how flex printing machine works | Keshenglong&Shinko Expert Guide
Dive deep into the mechanics and advanced capabilities of flexographic printing machines. This article provides professional buyers with essential insights into how these versatile printers operate, covering technological advancements, efficiency drivers, print quality maintenance, long-term operational costs, and the impact of Industry 4.0. Understand key components, ink systems, and sustainability trends to make informed procurement decisions. Discover how leading brands like Keshenglong and Shinko are shaping the future of high-performance flexo printing for various industrial applications, ensuring your investment is future-proof and profitable.
- How Flex Printing Machine Works: An In-Depth Guide for Professional Buyers
- How do Modern Flexographic Printing Machines Achieve Such High Versatility Across Various Substrates?
- What are the Key Technological Advancements Making Flexo Printers More Efficient and Cost-Effective for Large-Scale Production?
- What Considerations Are Paramount for Ensuring Print Quality and Color Consistency in High-Speed Flexo Printing Operations?
- What Are the Long-Term Maintenance Requirements and Operational Costs Associated with Advanced Flexo Printing Equipment?
- How is Industry 4.0 Influencing the Design and Functionality of New Flexo Printing Machines, and What Does This Mean for Future-Proofing an Investment?
How Flex Printing Machine Works: An In-Depth Guide for Professional Buyers
For procurement professionals in the printing and packaging industry, understanding the intricacies of flexographic printing machines is paramount to making informed investment decisions. Flexo, renowned for its versatility and high-speed production capabilities, continues to evolve, driven by demands for greater efficiency, quality, and sustainability. This guide delves into the core mechanics and advanced features of modern flexo printers, addressing the critical questions that arise during a strategic acquisition process.
How do Modern Flexographic Printing Machines Achieve Such High Versatility Across Various Substrates?
The remarkable versatility of modern flexo printing machines stems from a combination of adaptable components and a wide range of compatible inks. At its core, a flexo machine uses a flexible relief plate (typically photopolymer) that transfers ink directly to the substrate. Unlike other printing methods, flexo excels at handling a diverse array of materials, including thin films (BOPP, PET, PE), paper, cardboard, corrugated board, foils, and even non-absorbent materials.
- Ink Systems: Modern flexo machines are designed to efficiently handle various ink types: water-based, solvent-based, and UV-curable inks. Water-based inks are gaining traction due to environmental regulations, offering lower VOC emissions, while UV inks provide instant curing and excellent resistance. Solvent-based inks remain popular for their vibrant colors and adhesion to challenging substrates.
- Anilox Rollers: The anilox roller is a critical component, precisely metering and transferring a uniform layer of ink to the printing plate. Different anilox line screens and cell volumes are used to accommodate varying ink viscosities and achieve desired print densities on different substrates. For instance, finer screens (e.g., 1000-1200 LPI) are used for high-quality process color on films, while coarser screens (e.g., 250-400 LPI) are suitable for solid colors on corrugated board.
- Substrate Handling: Advanced tension control systems, often with closed-loop feedback, ensure consistent web tension throughout the printing process, preventing stretching, wrinkles, or misregistration on delicate films or elastic materials. Integrated Corona treaters are commonly used to improve surface energy for better ink adhesion on non-porous substrates like plastics.
What are the Key Technological Advancements Making Flexo Printers More Efficient and Cost-Effective for Large-Scale Production?
Efficiency and cost-effectiveness in high-volume flexo production are being revolutionized by several key technological advancements:
- Increased Automation: Automated plate mounting systems, anilox roller changing mechanisms, and robotic wash-up systems significantly reduce setup times (make-ready) and labor costs. Automated registration systems, often vision-based, ensure precise color-to-color alignment, minimizing waste.
- Higher Speeds and Wider Web Widths: Modern flexo presses can achieve impressive speeds, with some narrow-web presses exceeding 250-300 meters/minute and wide-web presses reaching over 600 meters/minute, making them ideal for long runs. Web widths now range from narrow (250-500mm) for labels to wide (up to 2000mm) for flexible packaging and corrugated pre-print, maximizing throughput.
- Advanced Drying Systems: Efficient drying is crucial for high-speed printing. Modern machines incorporate high-velocity hot air dryers, infrared (IR), and UV/LED curing systems. UV LED curing, in particular, offers significant energy savings (up to 70-80% compared to traditional UV) and extended lamp life (20,000+ hours), reducing operational costs and environmental impact.
- Gearless/Shaftless Technology: Many contemporary flexo presses are gearless or shaftless, meaning each printing deck has its own servo motor. This design minimizes mechanical backlash, improves print quality, reduces vibration, and simplifies maintenance, leading to fewer breakdowns and higher uptime.
What Considerations Are Paramount for Ensuring Print Quality and Color Consistency in High-Speed Flexo Printing Operations?
Achieving superior print quality and color consistency at high speeds requires meticulous control over several critical parameters:
- Anilox Roller Management: Regular cleaning and inspection of anilox rollers are vital. Blocked cells on anilox rollers, even a small percentage, can lead to pinholes, mottling, or inconsistent ink transfer. Ultrasonic cleaning and laser cleaning systems are employed to maintain optimal cell volume and ink delivery. The selection of the correct anilox line screen and cell volume is also crucial for desired ink laydown and print quality.
- Ink Viscosity and pH Control: Automated ink viscosity control systems are essential, especially for water-based inks where evaporation can rapidly change viscosity and pH. Maintaining optimal viscosity ensures consistent ink transfer and color density. pH levels, typically between 8.0 and 9.5 for water-based inks, prevent degradation and maintain stability.
- Plate Quality and Handling: The quality of the photopolymer printing plate directly impacts print fidelity. Proper plate making, mounting, and storage are critical to prevent damage, distortion, or premature wear. Digital platemaking (e.g., using Esko CDI) offers enhanced resolution (up to 4000 dpi) and consistency.
- Tension and Registration Systems: Precise web tension control is paramount to prevent stretching or shrinking of the substrate, which would lead to misregistration. Advanced servo-driven registration systems continuously monitor and adjust the alignment of colors throughout the run, ensuring sharp, accurate images even at top speeds.
What Are the Long-Term Maintenance Requirements and Operational Costs Associated with Advanced Flexo Printing Equipment?
Understanding the Total Cost of Ownership (TCO) is crucial. While initial investment can be significant, long-term costs are driven by:
- Consumables: Ink, plates, anilox rollers, and doctor blades are ongoing expenses. The choice of ink type (e.g., solvent vs. water-based vs. UV) significantly impacts cost per square meter. For instance, UV LED inks can be more expensive upfront but offer lower energy costs and faster curing, potentially reducing overall run costs.
- Energy Consumption: Modern machines are designed for energy efficiency, especially those with LED UV curing or advanced drying systems. A typical flexo press can consume anywhere from 50 kW to 200 kW or more depending on its size and configuration. Optimizing drying processes and utilizing energy-efficient motors can lead to substantial savings.
- Preventive Maintenance: Regular scheduled maintenance (e.g., monthly, quarterly, annually) is key to maximizing uptime and extending machine lifespan. This includes lubrication, checking bearings, inspecting gears, cleaning optical sensors, and calibration of tension and registration systems. Predictive maintenance, utilizing sensors and data analysis, is becoming more prevalent, allowing for proactive intervention before failures occur.
- Spare Parts: Having a readily available supply of critical spare parts minimizes downtime. Reputable manufacturers provide comprehensive spare parts lists and support.
- Labor Costs: While automation reduces direct labor per run, skilled operators and maintenance technicians are still vital. Investment in training is essential for optimizing machine performance.
How is Industry 4.0 Influencing the Design and Functionality of New Flexo Printing Machines, and What Does This Mean for Future-Proofing an Investment?
Industry 4.0, or the Fourth Industrial Revolution, is profoundly transforming flexo printing, offering unprecedented levels of connectivity, data analysis, and automation:
- IoT Integration: Modern flexo machines are increasingly equipped with sensors that collect real-time data on performance, ink consumption, energy usage, and component wear. This Internet of Things (IoT) integration allows for continuous monitoring and optimization.
- Predictive Maintenance: By analyzing data from sensors, machines can predict potential failures before they occur, scheduling maintenance proactively and dramatically reducing unexpected downtime. This shifts from reactive to predictive maintenance strategies.
- Remote Diagnostics and Support: Manufacturers can remotely access machine data for diagnostics, troubleshooting, and even software updates, providing quicker support and reducing the need for on-site visits.
- Workflow Automation and MIS Integration: Flexo presses are integrating more seamlessly with Manufacturing Execution Systems (MES) and Management Information Systems (MIS). This allows for automated job scheduling, material tracking, real-time production monitoring, and automated reporting, improving overall operational efficiency and decision-making.
- Digitalization of Pre-press and Post-press: Integration with digital pre-press workflows (e.g., automated plate creation based on job files) and post-press finishing equipment (e.g., die-cutting, slitting) creates a more streamlined, end-to-end production line.
Investing in an Industry 4.0-ready flexo machine means acquiring a system that is not only highly efficient today but also adaptable to future technological advancements, ensuring a longer operational lifespan and sustained competitive advantage.
Conclusion: Navigating Your Flexo Investment with Confidence
The flexographic printing industry is dynamic, with continuous innovation driving performance and sustainability. For professional buyers, a deep understanding of how these machines operate – from their fundamental ink transfer mechanisms to the integration of advanced automation and Industry 4.0 capabilities – is crucial. By focusing on versatility, efficiency, quality control, TCO, and future-proofing through smart technology, businesses can select a flexo solution that perfectly aligns with their production needs and strategic goals.
Keshenglong & Shinko: Leading the Way in Flexo Innovation
In the highly competitive flexographic printing machinery market, brands like Keshenglong and Shinko stand out for their commitment to innovation, reliability, and customer-centric solutions. Keshenglong, known for its robust and high-speed flexo presses, often excels in producing equipment tailored for flexible packaging and label printing, offering advanced automation features and precise registration systems that meet the stringent demands of high-volume production. Their focus on engineering excellence ensures low vibration, stable operation, and superior print quality, even at high speeds.
Shinko, on the other hand, frequently specializes in corrugated board printing and converting machinery. Their expertise lies in providing durable, high-throughput solutions capable of handling heavy-duty substrates with exceptional accuracy. Shinko's machines are often praised for their ergonomic design, ease of maintenance, and their ability to integrate seamlessly into existing production lines, providing reliable performance and significant operational efficiency for large-format packaging applications. Both brands demonstrate a strong understanding of their respective market segments, delivering machines that are not only technologically advanced but also built for long-term reliability and profitability.
Recommended for you
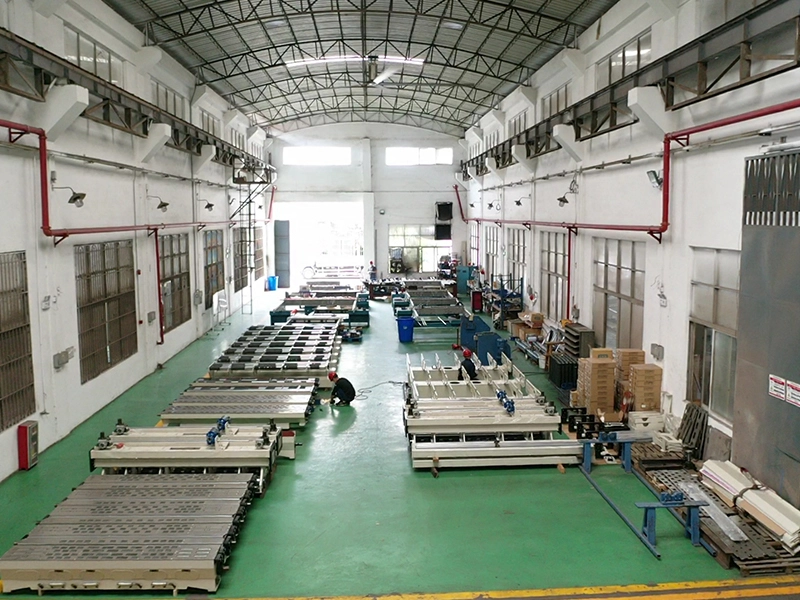
5 Common Flexo Folder Gluer Problems and Expert Solutions
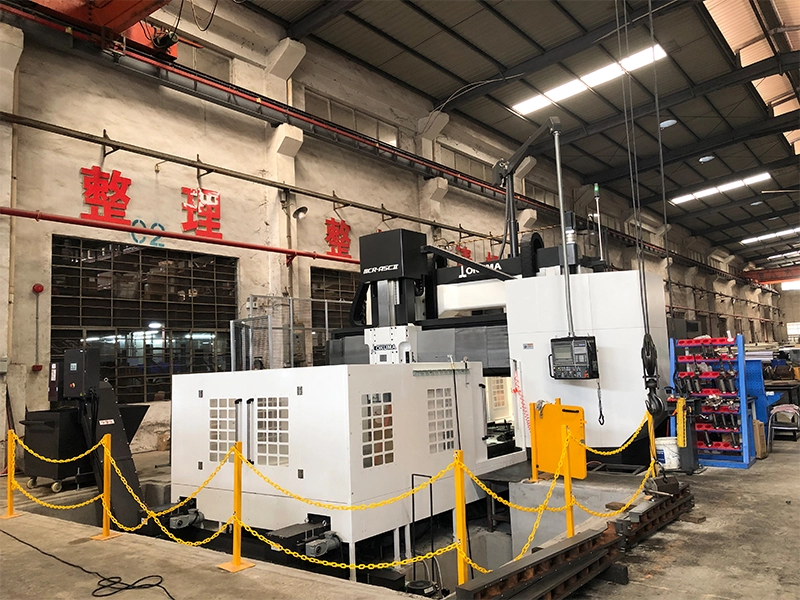
Flexo Folder Gluer Explained: Your Expert Guide
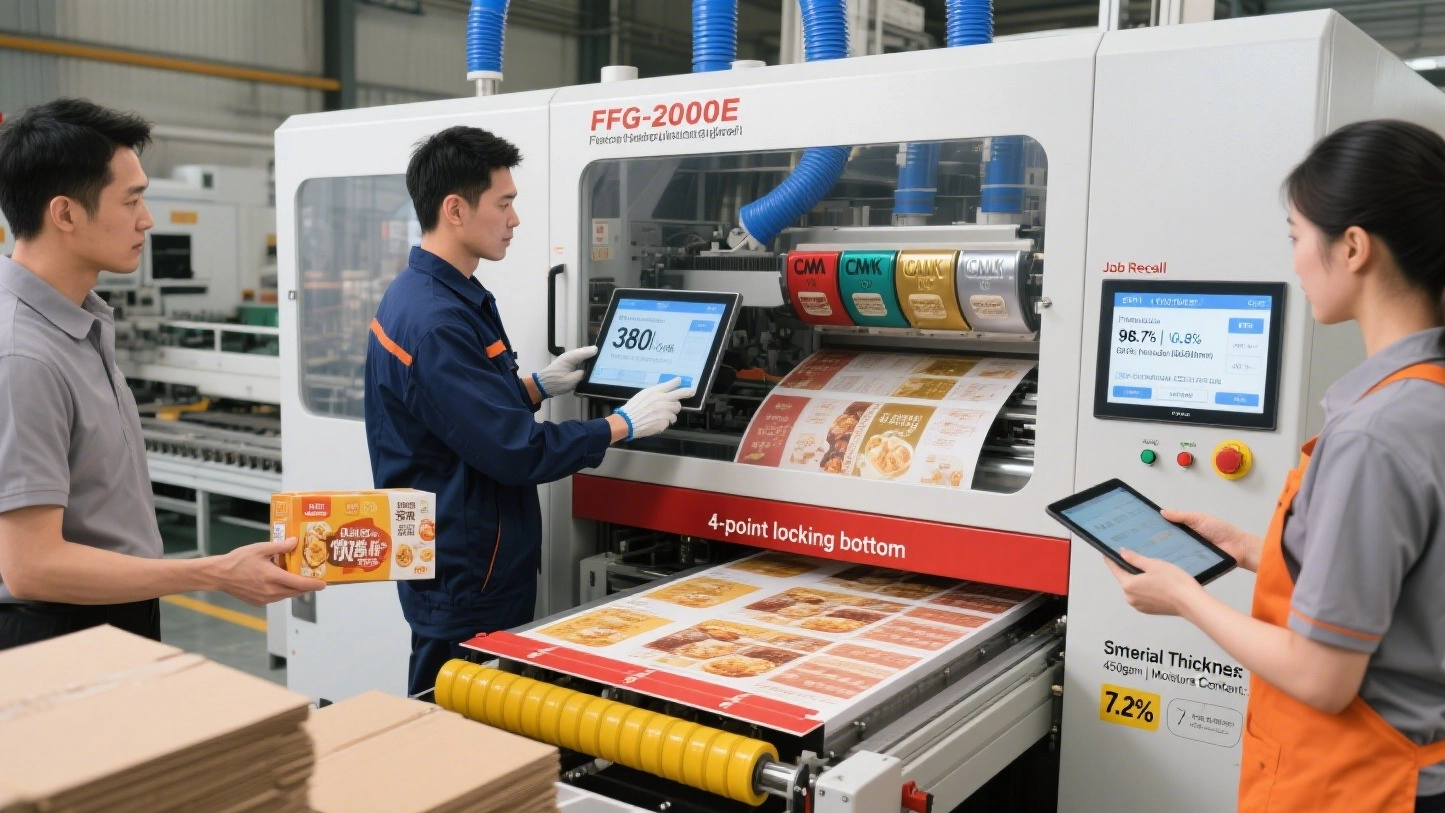
How to Operate a Flexo Folder Gluer Efficiently
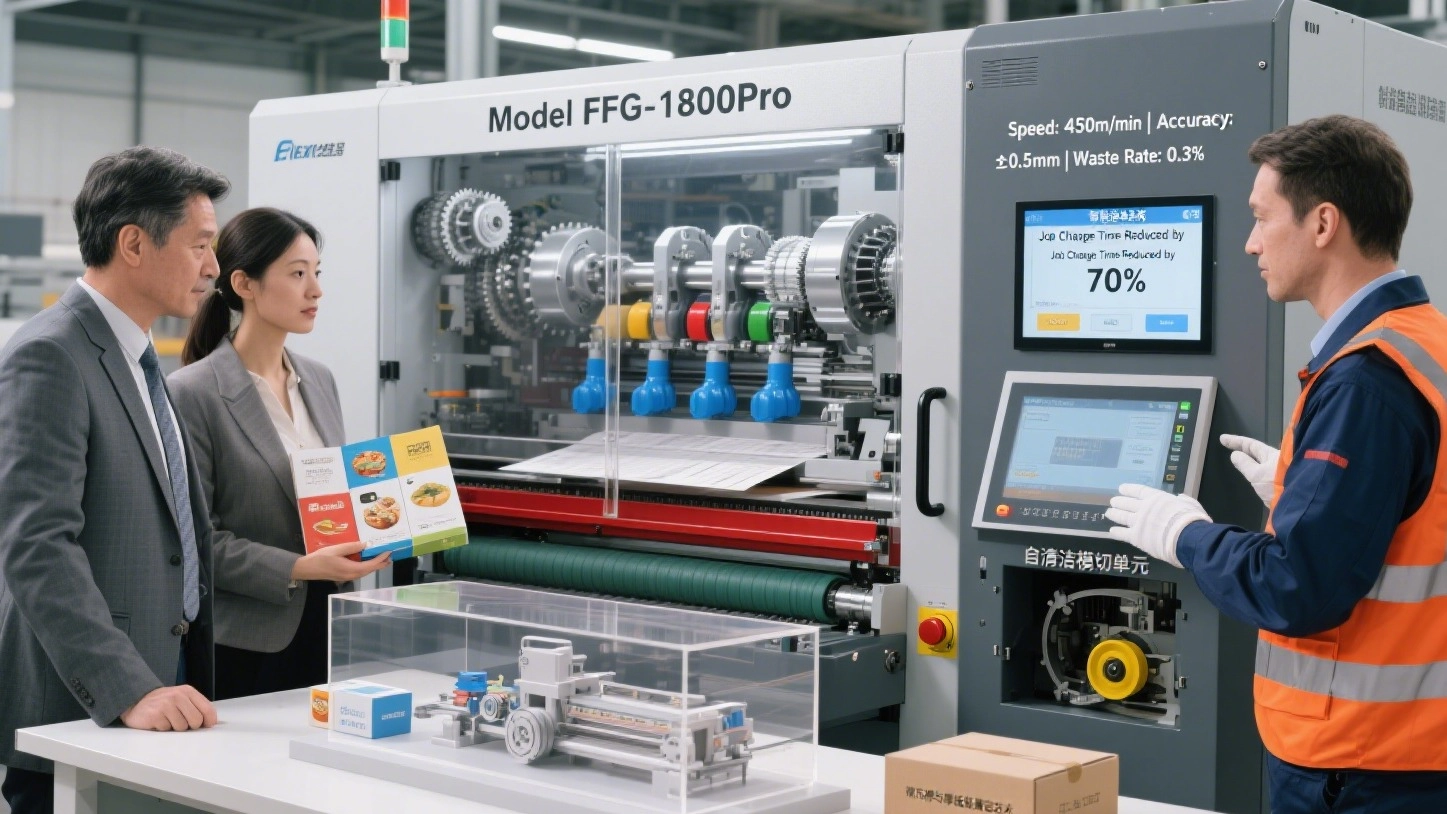
The Ultimate Guide to Flexo Folder Gluer Machines: How to Choose, Operate, and Maintain

Top Corrugated Box Printer Machine Brands
Product
What should I do if the machine jams during operation?
In case of a jam, immediately stop the machine, remove any obstructions, and check for any damage before restarting.
What materials are compatible with your folding carton machines?
Our machines are compatible with a wide range of materials including cardboard, corrugated board, and paperboard.
Shipping
What are the shipping costs for your folding carton machines?
Shipping costs depend on the destination, machine size, and shipping method. Contact us for a detailed quote.
Industry Solutions
How do your machines comply with industry standards and regulations?
Our machines are manufactured to meet or exceed industry standards and regulations, ensuring safe and compliant operation.
What kind of technical support do you offer for industry applications?
We provide comprehensive technical support, including installation, maintenance, and troubleshooting services.
Leave a message
Have any questions or queries about our products? Please leave us a message here and our team will get back to you promptly.
* Rest assured that your privacy is important to us, and all information provided will be handled with the utmost confidentiality.
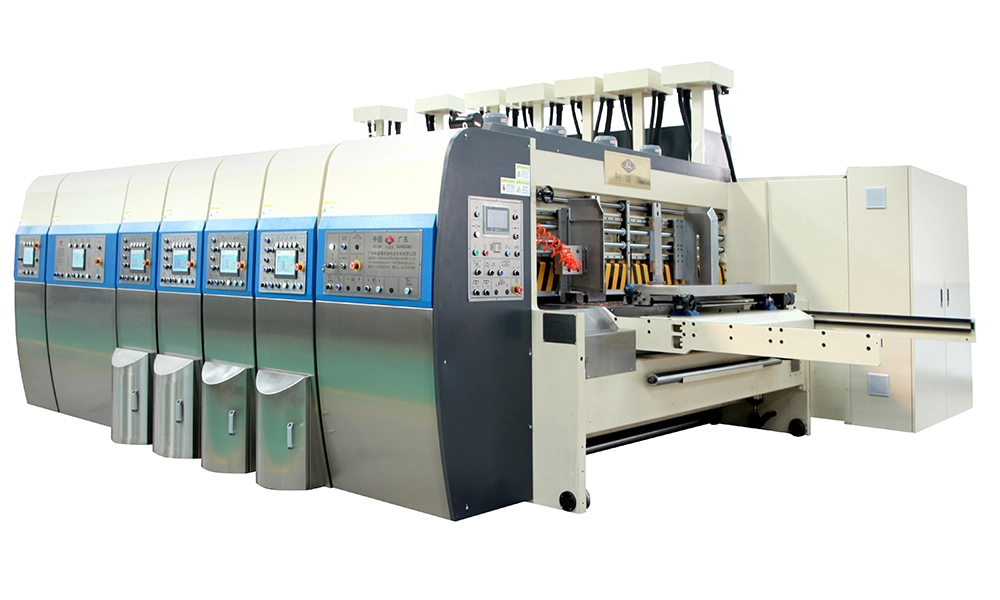
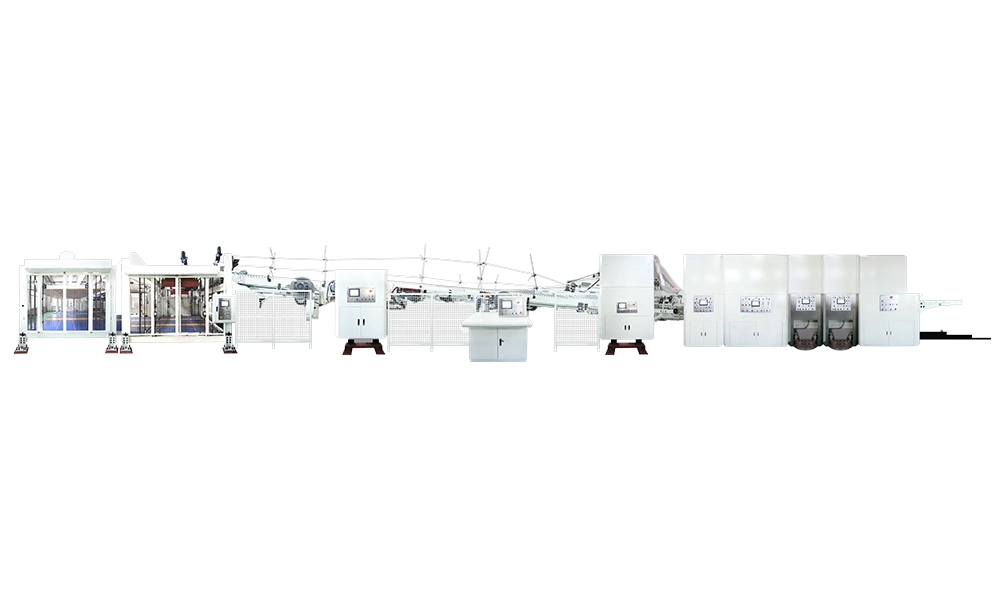
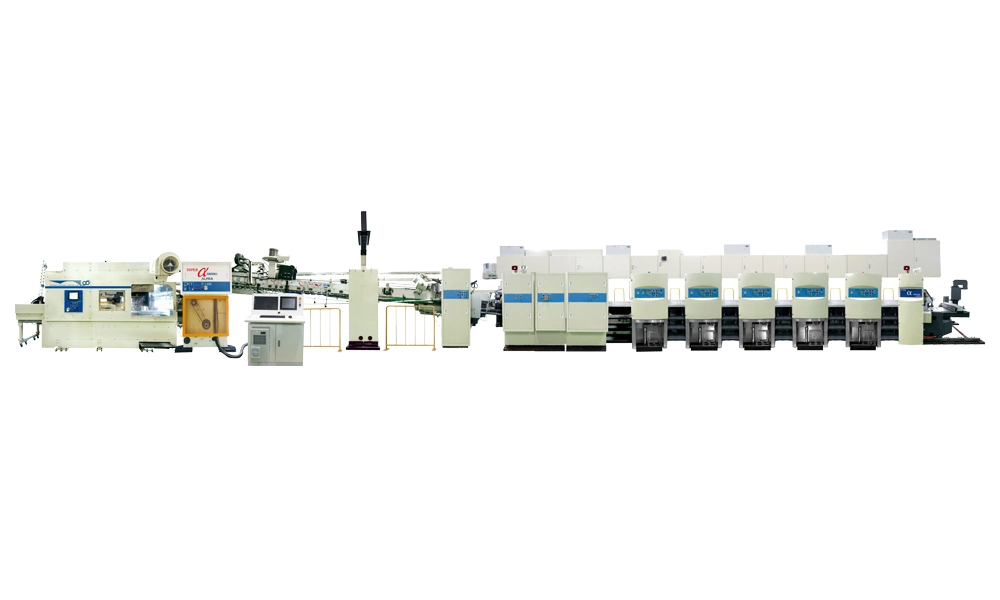
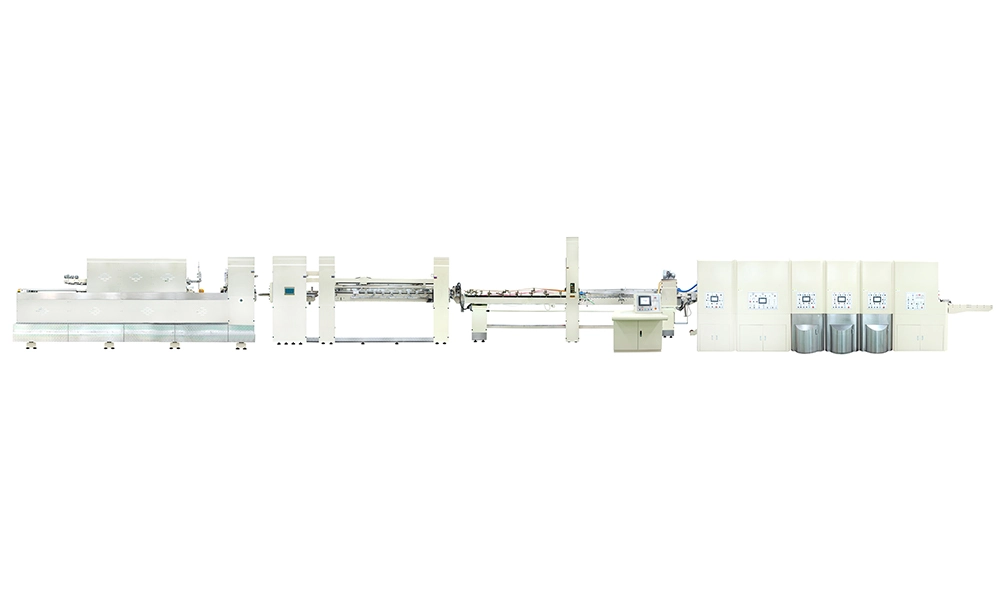
© 2025 Keshenglong & SHINKO All Rights Reserved.
Keshenglong Carton Packing Machine
Keshenglong Carton Packing Machine
Keshenglong Carton Packing Machine
Keshenglong Carton Packing Machine
Keshenglong Carton Packing Machine