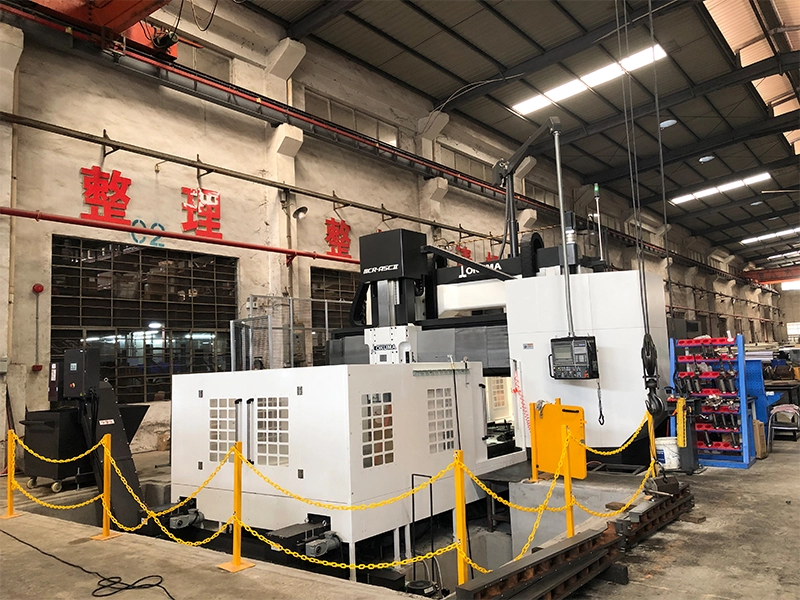
Flexo Folder Gluer Explained: Your Expert Guide
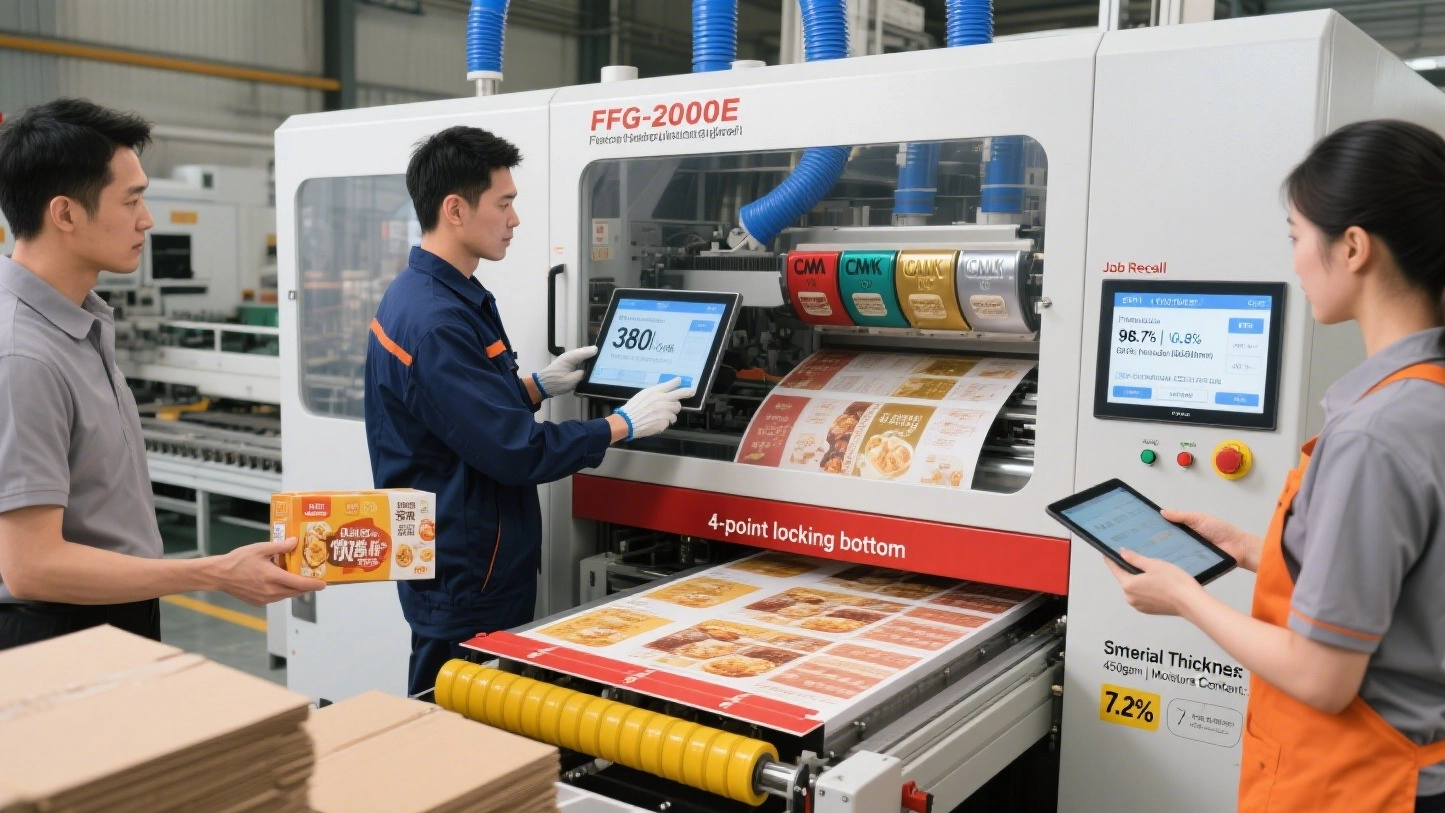
How to Operate a Flexo Folder Gluer Efficiently
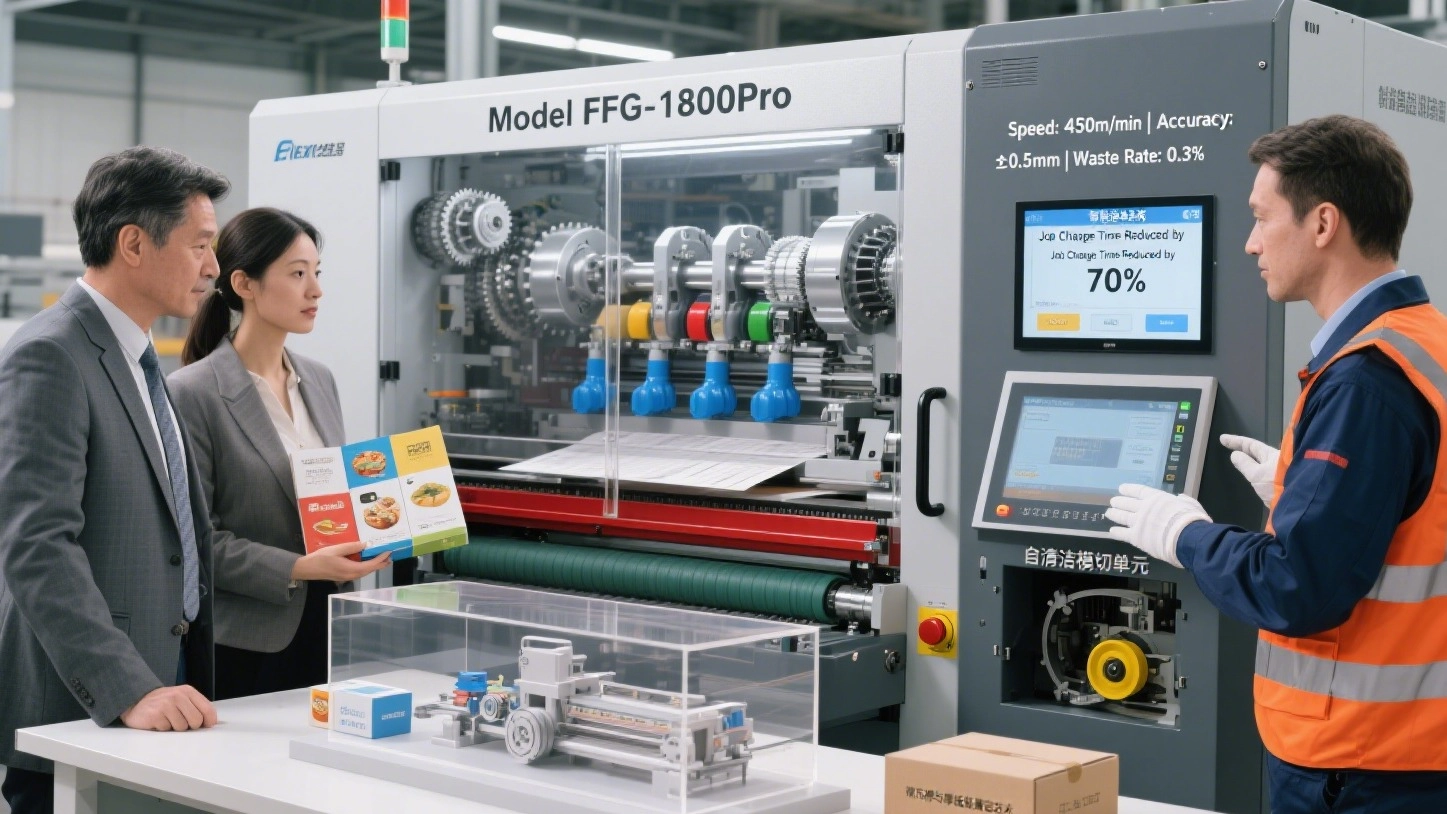
The Ultimate Guide to Flexo Folder Gluer Machines: How to Choose, Operate, and Maintain

Top Corrugated Box Printer Machine Brands
Shipping
What are the shipping dimensions and weight of your folding carton machines?
Shipping dimensions and weight vary by model; please refer to the specific product details for accurate information.
Product
Do your machines support automated quality control checks?
Yes, our machines can be equipped with automated quality control systems to ensure consistent production quality.
Are there safety features integrated into your machines?
Yes, our machines come equipped with multiple safety features including emergency stop buttons and safety guards.
Industry Solutions
How do your machines comply with industry standards and regulations?
Our machines are manufactured to meet or exceed industry standards and regulations, ensuring safe and compliant operation.
What kind of technical support do you offer for industry applications?
We provide comprehensive technical support, including installation, maintenance, and troubleshooting services.
Leave a message
Have any questions or queries about our products? Please leave us a message here and our team will get back to you promptly.
* Rest assured that your privacy is important to us, and all information provided will be handled with the utmost confidentiality.
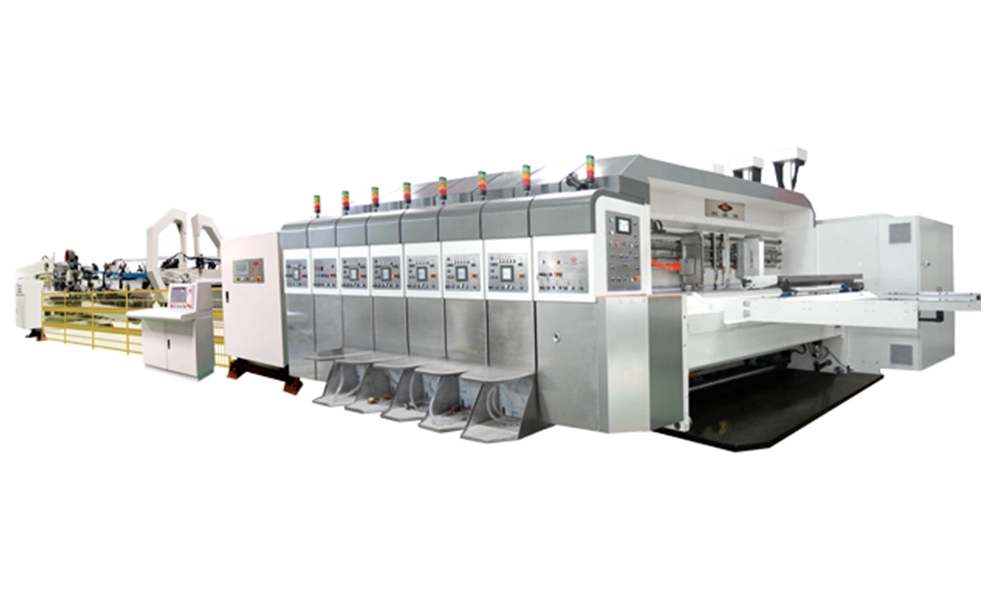
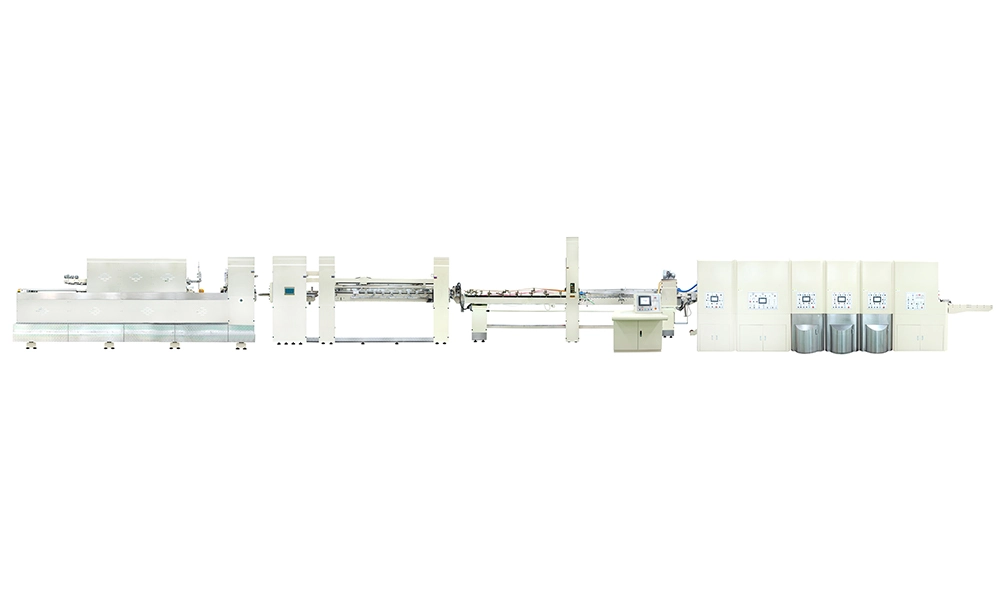
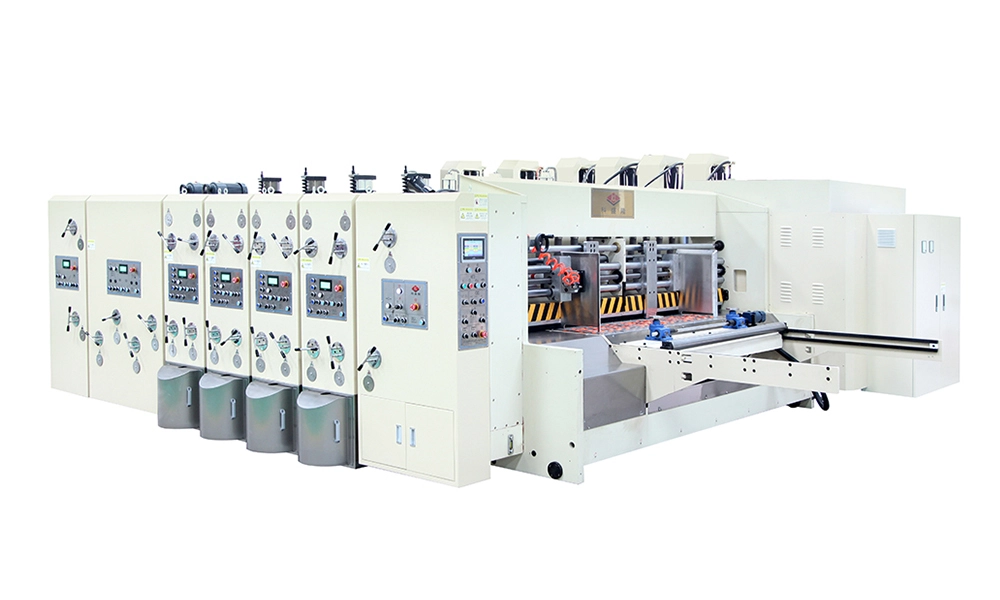
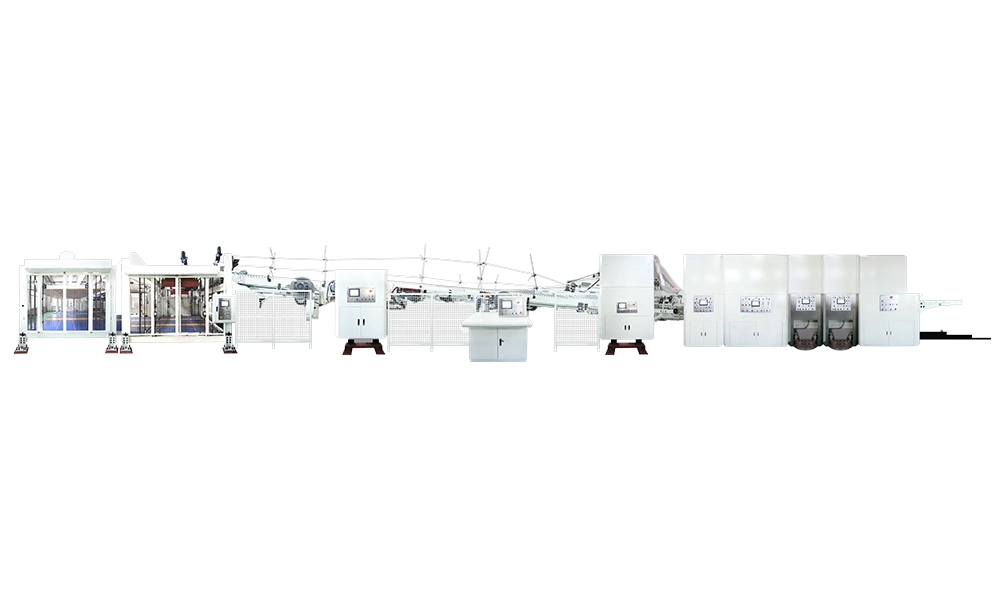
© 2025 Keshenglong & SHINKO All Rights Reserved.
Keshenglong Carton Packing Machine
Keshenglong Carton Packing Machine
Keshenglong Carton Packing Machine
Keshenglong Carton Packing Machine
Keshenglong Carton Packing Machine