What is the process of die cutting? | Keshenglong&Shinko Guide
Master the art of die cutting for your flexo printing needs! This guide covers die types (steel rule, magnetic, rotary), the cutting process, best practices, and common troubleshooting. Improve your quality & efficiency with Keshenglong&Shinko's expertise.
What is the Process of Die Cutting?
This article clarifies the die-cutting process crucial for flexo printing, addressing common questions and challenges faced by professionals. We'll cover the mechanics, types of dies, and best practices for optimal results.
Understanding Die Cutting in Flexographic Printing
* Definition: Die cutting is a crucial post-press process in flexographic printing that uses a precisely engineered steel rule die to cut, pierce, or emboss printed materials into desired shapes and sizes. It's essential for creating intricate shapes, labels, and packaging.
* Purpose: Die cutting separates printed sheets into individual pieces, creates custom shapes beyond what's possible with simple guillotining, and adds value through intricate designs and finishes.
* Importance in Flexo: Flexo printing often utilizes die cutting to produce complex, high-quality labels, packaging, and other products, requiring accurate and efficient cutting for optimal results.
Types of Die Cutting Dies
* Steel Rule Dies: The most common type, utilizing precisely shaped steel rules embedded in a resilient backing material. These are cost-effective and suitable for most applications.
* Magnetic Dies: Offer faster setup times and easier adjustments compared to steel rule dies, making them ideal for shorter runs and frequent design changes.
* Rotary Dies: Used for high-volume production, providing faster speeds and greater precision than flatbed dies. They are particularly suitable for continuous web processes.
The Die Cutting Process Step-by-Step
* Die Preparation: The die is carefully prepared and mounted onto a die-cutting press. This involves checking its alignment and ensuring smooth operation.
* Material Feeding: The printed substrate (e.g., paper, film, or other flexible material) is fed into the press, precisely aligned for accurate cutting.
* Cutting Action: The press applies pressure, forcing the material against the sharp edges of the die, cleanly cutting or embossing it.
* Waste Removal: The waste material (the cut-out pieces) is separated from the finished product, often through a stripping process.
* Quality Inspection: The cut pieces are visually inspected to check for any defects, ensuring accuracy and quality.
Best Practices for Optimal Die Cutting
* Die Design & Construction: Invest in well-designed and expertly constructed dies to minimize defects and maximize efficiency.
* Material Selection: Choose appropriate materials that are compatible with the die-cutting process and desired outcome. Consider material thickness and strength.
* Press Maintenance: Regularly maintain the die-cutting press to ensure optimal performance and prevent damage to the die or material.
* Operator Skill: Properly trained operators are crucial for achieving consistent and high-quality results.
Troubleshooting Common Issues
* Poor Cutting Quality: This could indicate dull blades, incorrect pressure settings, or improper material handling.
* Material Damage: Check for appropriate material compatibility and adjust pressure settings as needed.
Conclusion
Understanding the die-cutting process is essential for flexo printers seeking to achieve optimal quality and efficiency. By following best practices and addressing common issues, you can maximize productivity and deliver high-quality products.
Recommended for you
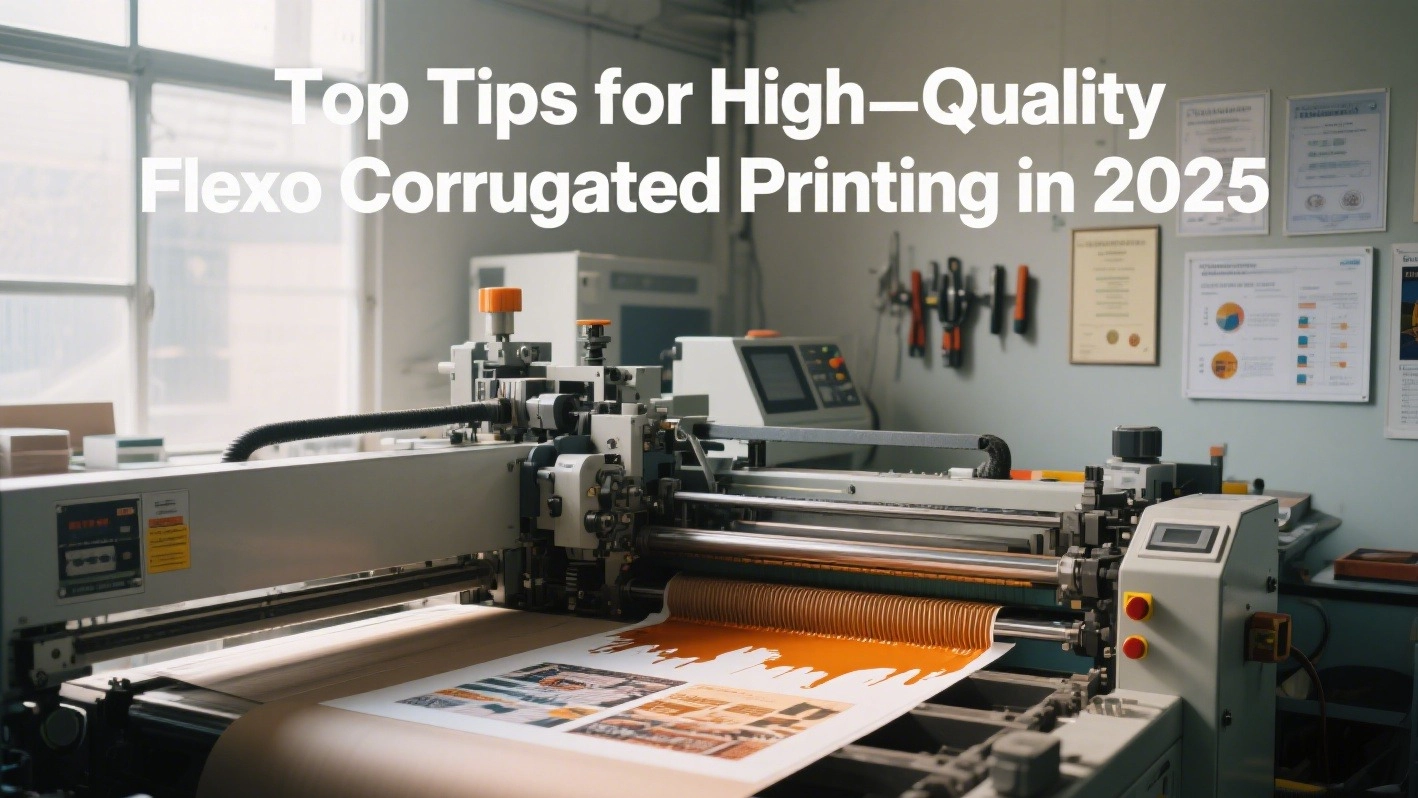
Top Tips for High‑Quality Flexo Corrugated Printing in 2025
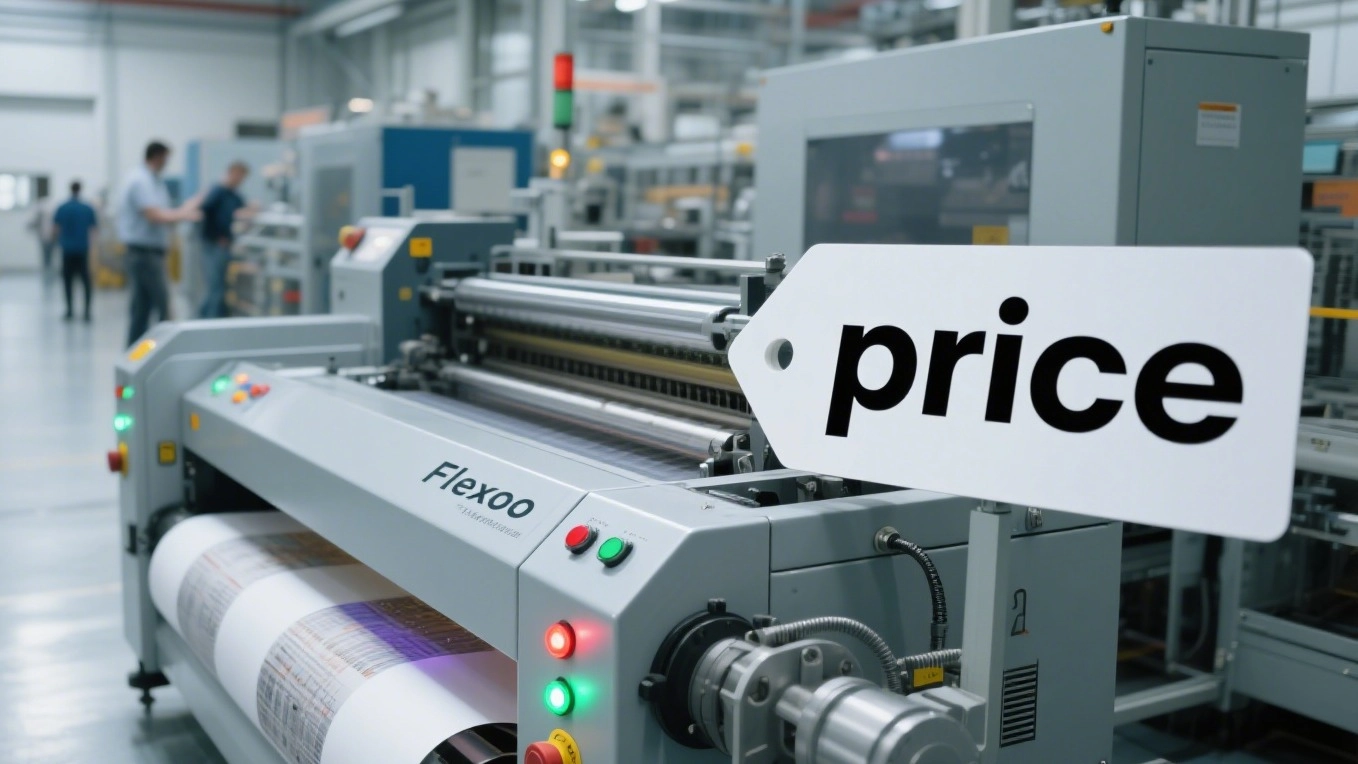
Flexo Printing Machine Price Guide 2025: What Buyers Should Know
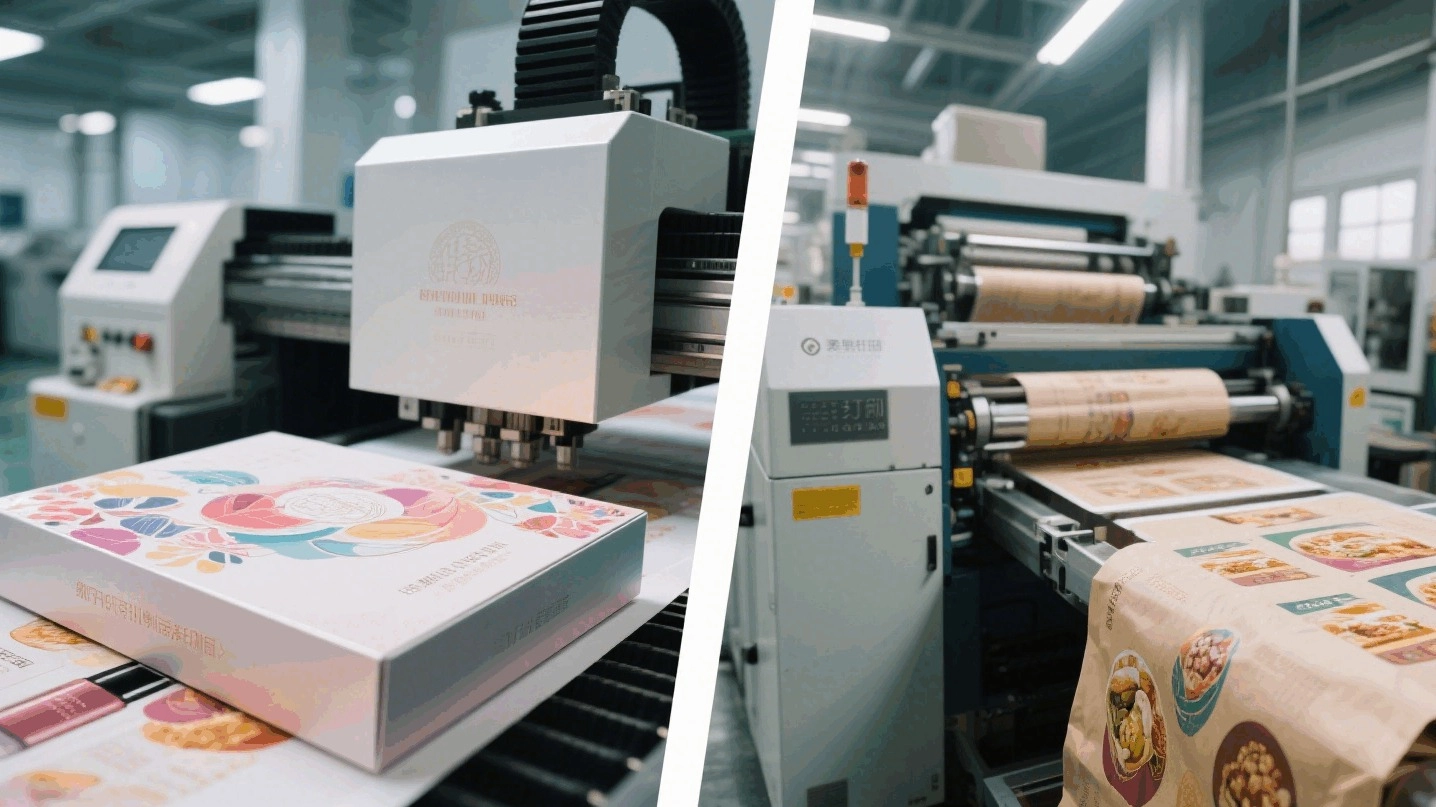
Digital vs Flexo Printing: Which Is Right for Your Packaging Business in 2025?
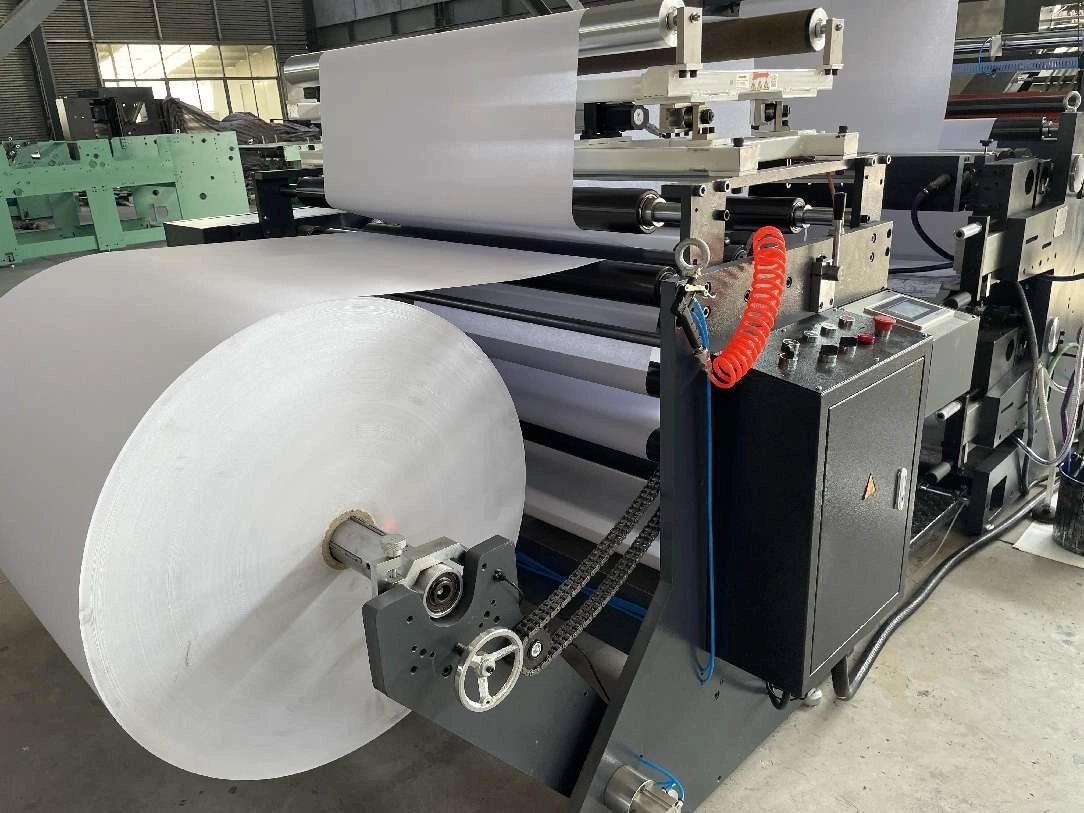
Top 6 Materials for Flexo Packaging: Choose the Best for Your Printing Line
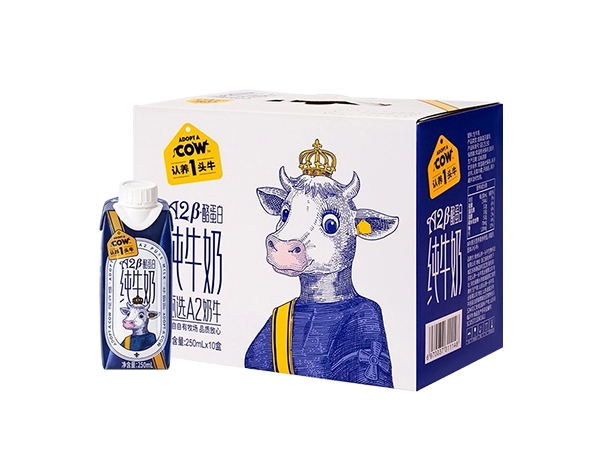
Flexo Printing on Corrugated Boxes: Ink Selection Guide
Product
How can I integrate your machines into my existing production line?
Our technical team can assist with integrating our machines into your current production setup, ensuring a seamless operation.
What should I do if the machine jams during operation?
In case of a jam, immediately stop the machine, remove any obstructions, and check for any damage before restarting.
Shipping
What is the estimated delivery time for your machines?
Delivery times vary based on location and order size, but we typically estimate 4-6 weeks for delivery.
Can you ship to remote or difficult-to-access locations?
Yes, we can arrange shipping to remote locations, though additional charges and time may apply.
Industry Solutions
How can your machines improve my production workflow?
By automating carton production, our machines streamline your workflow, increase output, and reduce downtime.
Leave a message
Have any questions or queries about our products? Please leave us a message here and our team will get back to you promptly.
* Rest assured that your privacy is important to us, and all information provided will be handled with the utmost confidentiality.
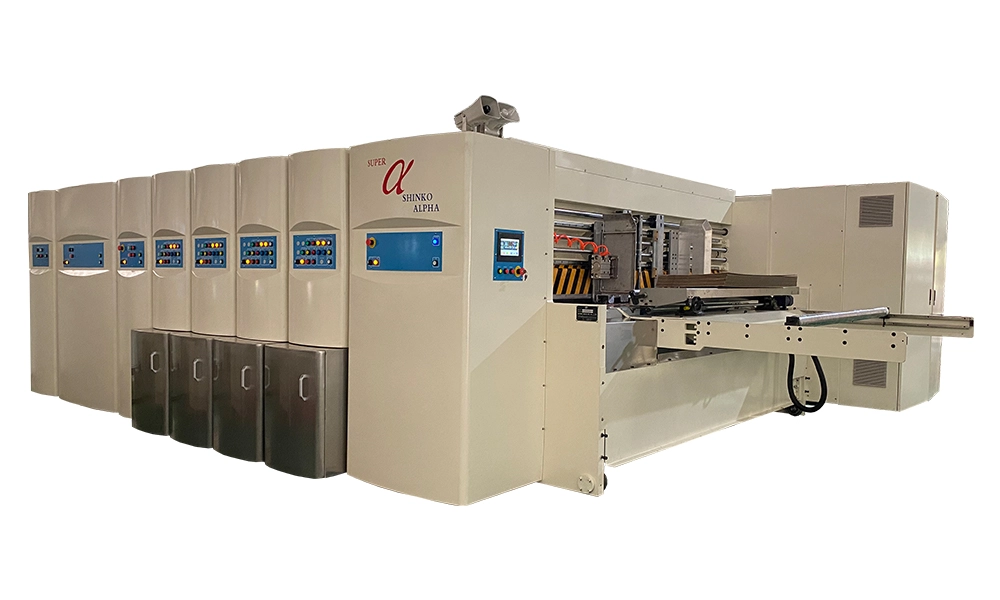
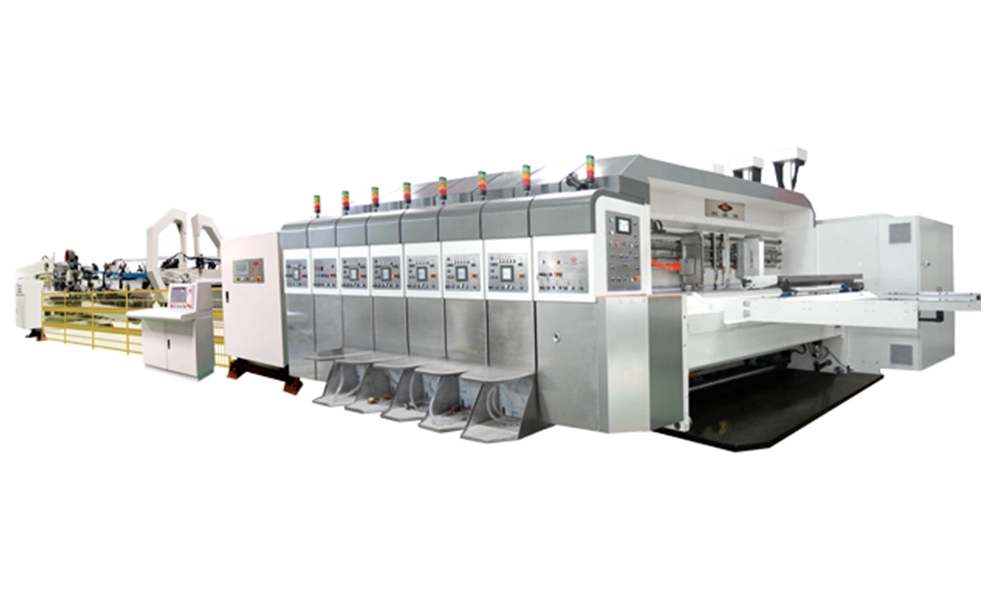
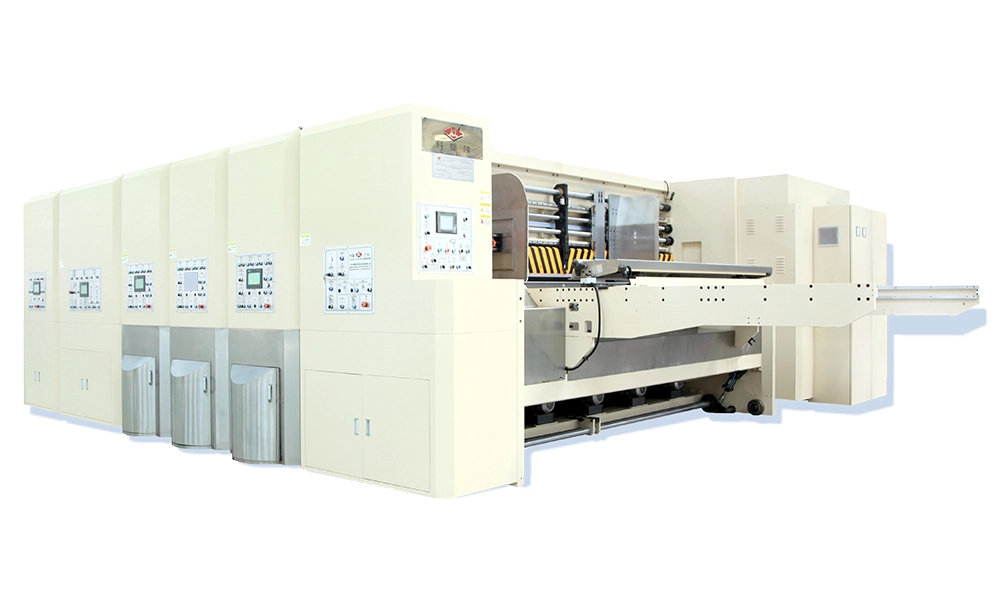
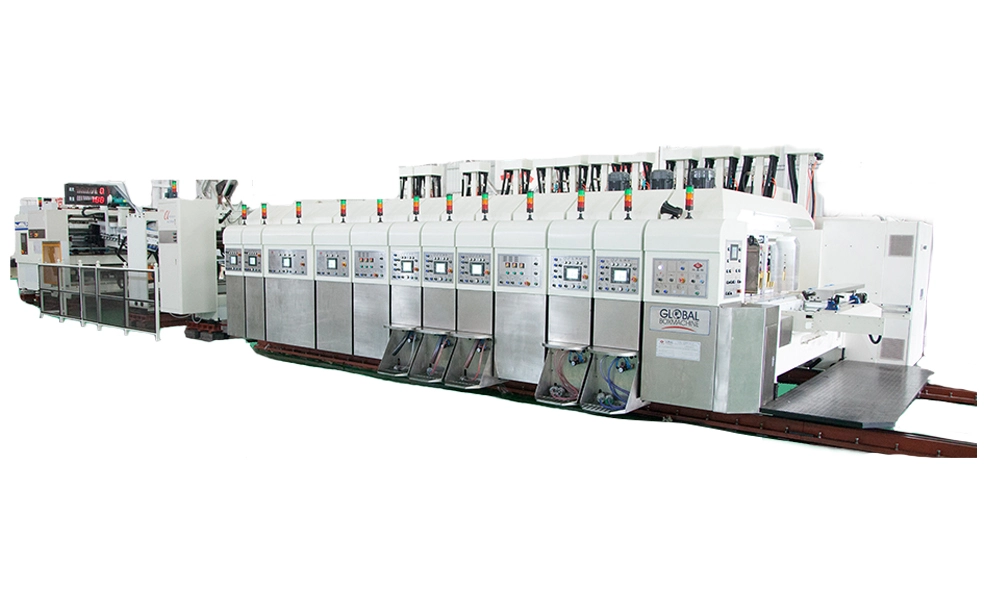
© 2025 Keshenglong & SHINKO All Rights Reserved.
Keshenglong Carton Packing Machine
Keshenglong Carton Packing Machine
Keshenglong Carton Packing Machine
Keshenglong Carton Packing Machine
Keshenglong Carton Packing Machine